- 2024/04/11
-
センタレス研磨と円筒研磨の違いと方法・メリットデメリット
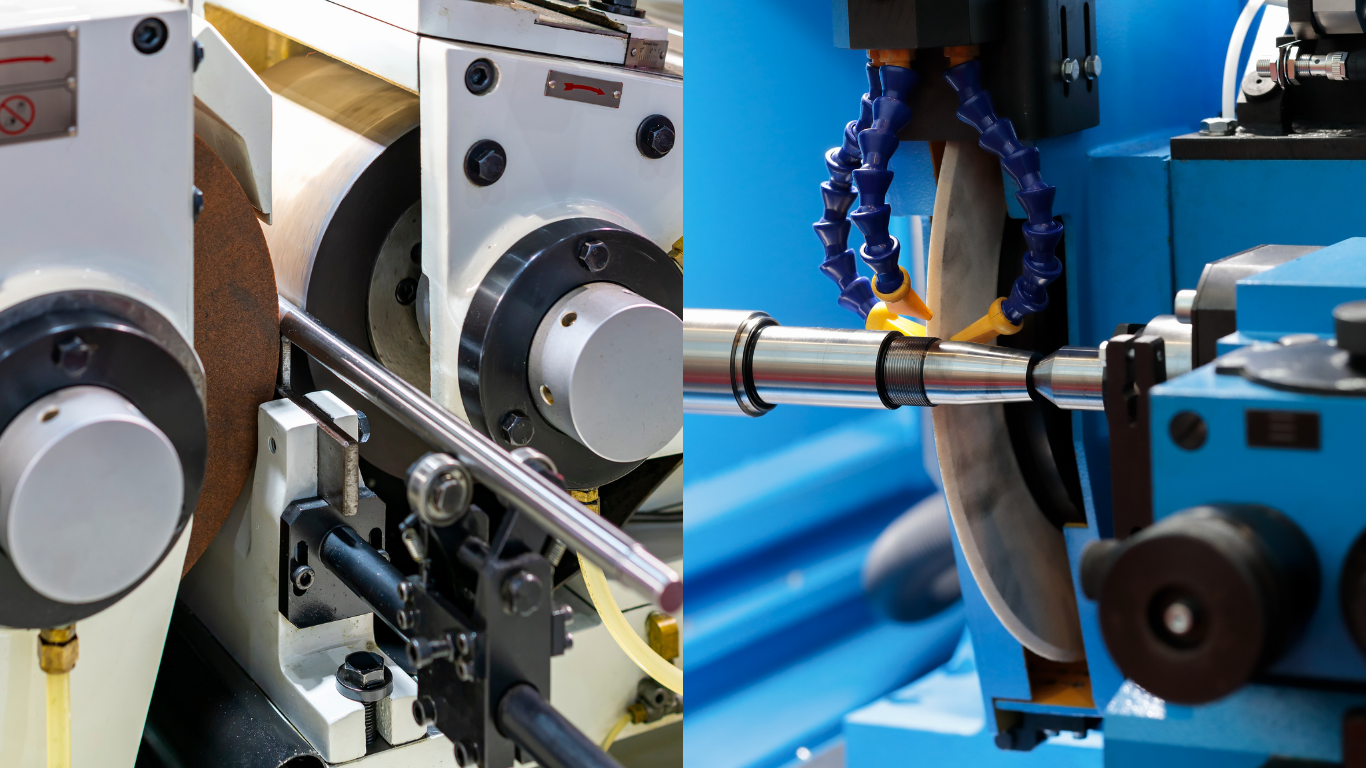
センタレス研磨と円筒研磨。この2つの精密加工技術は、見た目以上に異なる特性と用途を持っています。
本記事では、センタレス切削と円筒研磨の基礎から、具体的な研削方法、使用ポイント、メンテナンスのことまで包括的に解説します。
効率的かつ高品質な加工を目指すための知識を一緒に深めていきましょう。
目次 [hide]
センタレス切削と円筒研磨とは
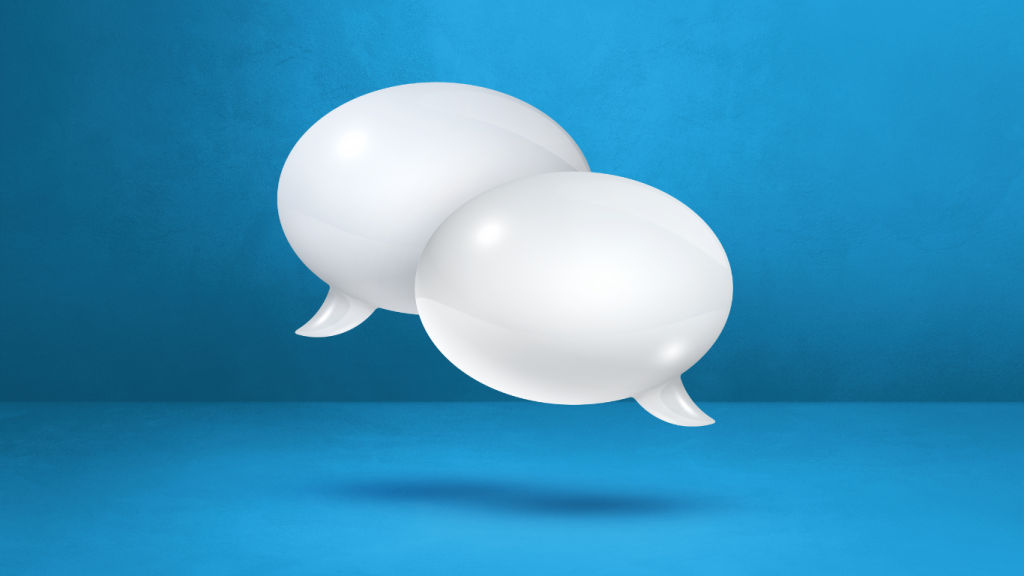
センタレス切削と円筒研磨は、金属部品の仕上げにおいて、よく使われる二つの技術です。それぞれ異なる方法を用いて、部品の形状を正確にする役割を果たします。
センタレス切削
センタレス切削は、金属部品を固定せずに切削する方法です。この技術は、高速かつ高精度で大量生産に適しています。ワークは、回転する2つのホイールの間に置かれ、それにより加工されます。切削精度が高いことから、自動車部品や精密機械の製造に多用されます。
センタレス切削のもう一つの特徴は、省スペースであることです。固定装置が不要なため、作業スペースがコンパクトに収まります。また、切削中に発生する熱も少なく、加工物の品質を保持することができます。そのため、高温に弱い材料の加工にも適しています。
この技術は、生産効率を向上させるための重要な要素です。短い時間で大量のワークを処理できるため、コスト削減にも寄与します。その結果、多くの産業で広く利用されています。
円筒研磨
円筒研磨は、ワークを回転させながら表面を研磨する技術です。一般的には、ワークを固定し、研磨ホイールで表面を削りながら仕上げていきます。円筒研磨によって、非常に滑らかな表面仕上げが可能になります。主に、シャフトやローラーなどの円筒形部品に用いられます。
この方法は、高精度と高品質を要求される部品の製造に向いています。例えば、ベアリングや精密機器のパーツなどです。研磨後の仕上げ精度が高いことで、部品の耐久性や性能も向上します。
また、円筒研磨は、異なる材料に対しても適用可能です。ステンレスやアルミニウムなど、さまざまな金属を研磨することができます。さらに、作業効率も良いため、量産にも対応できる点が評価されています。
