- 2024/07/19
-
シャフト部品の熱処理完全ガイド|焼入れ・歪み・仕上げ対策まで徹底解説

シャフト部品は、回転機構や駆動系に欠かせない重要なパーツです。ただし、高い強度・耐摩耗性・寸法精度が求められることから「熱処理」が必要になります。また、焼入れや浸炭処理などの熱処理には、寸法変化や歪みといった課題もつきものです。精密シャフトでは、ミクロン単位の精度確保が製品機能に直結するため、適切な処理条件の設定や、加工後の補正・検査体制が重要です。
本記事では、シャフト熱処理の基本から処理方法の違い、精度維持の管理ポイント、材質ごとの選定方法まで網羅的に解説します。
目次 [hide]
シャフト部品における熱処理の役割とは?
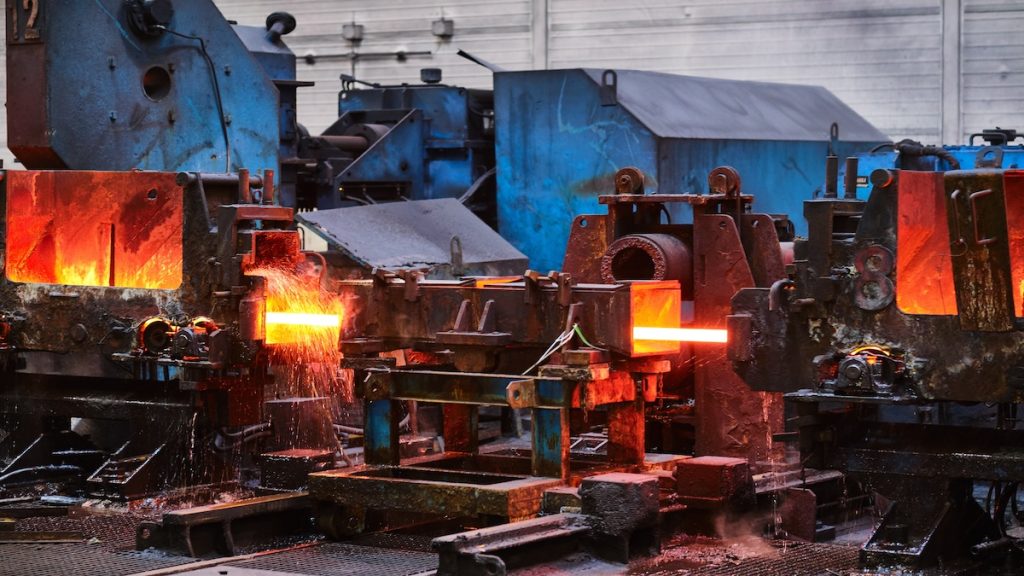
引用元:pixabay
シャフト部品は、回転運動や荷重の伝達を担う重要な機構部品です。軸受けやギアと組み合わせて使われることも多く、高速回転や高荷重、摩耗環境などにさらされるため、単なる加工だけでなく「熱処理」が必要不可欠です。熱処理により、シャフトの強度・耐摩耗性・靱性・寸法安定性が向上。長期使用における耐久性や精度保持にもつながります。
使用環境や機能に応じた強度・耐摩耗性が必要
シャフトはエンジンやモーター、ギア、センサーなど多様な装置で使用され、摩擦や衝撃、繰り返し荷重にさらされるため、素材そのままの状態では十分な耐久性を持ちません。摺動部や軸受部では、耐摩耗性と表面硬度が求められ、折損や変形を防ぐためには一定以上の引張強度も必要です。
こうした要件を満たすには、焼入れや浸炭処理などの熱処理を施すことが有効です。
熱処理により素材特性を最適化できる
熱処理は、材料の物理的特性や内部組織を制御する工程で、同じ材質でも処理方法次第で強度や靱性、硬度、寸法安定性を大きく変えることが可能です。たとえば、シャフトの表面を硬化させつつ芯部は粘りを持たせたい場合は、浸炭焼入れが適しています。
逆に、応力を抜いて変形しにくくしたい場合は焼なましや応力除去処理を施すことで、後工程の精度を高めることができます。
シャフト向けの代表的な熱処理の種類
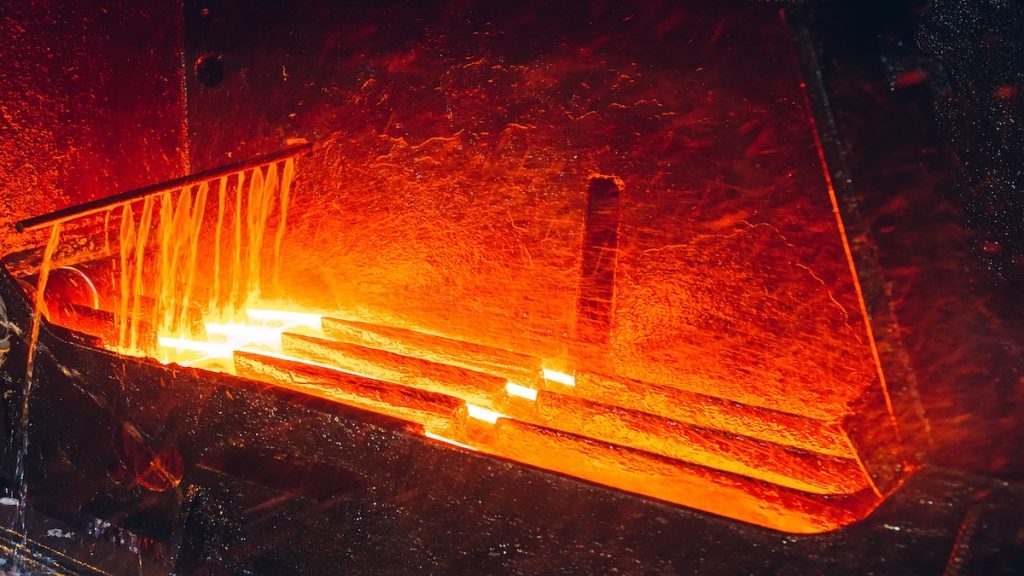
引用元:pixabay
シャフト部品に対しては、目的に応じたさまざまな熱処理が選択されます。ここでは、代表的な処理法とその特徴を紹介します。
焼入れ・焼戻し
シャフトの強度と硬度を同時に高めるために広く使われるのが焼入れと焼戻しです。焼入れは材料を高温加熱後に急冷し、硬化を促す処理であり、そのままだと脆くなるため、焼戻しで適度な靱性と応力緩和を与えます。主に合金鋼や炭素鋼に用いられ、回転軸や摺動軸など、衝撃と摩耗が繰り返される部位に適しています。
浸炭・窒化処理
シャフトの表面硬度だけを高めたい場合に有効なのが、浸炭処理や窒化処理です。浸炭処理は低炭素鋼の表面に炭素を浸透させた後に焼入れを行うことで、表層を硬化させる技術です。
