- 2025/03/03
-
マシニングの深穴加工技術を徹底解説!
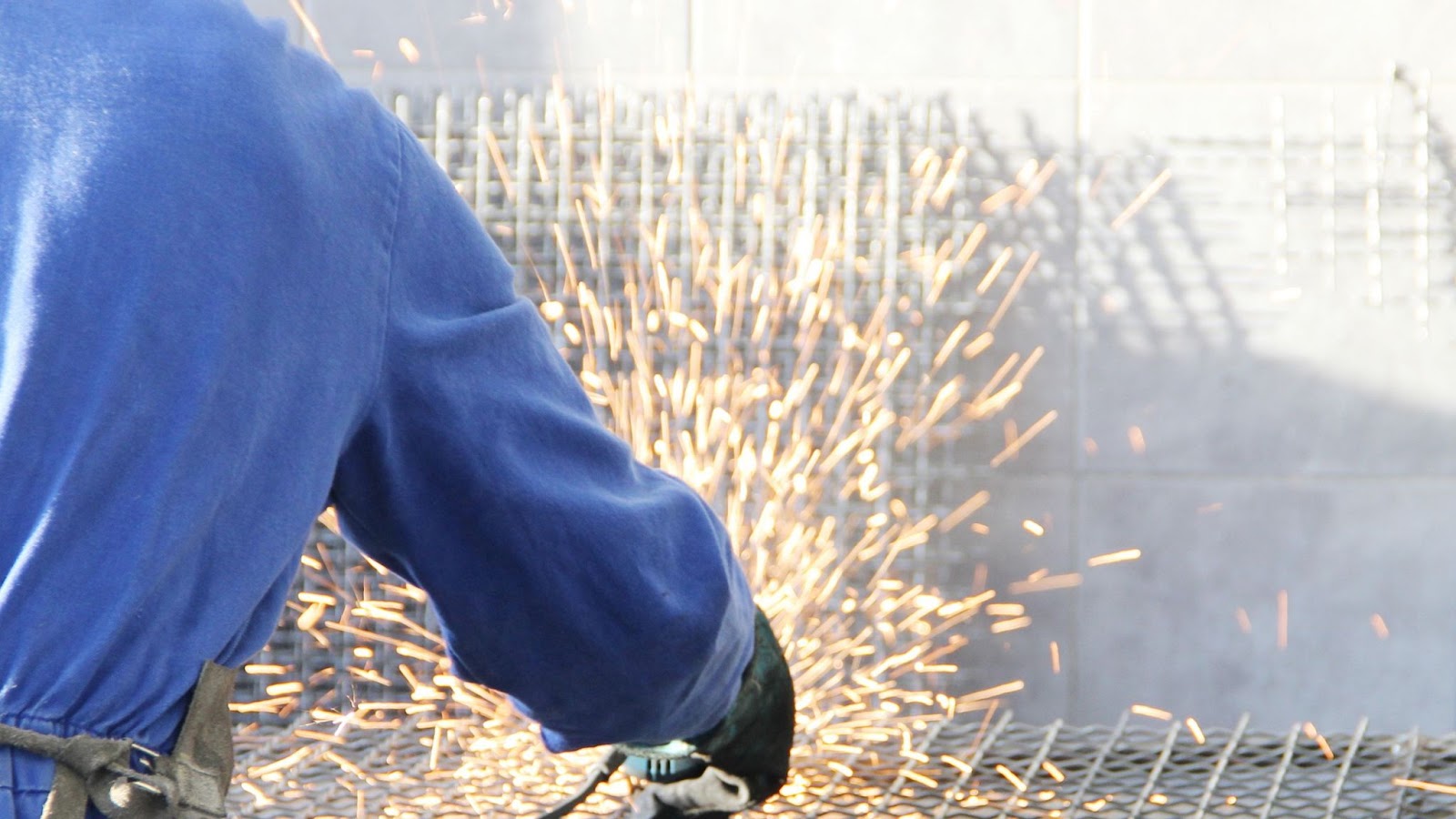
マシニングによる深穴加工は、製造業において欠かせない技術として広く利用されています。本記事では、深穴加工の基本概念から始まり、マシニングを用いる利点や主な用途、そして具体的な技術と手法について詳しく解説します。
また、NCプログラムによる自動化や、マシニングセンターでの実践方法にも触れ、最新技術とトレンドを紹介。深穴加工の高精度を実現するためのポイントやトラブルシューティングについても網羅し、実践的な知識を解説します。
マシニングの深穴加工とは
マシニングによる深穴加工は、製造業における高度な加工技術のひとつ。通常の穴加工よりも深さが大きく(直径の10倍以上)なる穴を、高精度かつ効率的に加工する手法です。特に金属加工では、エンジンやタービンなど多様な部品に適用され、その真円度や直線度が特に重視されます。
マシニングセンタを活用すれば、自動化と安定した精度管理が可能となり、振動や熱などの課題も最適な工具と加工条件によって軽減できます。
深穴加工の基本概念
深穴加工は、材料に大径比で極めて深い穴を加工する際に用いられる手法です。専用設計のドリルビットやボーリングバーを使用し、切削油・冷却液を活用しながら穴の内壁を滑らかに仕上げていきます。
切屑詰まりや工具摩耗を抑え、狙った寸法精度と形状を得るためには、加工条件を慎重に設定することが不可欠です。このプロセスは、エンジン部品や医療機器などの品質向上や製造効率に大きく貢献します。
マシニングを用いた深穴加工のメリット
マシニングセンタを活用した深穴加工には、多くのメリットがあります。マシニングセンタは高精度な加工を可能にし、複雑な形状の穴でも高い精度で掘削できます。
- 高精度の維持
マシニングセンタの制御精度と剛性によって、深穴でも安定した真円度や直線度を確保。 - 自動化と効率化
NCプログラムの活用により、作業者の負担を減らしながら一貫した品質を実現。 - リードタイム短縮
工具交換や加工条件をプログラム化できるため、段取り替えの時間を削減。 - コスト削減
適切な工具・切削条件を選定することで、摩耗を抑えつつ工具寿命を延ばし、メンテナンスコストを軽減。
深穴加工の主な用途
深穴加工は、多くの産業において幅広く利用されています。特に、自動車産業や航空宇宙産業では、エンジンやタービンの部品製造に深穴加工が必須です。これらの部品には、高い精度と耐久性が求められるため、深穴加工の技術の意義は極めて大きいといえます。
また、石油・ガス産業では、掘削機器やパイプラインの製造に深穴加工が施されます。さらに、医療機器や精密機械の分野でも、深穴加工は外せません。これらの分野では、高精度で複雑な形状の穴が求められることが多く、深穴加工技術がその要件を満たしています。
- 自動車・航空宇宙分野
エンジンやタービンなど、高精度と高い耐久性が求められる部品に多用。 - 石油・ガス産業
掘削機器やパイプライン部品に施される深穴加工で、厳しい使用環境下でも性能を保つ。 - 医療機器・精密機械
小径かつ複雑な形状の穴加工が必要とされる分野で、深穴加工が不可欠。
深穴加工の技術