センタレス切削と円筒研磨の違い
センタレス研磨と円筒研磨は、どちらも工業用の精密研磨方法ですが、加工方法や適用範囲において異なる特徴があります。
- センタレス研磨:
- センター支持不要: 被削材をセンタで固定することなく、研削砥石と調整砥石(レギュレーティングホイール)によって支持し、研削します。
- 高速・高効率: センタレス研磨は設定時間が少なく、高速で連続的な生産が可能です。
- 形状の制限: 主に直線形状の被削材に適しており、複雑な形状や非常に短い部品、極端に薄い部品の加工には向いていません。
- 円筒研磨:
- センター支持が必要: 被削材を機械のセンターに固定して研磨します。
- 精度の高さ: センター支持により、被削材が安定し、高精度の加工が可能です。
- 柔軟性のある加工: 内研磨、外研磨、面研磨など、さまざまな研磨が可能ですが、セットアップや調整に時間がかかります。
要するに、センタレス研磨は高速で効率的な生産を求める場合に適している一方で、円筒研磨は高精度が要求される多様な形状の加工に対応可能です。
円筒研削盤の研削方法
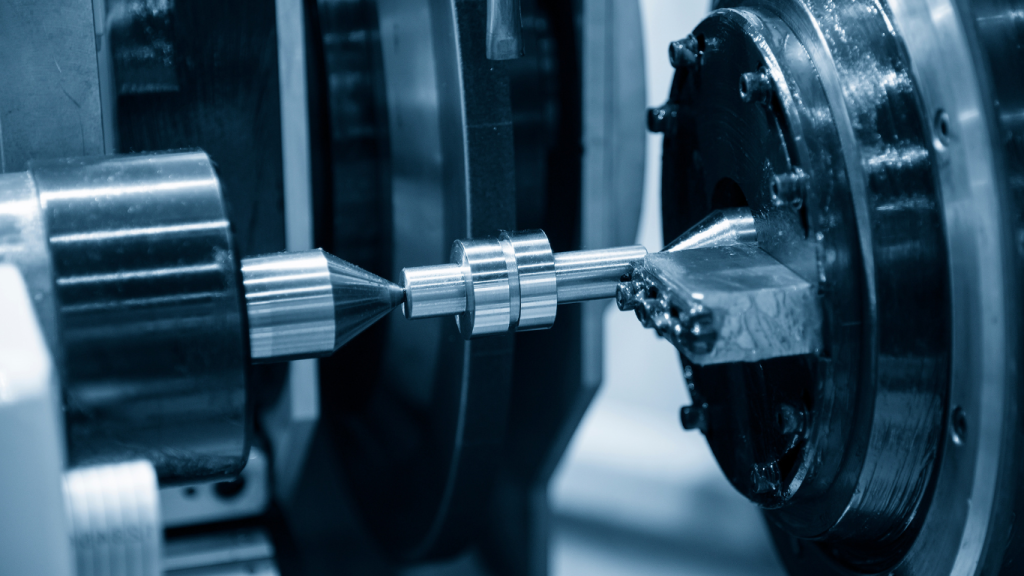
円筒研削盤は、精密な円筒形状を実現するための重要な工作機械です。この機械を使用することで、表面の粗さや形状誤差を最小限に抑えることができます。
円筒研削には、さまざまな方法があり、適切な方法を選ぶことが重要です。主にアンギュラ研削、プランジ研削、トラバース研削の3種類が一般的です。それぞれの研削方法には特徴と利点があり、用途に応じて使い分けます。
アンギュラ研削
アンギュラ研削は、斜めに配置された工具と工件を使って行う研削方法です。この方法では、主に斜面やテーパーを加工することができます。特徴としては、高精度の斜面加工を可能にする点です。
第一に、安定した工具配置が求められます。次に、適切な研削液を使用することで、工具の摩耗を抑え、成果を向上させることができます。さらに、加工条件を最適化することで、高品質な仕上がりを実現します。