一方、窒化処理は窒素を拡散させて硬質層を形成し、耐摩耗性・耐食性に優れた表面を実現します。浸炭処理や窒化処理は内部の靱性を保持しつつ、表面の強度を確保するのに適しています。
応力除去の処理
前加工(切削・研削など)で残留した内部応力があると、後の熱処理や使用中に歪みや変形が起きる原因になります。そのため、応力除去焼なましや時効処理をあらかじめ施すことがあります。
また熱処理中の歪みを抑え、後工程の精度安定性を高めることができます。高精度なシャフト製品では、応力除去の処理の有無が仕上がりを左右する重要ポイントです。
シャフト熱処理で発生しやすい課題

引用元:pixabay
熱処理はシャフト部品の性能向上に欠かせない反面、処理方法や条件の選定を誤ると、寸法精度や形状安定性に深刻な悪影響を及ぼす可能性があります。ミクロン単位の精度が要求される精密シャフトでは、些細な歪みや変形が機能不良に直結するため、熱処理設計と工程管理には高度な技術と知見が求められます。
ここからは、現場でよく問題となる典型的な課題について詳しくみていきましょう。
寸法変化・歪みのリスクがある
シャフトに熱処理を施す際、材料は加熱による膨張と冷却による収縮を繰り返します。マルテンサイト変態のような相変態が起きると体積が変化し、これによって微細な寸法ズレや形状歪みが発生。また、前加工で生じた残留応力が熱処理により再分布することで、設計意図とは異なる挙動を示すケースもあります。
たとえば全長100mmのシャフトであっても、0.01〜0.05mmの変化が起きることは珍しくありません。寸法変化は製品機能や嵌合精度に影響を与えるため、あらかじめ補正設計や後工程での精密仕上げを計画する必要があります。
反り・ねじれによる同軸度不良が起きる
シャフトは長さ方向に細長いため、熱処理時の温度分布が不均一になると、わずかな差でも反りやねじれにつながります。左右非対称な断面形状や偏肉構造の場合、熱伝導性や冷却速度の差が生じやすく、これが応力の偏りや変形の原因になります。
反りやねじれは、回転精度や摺動部の摩耗寿命に大きく影響を与えるため、冶具設計による固定と支持、加熱・冷却の均一化が欠かせません。冷却方法の工夫として、油冷から空冷へ切り替えるのも一つの方法です。
表面硬化と内部組織のバランスの考慮が必要
浸炭や窒化などの表面硬化処理では、外層が高硬度化し、内部は比較的靱性を保ったままになります。性質に違いがあると、使用中に応力が集中しやすく、クラックや破損の起点になるリスクが高まりやすくなるでしょう。
温度・時間・深さといった処理条件が適切でない場合、硬化層の割れや剥離が起きることもあります。これらを防ぐには、処理深さ・硬度分布のシミュレーションや事前評価、実機使用条件を想定した材質選定が重要です。実際の使用負荷に耐えうる構造設計と処理設計の両立が、信頼性の高いシャフトづくりに直結します。
熱処理後のシャフト精度を守るための管理ポイント

引用元:pixabay
熱処理によってシャフトに必要な強度や硬度を確保できたとしても、その過程で寸法や形状の精度が損なわれてしまえば、最終製品としての品質が担保されません。特に精密シャフトでは、ミクロン単位での管理が要求される場面もあり、熱処理後の精度確認と補正工程は不可欠です。