深穴加工では、長尺のドリルを使い、高い精度を保ちながら多くの切屑を排出することが求められます。通常のドリル加工に比べ、熱処理や冷却、排屑技術など高度な制御が必要となるため、経験豊富な技術者や専用設備が不可欠です。
深穴加工に適した工具
深穴加工に適した工具は、通常のドリルとは異なり、特別な設計と材質を持っています。代表的な例としては、ガンドリルやBTAドリルがあります。
これらの工具は、切削熱を抑制しつつ切屑をスムーズに排出するため、専用の冷却・給排システムと組み合わせるのが一般的です。
- ガンドリル
小径の深穴に適した工具で、真直度を重視する場合に有効。 - BTAドリル
大径で深い穴の加工に適し、切削油を効率的に循環させる機構を備える。
高精度を実現するための技術のポイント
深穴加工で高精度を実現するには、いくつかの技術的ポイントを押さえることが大事です。まず、工具の選定とその状態管理が肝心。高精度を維持するためには、適切な工具の選択と定期的なメンテナンスが欠かせません。
また、切削条件の最適化も見逃せません。速度や送り量、切削深さなどをしっかり設定することで、加工精度が向上します。加えて、冷却液を効果的に使うことで熱を制御し、工具摩耗を抑えることができます。
- 工具の選定と管理
適切な材質やコーティングで摩耗や折損リスクを低減。 - 切削条件の最適化
回転数・送り量・切削深さなどをバランスよく設定し、精度と工具寿命を両立。 - 熱の管理
冷却液を効果的に供給して温度上昇を抑え、工具の摩耗を低減。 - 機械の剛性確保
振動やたわみを最小限にとどめ、高い寸法精度をキープ。
深穴加工のプロセス
深穴加工のプロセスは、いくつかのステップに分かれています。
- 仕様の確認と工具選定
穴径・深さなどの条件を基に、最適なドリルやパラメータを決定。 - 機械設定とプログラム作成
切削速度や送り、クーラントの供給方法などをNCプログラムで制御。 - 材料の固定とセンタリング
ワークピースがぶれないようしっかり固定し、必要に応じてセンタリングを実施。 - 加工実行と測定
途中で穴径や深さを測定しながら、最終的な仕上げ加工を行う。
トラブルシューティング
深穴加工では、工具の折損、穴の精度不良、切屑の詰まりなどのトラブルが起きるケースもあります。
工具の折損の原因は、過剰な切削抵抗や不適切な工具選定によるものです。適切な工具の選定と定期的な工具の状態チェックを必ず行いましょう。
また、穴の精度不良は、振動や工具のたわみが原因となります。機械の剛性を高め、適切な切削条件を設定することで改善できることがほとんどです。
切削油の供給不足や不適切な排出経路で起こる切屑の詰まりは、適切な冷却システムの導入と切屑の排出経路の設計を見直すことが必要です。
NCプログラムによる深穴加工の自動化
NCプログラムを活用した深穴加工の自動化は、製造業の効率的な生産において欠かせない存在です。NCプログラムは、数値制御を用いて工作機械を操作し、複雑な加工を正確に行えるようにします。
特に深穴加工では、手作業では難しい高精度が要求されるため、自動化が大いに役立ちます。
NCプログラムとは?