一方で、設定や調整が複雑であるため、経験と技術が必要です。効率的に作業を進めるためには、機械の特性を理解し、適切なメンテナンスを行うことも重要です。また、研削中の振動を最小限に抑えるため、機械の安定性が求められます。
プランジ研削
プランジ研削は、円筒研削盤において、工具を工件に直接進めることで行う方法です。この手法は、深い溝や特定の形状を一度に加工する際に便利です。特徴として、短時間で高い精度を実現できる点が挙げられます。適切な工具選びと、進入速度の調整が肝心です。
さらに、工件の保持方法や工具の設定が重要な要素です。この方法では、工件の寸法変化を最小限に抑えることが可能です。例えば、工具が工件に対して垂直に設定されるとき、最も効果的な研削が行えます。一方、誤った設定では工具が過度に摩耗するリスクもあります。
プランジ研削を成功させるためには、定期的な工具の点検とメンテナンスが必要です。特に、摩耗具合のチェックを怠らないことが重要です。また、加工中に適切な冷却液を使用することで、工具の寿命を延ばすことができます。
トラバース研削
トラバース研削は、工具を横方向に動かしながら工件を研削する方法です。この手法は、長いものや広い面積を均一に仕上げる場合に適しています。小刻みに動かすことで高い精度を保ち、均一な仕上がりを実現します。工具と工件の接触面を広く保ち、効率的に研削を行うためです。
まず、適切な工具配置と進行速度が重要です。次に、研削液の使用で摩擦熱を抑え、工具の寿命を延ばします。最後に、機械の定期的なメンテナンスも欠かせません。この方法は、一定のリズムで行うことで、最も効果的に機能するのです。
一方、適切な研削条件を設定することが求められます。不適切な設定では、研削面にムラが生じるリスクがあります。また、振動や騒音に注意を払い、安定した運転を心がけることが重要です。このため、トラバース研削を行う際には、経験と注意が必要です。
アンギュラ研削、プランジ研削、トラバース研削の違い
以下は、アンギュラ研削、プランジ研削、トラバース研削の違いを表にしています。
方法 | 説明 | 適用例 | 精度 | 効率 |
---|---|---|---|---|
アンギュラ研削 | 研削砥石を被削材に対して角度をつけて設定し、端面と外径を同時に研削する方法。 | 複雑な形状の部品の研削に適している。 | 高いが、設定や砥石の角度に依存。 | 中程度で、一回のパスで複数の面を仕上げることが可能。 |