次に、シャフト精度を確実に保つために実施すべき管理ポイントを解説します。
真円度・同軸度を測定する
シャフトの基本性能である真円度・同軸度は、回転精度や摺動性能に直結する極めて重要な品質特性です。熱処理による歪みや寸法変化によって、精度が大きく損なわれることがあります。そのため、処理後には必ず専用の測定機器を用いた再評価が必要です。
三次元測定機や真円度測定器、プロファイル測定器、光学式センサーなどを活用し、規定公差内で収まっているか確認することが重要。測定結果は仕上げ工程や熱処理条件の見直しにも活かされ、全体の工程品質を高める重要なフィードバック源となります。
仕上げ研磨・切削で精度を補正する
熱処理後にわずかでも寸法や形状が変化してしまった場合、それを補正する仕上げ工程が不可欠です。具体的にはセンタレス研磨や円筒研削、内径研削、表面仕上げ切削などを通じて、必要な寸法精度や表面粗さに仕上げます。
嵌合部やベアリング接触面、摺動部など、高精度な嵌め合いが要求される箇所では、μm単位の取り代調整が必要になることもあるでしょう。取り代の設計や砥石・工具の選定、機械剛性の確保、温度管理など、各要素を一貫して最適化することで、加工後のばらつきを抑えやすくなります。
検査・トレーサビリティを実施する
シャフトの品質を安定して保つには、最終検査体制の整備と、製造履歴の見える化が欠かせません。寸法・形状測定だけでなく、硬度や表面粗さ、マイクロ構造など多角的な検査を行うことで、製品の適合性を総合的に評価できます。
また、誰が・いつ・どの工程で加工・検査を実施したかを記録・管理するトレーサビリティ体制を整えておくことで、万が一の不良時にも迅速な原因追究と対策が可能です。クライアントの信頼確保やクレームリスク低減にも貢献することでしょう。
熱処理後の精度維持は、「測定」「補正加工」「検査・履歴管理」の三位一体の取り組みが不可欠であり、それぞれの工程に対する高度な管理技術と現場対応力が求められます。
材質ごとに異なるシャフト熱処理の選び方

引用元:pixabay
シャフトの材質によって、適用可能な熱処理方法や処理条件は異なります。ここでは代表的な材質ごとの熱処理対応を紹介します。
SUS(ステンレス)シャフトの場合
ステンレスは耐食性に優れる一方で、炭素鋼と比べて熱伝導性が低く、熱処理の難易度がやや高い傾向にあります。SUS420などのマルテンサイト系ステンレスは焼入れ可能で、高硬度・耐摩耗性を持たせることができますが、変形にも注意が必要です。
SUS304などオーステナイト系は基本的に焼入れできず、加工硬化や冷間加工で硬さを持たせるケースが一般的です。
SCM・SKなど合金鋼シャフトの場合
SCM(クロモリ鋼)やSK(工具鋼)は、熱処理性がよいのが特徴です。焼入れや焼戻しによって高い硬度と靱性の両立が可能になります。SCM440は、自動車や産業機械のシャフトに多用される材料で、焼入れ後に精密研削を行うことで、耐久性と寸法安定性を実現できます。