NC(Numerical Control)プログラムは、工作機械の動きをGコード・Mコードなどの数値で制御する仕組みです。これによって、穴の位置や深さ、工具の軌道などを一括で管理し、高精度かつ大量生産にも対応できます。
NCプログラムを使用した深穴加工の流れ
- 図面の解析とプログラム作成
穴の形状・深さを基に、工具軌道や加工順序を数値化。 - 工具・切削条件の設定
回転数、送り速度、クーラントなどを最適化し、機械に転送。 - 試運転・修正
空運転やシミュレーションにより、プログラムの動作を確認。 - 本加工
問題なければ実際の深穴加工を行い、適宜測定を実施。
NCプログラム作成の基本手順
NCプログラムを作成する際は、以下の手順やポイントに留意しましょう。
- 製品図面の分析
まずは、加工する製品の図面を詳細に読み取り、どのような加工が必要かを把握します。 - 工具や加工条件の選定
加工内容に応じて、使用する工具や速度・回転数などの条件を決定し、それに基づいてプログラムを組み立てます。特に、工具の選定と加工条件が不適切だと、加工精度の低下や工具破損、さらには製品不良の原因になります。 - プログラムへの反映
加工順序や工具の送り速度、回転数などをプログラムに正確に記述します。ここで誤りがあると、後の工程ですべてをやり直す必要が生じる場合もあるため、丁寧に入力・確認しましょう。 - シミュレーションによる検証
プログラムを実行する前に、シミュレーションで動作を確認し、事前にエラーを検出して修正します。これにより、実際の工作機械で問題が起きるリスクを大幅に低減できます。 - 安全対策の徹底
NC工作機械は高精度かつ強力なため、誤操作が重大な事故につながる可能性があります。プログラムの作成や実行時には、すべての動作が安全かつ正確に行われるよう、常に細心の注意を払うことが大切です。
効率的なプログラム運用のためのポイント
NCプログラムを効率的に運用するポイントは以下の通りです。これらを押さえることにより、NCプログラム運用効率が向上し、製造コスト削減や製品品質向上が期待できます。
- プログラムの標準化と管理徹底: オペレーターが異なっても同じ品質の加工を可能にし、生産効率を向上させます。
- 定期的なメンテナンスと更新: プログラムの精度を維持し、最新技術に対応します。
- オペレーターのスキルアップ: プログラム理解度を高め、トラブル対応を迅速化し、ダウンタイムを減らします。
- シミュレーションソフト活用: 事前検証でエラーを防ぎ、加工成功率を高めます。
マシニングセンターでの深穴加工の実践方法
マシニングセンターを使うことで、深穴加工を自動化しつつ高精度で行うことが可能です。適切な機種選定とセットアップを行えば、安定した生産性と品質を維持できます。
マシニングセンターの選び方
- 加工対象に合った主軸性能
回転数やトルクは、材料特性や穴の直径に応じて選定。 - 機械の剛性と制御精度
深穴加工での振動を抑え、誤差を最小限にするために重要。 - 生産量と自動化オプション
大量生産にはATC(自動工具交換)やパレットチェンジャー搭載機が有効。 - 操作性・メンテナンス性
シンプルなインターフェースやメンテナンスが容易な設計も選定基準。
セットアップと準備工程
- 工具の取り付け
深穴加工向けのドリルを正確に装着。刃長やドリル径の確認を行う。 - ワーク固定