プランジ研削 | 研削砥石を被削材に対してラジアル方向に進め、被削材は固定されたまま研削する方法。 | 短い精密部品や、同様の部品のバッチ生産に最適。 | 非常に高い、接触面積が大きいため。 | 直接かつ強力な研削力により高い。 |
トラバース研削 | 研削砥石の下で被削材を左右に動かしながら研削する方法。長い円筒形の表面を均一に仕上げることができる。 | 長い、直線的な部品、例えばシャフトや長棒の加工に適している。 | 中から高い、作業物の長さにわたって一貫性が保たれる。 | 中程度、作業物を繰り返し通過させる必要があるため。 |
円筒研削盤の使い方ポイント
円筒研削盤を使用する際の主なポイントは以下の通りです:
- セットアップの精度:
- 被削材のセットアップ時には、正確なセンタリングと固定が必要です。特に被削材の両端がしっかりとセンタに合っているか、またはチャックで確実に固定されているかを確認します。
- 砥石の選定と調整:
- 加工する材料や仕上げたい表面品質に応じて、適切な砥石(硬度、粒度、結合剤のタイプ)を選びます。また、使用前に砥石のドレッシング(形状修正と再研磨)を行い、最適な切削性能を確保します。
- 切込みと送り速度の調整:
- 研削の切込み量と送り速度は、被削材の材質や必要な加工精度に基づいて慎重に設定します。適切な設定により、過剰な熱発生を避け、研削精度を保つことができます。
- 冷却液の使用:
- 研削時には適切な冷却液を用いて、摩擦熱による被削材や砥石の損傷を防ぎます。冷却液は、適切な流量と圧力で供給することが重要です。
- スパークアウトの活用:
- 研削の最終段階でスパークアウトを行い、余分な材料を除去して仕上げ精度を向上させます。これにより、表面の微細な不均一を取り除き、仕上がりの品質を高めることができます。
- 安全管理:
- 研削盤の操作中は、安全装置が正しく機能しているかを常にチェックし、操作者の保護具(保護メガネ、手袋、防音耳栓など)の着用を徹底します。
センタレス切削の研削方法
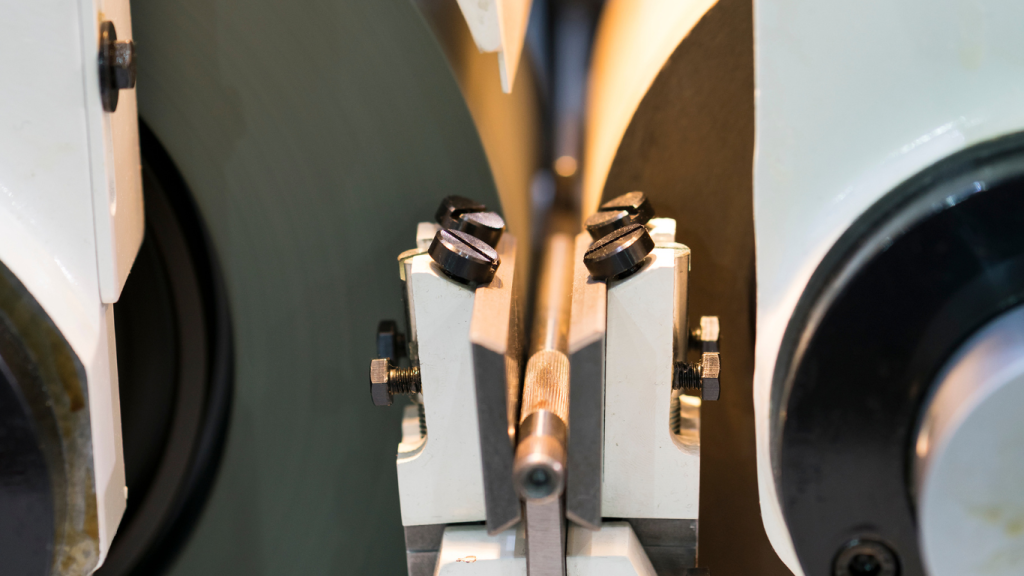