真鍮・アルミ等の非鉄シャフトの場合
非鉄金属は基本的に焼入れが不要または不可能です。しかし冷間加工による強度付与や、時効硬化処理(アルミ合金など)によって特性を引き出すことができます。熱処理の代わりに、アルマイトや無電解Niメッキといった表面処理で耐摩耗性や耐食性を補うことが多いです。
加工事例 熱処理 円筒研磨製品

写真の製品は円筒研磨をしている製品です シャフトの加工には欠かせない研磨です 特に弊社では熱処理などの処理のあとに 社内で歪をとる矯正を実施した後に円筒研磨をすることにより 削り量の削減、精度の向上を得意としております 熱処理後の研磨にもしお困りでしたら一度相談していただけたらと思います
加工事例 熱処理 センタレス研磨製品

写真の製品は 熱処理センタレス研磨を実施している製品です センタレス研磨を選択する理由は センタ穴がなくて円筒研磨ができない 量がたくさんあって困っている時に選ばれているかと思います 同軸、真円などは素材に倣ってしまう傾向が強いので 曲がりや歪が大きいと加工ができない可能性があります ただ加工が可能であれば円筒研磨に比べれば圧倒的なコストメリット 量の確保が可能です 切削で厳しい公差をできるだけ安く研磨に変えたい 円筒研磨では時間が掛かりすぎるといった方は一度ご相談していただければと思います
シャフトの熱処理に関するよくある質問
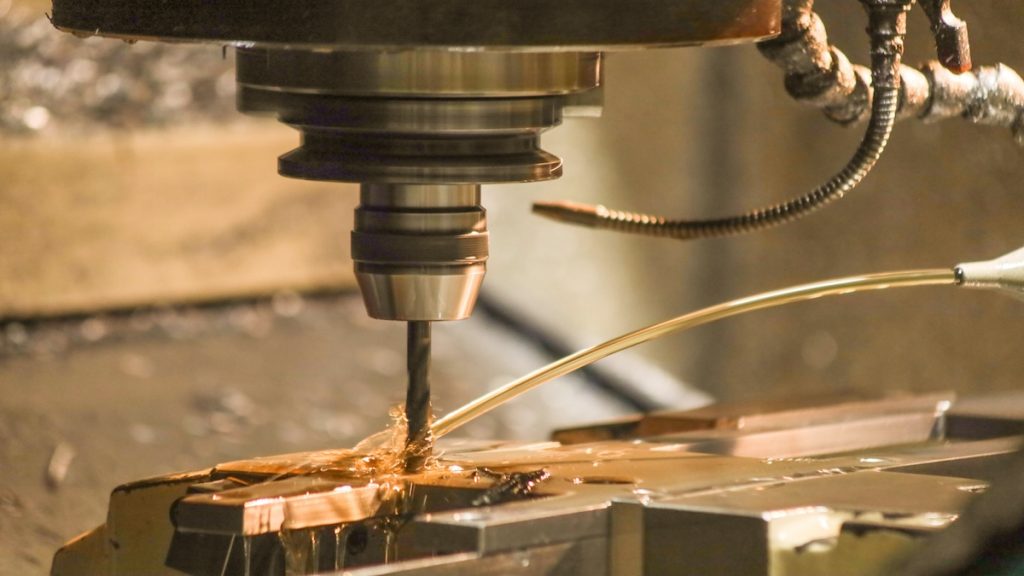
引用元:pixabay
Q. 熱処理による寸法変化はどれくらい見込むべき?
材料や処理条件によりますが、一般的には0.01~0.1mm程度の寸法変化が生じる場合があります。高精度なシャフトでは、熱処理後に再研削を前提とした加工設計が推奨されます。
Q. シャフトの硬度はどの程度まで上げられる?
合金鋼や工具鋼などの焼入れ材では、HRC55〜65程度の硬度が可能です。ただし、硬度を上げすぎると脆性が高まり、破損リスクも増えるため、使用環境や荷重条件を考慮したバランス設計が必要です。
Q. 精度と強度の両立はどう考えるべき?
熱処理で強度を高めると、どうしても歪みや寸法変化が避けられません。そのため、仕上げ加工を後工程に回し、熱処理後に必要な精度を補正するのが一般的です。工程全体での設計が重要になります。
まとめ
シャフト部品における熱処理は、強度・耐摩耗性・靱性の確保において不可欠な工程です。一方で、寸法変化や歪みといった課題も伴うため、材質ごとの適切な処理選定と、熱処理後の精度管理・補正体制が求められます。
日興精機では、シャフトの素材選定から熱処理、仕上げ研磨、検査までを一貫して対応し、高精度・高耐久なシャフト製品を安定供給しています。シャフト部品の熱処理に関する疑問を抱える方は、ぜひ一度ご相談ください。
お問い合わせ
弊社製品、加工についてのお問い合わせは、こちらで受付しております。
各部門のスペシャリストが、ご質問にお応えします。
電話
0574-54-2231
(平日 8:15~17:15)
FAX
0574-54-2235