加工中に振動やずれが生じないよう、しっかりとクランプ。 - NCプログラム設定
穴の深さ、位置、切削条件などを入力し、シミュレーションで動作確認。 - 切削条件の微調整
実際に試し加工を行い、仕上がりをチェックして最適化。
対話式プログラムの活用方法
対話式プログラムは、画面の指示に沿って穴の位置や径・深さを入力するだけで、自動的に加工経路を生成してくれるシステムです。プログラミング経験が浅いオペレーターでも直感的に操作でき、シミュレーション機能で加工動作を可視化できるため、ミスを減らしつつセットアップ時間を短縮できます。
加工品質を高めるための工夫
- 工具選定と交換周期の管理
切れ味が悪化した工具を使い続けると精度が落ちるため、定期的に交換。 - 最適な加工条件の設定
材料や穴のサイズに合わせて切削速度や送り量を調整。 - 温度管理
適切な冷却液供給やクーラントの循環で、熱変形による寸法ズレを防止。 - 定期メンテナンス
マシニングセンターの稼働精度を維持するため、軸や主軸の点検を徹底。
深穴加工の最新技術
深穴加工は、高精度と高効率を追求する中で常に進化を続けています。近年は切削速度を大幅に高める高速切削技術や、長寿命化につながるコーティング、高圧クーラントシステムなどが注目されています。
新素材への対応技術
航空宇宙や自動車産業では、チタン合金やCFRPといった熱特性や硬度の異なる新素材が増えています。こうした材料を扱う際は、工具選定や温度管理が従来以上に大切です。高速切削や特殊コーティング、振動抑制技術を組み合わせることで、加工精度を確保しながら工具摩耗を抑える取り組みが進んでいます。
IoTとAIによる加工プロセスの進化
- リアルタイム監視
IoTセンサーで機械の稼働状況や工具摩耗をモニタリングし、予防保全を実現。 - AIを活用した加工条件の最適化
大量の加工データを分析し、自動的に最適パラメータを提案。 - 自動プログラム生成
AIが材質や形状に応じた加工シーケンスを生成し、オペレーターの負担を軽減。
環境に配慮した加工技術
- ドライ加工や再利用可能クーラント
クーラント使用量を減らし、環境負荷を軽減。 - 高効率モーター・ポンプの導入
エネルギー消費を抑え、コストダウンとCO₂排出削減に貢献。 - 工具寿命の延長
工具交換頻度を最適化し、廃棄物と資源消費を低減。
まとめ
マシニングによる深穴加工は、NCプログラムや対話式プログラムを活用すれば、初心者でも短期間で習得しやすくなっています。たとえば、M6やΦ6.6、Φ11.0といったさまざまな穴径の加工も、プログラム設定で柔軟に対応可能です。
深穴加工では、工具の選定や冷却・排屑方法など、多角的な視点での管理が欠かせません。NCプログラムの標準化やシミュレーションを通じたミス防止、AIを含む新たな技術の取り入れ方次第で、生産性と品質をさらに高めることができます。ぜひこれらの要点を踏まえ、より効率的で高品質な深穴加工に挑戦してみてください。
お問い合わせ
弊社製品、加工についてのお問い合わせは、こちらで受付しております。
各部門のスペシャリストが、ご質問にお応えします。
電話
0574-54-2231
(平日 8:15~17:15)
FAX
0574-54-2235