センタレス切削は、従来のセンタ付け方式よりも効率的に研削できる方法です。この方法は、通常の加工方法に比べて高い生産効率を持ち、特に大量生産に向いています。
センタレス切削では、チャックやセンターを使用せず、ワークピースをローラーと研削砥石の間に挟み込むことで研削を行います。この方法により、高い寸法精度と表面仕上げが実現可能です。また、簡単に機械設定ができるため、操作性も優れています。
スルーフィード研削
スルーフィード研削は、センタレス研削の中でも、連続的にワークピースを供給しながら加工する方法です。この方法では、ワークピースが研削機を通過する際に一定の速度で送り込まれ、連続して切削が行われます。そのため、生産効率が非常に高くなります。
スルーフィード研削では、ワークピースの形状や材質に応じた最適な設定が必要です。また、加工中の温度管理も重要なポイントです。過熱を避けるために、冷却液を使用することが一般的です。
この方法は特に長尺物や大量生産に向いており、効率的に高精度な研削が可能です。ただし、設定や管理を適切に行わないと、ワークピースの品質に影響が出ることがあるため、注意が必要です。
インフィード研削
インフィード研削は、特定の形状や部分を精密に研削するためのセンタレス研削方法です。この方法では、ワークピースは固定され、砥石がワークピースに向かって送り込まれます。
インフィード研削は、外径や特定の部分のみを精密に加工することができ、多様な形状のワークピースに対応できます。例えば、段付きシャフトや複雑な形状の加工に向いています。そして、工具の設定や調整は複雑ですが、高い精度と仕上げ品質を実現します。
また、この方法では加工途中の微調整が可能で、繊細な加工が求められる場合に適しています。ただし、生産効率はスルーフィード研削に比べてやや劣ります。
スルーフィード研削、インフィード研削の違い
以下はスルーフィード研削とインフィード研削の特徴を比較した表です:
特性 | スルーフィード研削 | インフィード研削 |
---|---|---|
研削方法 | 被削材が一方向に連続して流れる | 被削材を一箇所で停止し、局所的に研削 |
生産効率 | 高い(連続加工により高速生産可能) | 低い(部品ごとにセットアップが必要) |
適用形状 | 長尺で直径が一定の単純形状 | 形状が複雑で短い部品、テーパー・段付き部品 |
精度 | 相対的に低い(長尺部品のたわみ影響) | 高い(局所的な精密加工が可能) |
部品サイズ | 大きいサイズでも対応可能 | 主に小さいサイズに適している |
設定変更の容易さ | 容易(同じサイズの連続加工が可能) | 困難(部品ごとに調整が必要) |
センタレス切削の使い方ポイン
以下はセンタレス切削を最大限に活用するための主なポイントです:
- 適切なセットアップ:
- ブレードの位置調整:ブレード(支持刃)は被削材を正確に支持し、調整砥石と研削砥石の間で適切に位置づける必要があります。
- 調整砥石の設定:調整砥石(調整車)は、研削時の被削材の位置と送り角度を調整するために用います。砥石の傾斜を調整して、被削材に適切な推進力を与えます。
- 砥石の選定と管理:
- 砥石の種類と粒度:被削材の材質や仕上がりの要求に応じて、適切な砥石を選択します。硬い材料や精密な仕上がりを求める場合には、硬度や粒度が異なる砥石が必要です。
- 砥石のドレッシング:砥石の表面を定期的に整える(ドレッシング)ことで、切削能力を維持し、品質を一定に保ちます。
- 被削材の供給:
- 連続供給の確保:スルーフィード研削の場合、被削材は砥石間を連続的に流れるため、供給システムがスムーズに機能することが重要です。
- 正確な送り速度:被削材の送り速度を適切に設定することが、研削の品質と生産効率に直結します。
- 冷却液の使用:
- 適切な冷却:研削プロセス中に発生する熱を効果的に管理するために、適切な冷却液を使用し、適切な流量と圧力で供給します。
- プロセスのモニタリングとトラブルシューティング:
- 品質のモニタリング:研削過程を定期的に監視し、仕上がりの品質や砥石の状態、機械の挙動に異常がないかチェックします。
- 問題の迅速な対応:問題が発生した場合は、迅速に原因を特定し、必要な調整や修理を行います。
センタレス切削と円筒研磨のメリットとデメリット
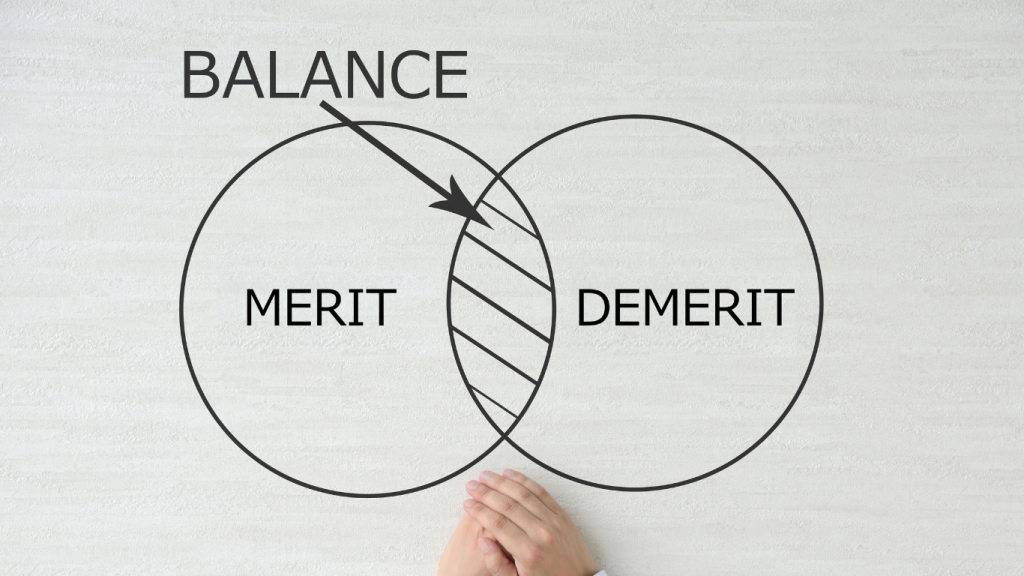
こちらがセンタレス切削と円筒研磨のメリットとデメリットを比較した表です。
特徴 | センタレス切削 | 円筒研磨 |
---|---|---|
セットアップ | セットアップが迅速で簡単 | 固定に時間がかかるが、一度セットすれば安定 |
精度 | 高精度が得られるが、セットアップに依存する | 非常に高い精度を実現 |
加工速度 | 連続生産による高速加工が可能 | 一品ずつの加工が基本で、センタレスより遅い |
形状の適用範囲 | 主に円筒形の部品に限られる | さまざまな形状やサイズに対応可能 |
設備コスト | 比較的低コスト | 設備投資が大きい |
技術要求度 | 操作が簡単であるが、最適な調整には熟練が必要 | 高い技術が必要で熟練が求められる |
センタレス切削と円筒研磨のメンテナンスと作業環境
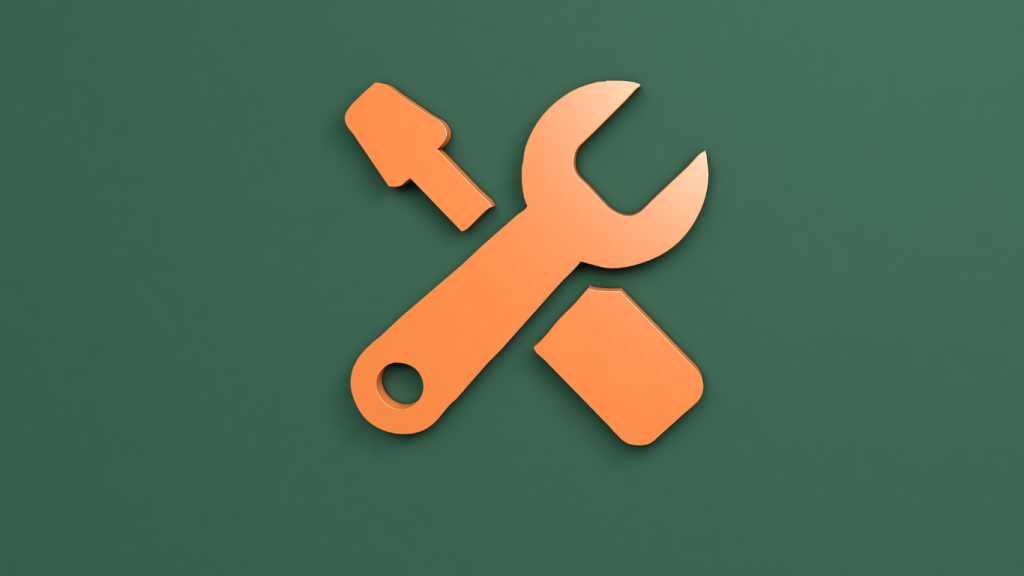
以下はセンタレス切削と円筒研磨のメンテナンスと作業環境を比較した表です。
項目 | センタレス研磨 | 円筒研磨 |
---|---|---|
メンテナンス | 砥石と調整車の定期的な調整が必要 | センタとチャックの精度保持とメンテナンスが重要 |
ブレードの摩耗や交換が頻繁に必要 | 砥石の交換とドレッシングが頻繁に必要 | |
研磨粉の除去と潤滑が重要 | スパークアウトの管理で精度を維持 | |
作業環境 | シンプルなセットアップで広いスペースは不要 | セットアップに時間がかかり、広い作業スペースが必要 |
連続作業によるノイズと熱が発生することが多い | 比較的静かで、精密作業に適した環境が必要 | |
量産に適しており、作業効率が高い | 単品作業や小ロット生産に適しており、柔軟性が高い |
まとめ
センタレス切削と円筒研磨は、それぞれ独自のメリットと特性を持つ重要な精密加工技術です。生産性や精度、そして柔軟性のバランスを取りながら、これらの方法を理解し、適切に選択することが、高品質な製品を効率的に生産する鍵となります。それぞれの技術がもたらす可能性を最大限に活かし、新たな製造の地平を切り開くことが求められています。技術の選択は単に工程の問題ではなく、製品の品質と直結しているため、正しい知識と適用が必要です。
お問い合わせ
弊社製品、加工についてのお問い合わせは、こちらで受付しております。
各部門のスペシャリストが、ご質問にお応えします。
電話
0574-54-2231
(平日 8:15~17:15)
FAX
0574-54-2235