- 2025/02/26
-
マシニングとフライスの違いとは?加工の特徴と使い分けを解説
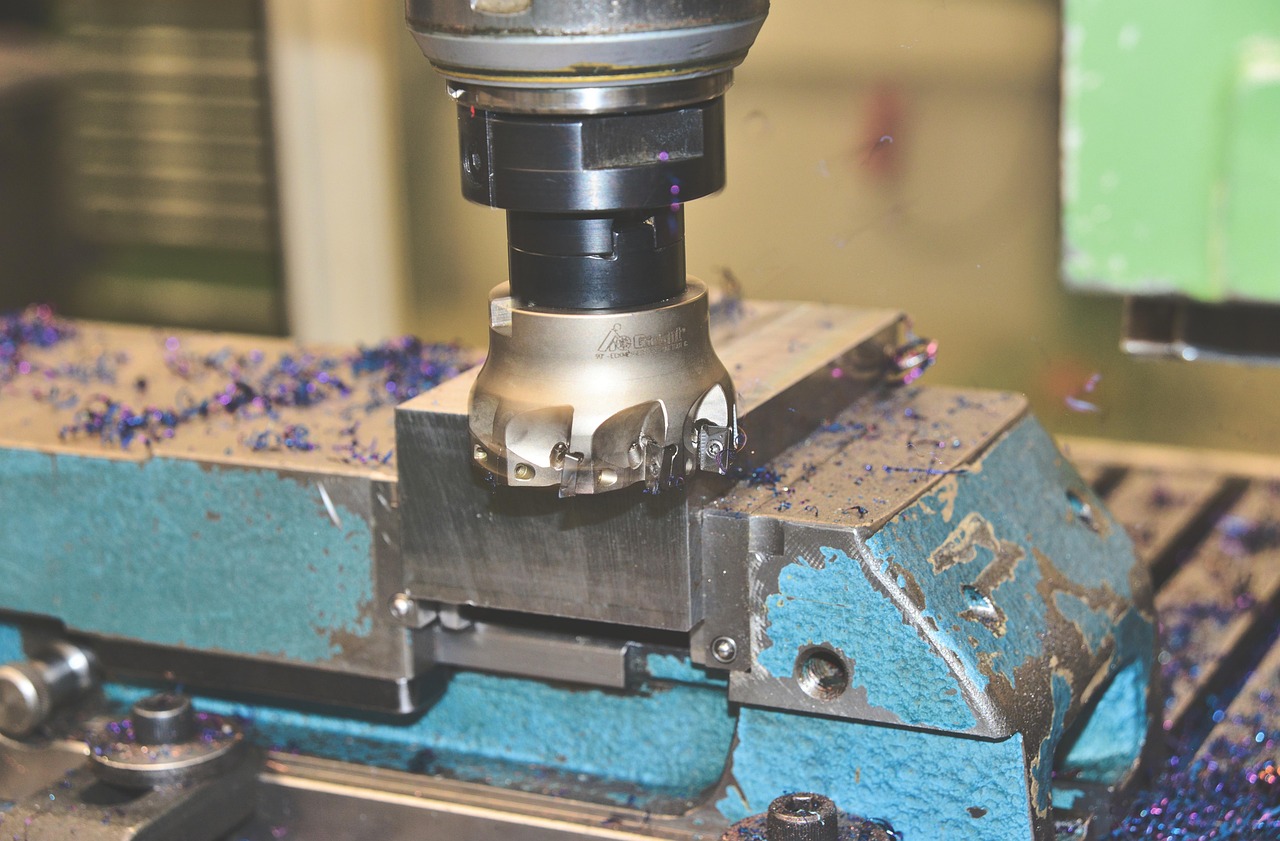
金属加工の現場でよく使われるマシニングセンターとフライス盤。どちらも切削加工を行う機械ですが、具体的な違いや用途を正しく理解していないと、より良い選択が難しくなります。それぞれの機械には特有の特徴があり、作業の効率や仕上がりの精度にも影響を与えます。本記事では、マシニングセンターとフライス盤の違いを詳しく解説し、それぞれのメリットや使い分けのポイントについて紹介します。
マシニングセンターとは?
製造業の現場では、金属や樹脂の加工を効率的に行うためにさまざまな機械が活用されています。その中でも、マシニングセンターは精密加工や大量生産を可能にする代表的な設備のひとつです。従来の手動フライス盤とは異なり、プログラムによる自動制御が可能であり、作業者の技量に左右されずに安定した品質を維持できます。それでは、まずマシニングセンターの基本的な定義について見ていきましょう。
マシニングセンターの定義
マシニングセンターとは、CNC(コンピュータ数値制御)を利用して加工動作を自動制御できる切削加工機です。オペレーターが手動で操作する必要がなく、プログラムされた指示に従って精密な加工を行うことが可能です。主に金属加工の現場で使用され、多様な加工を高い精度で実現できます。
マシニングセンターの特徴
マシニングセンターには、従来の手動フライス盤にはないさまざまな特徴があります。以下のポイントが、この設備が多くの製造現場で導入されている理由です。
1. 高精度な加工が可能
CNC制御により、ミクロン単位での精密加工が可能です。人間の手作業では再現が難しい均一な仕上がりが求められる部品でも、安定した品質を確保できます。また、誤差をできる限り抑えられるため、部品同士の組み合わせが必要な製品にも適しています。
2. 複数の加工工程を自動で実行
マシニングセンターは、穴あけ・フライス加工・ねじ切り・溝加工・研削など、多様な工程を1台の機械で完結できるのが強みです。手動で異なる工程を別々の機械で処理する必要がないため、作業の効率が向上し、生産スピードが大幅に向上します。
3. 切削工具の自動交換(ATC機能)
ATC(Automatic Tool Changer)機能により、加工内容に応じて工具を自動で交換できます。これにより、作業者が都度工具を変更する手間が省け、複数の工程を連続して実施可能になります。特に複雑な形状を加工する際には、異なる工具を使い分ける必要があるため、この機能の有無が生産効率に大きく影響します。
4. 大量生産向きの設備
自動化が進んでいるため、同じ品質の製品を大量に製造することに長けています。作業者の技術や経験による仕上がりのばらつきを抑え、安定した品質の製品を効率よく生産できます。特に、精密機器や自動車部品など、大量に生産される工業製品の加工には欠かせない存在です。
マシニングセンターの用途
マシニングセンターは、精密な加工が求められる幅広い業界で活用されています。主に以下のような場面で導入されています。
1. 精密機械部品の大量生産
マシニングセンターは、自動車部品・航空機部品・医療機器のパーツなど、精度が求められる製品の加工に適しています。同じ仕様の部品を大量に製造する場合、手作業では時間がかかるだけでなく品質にばらつきが出る可能性があります。しかし、マシニングセンターを導入することで、一定の品質を維持しながら効率的に生産できます。
2. 複雑な形状の部品加工
従来の手動フライス盤では加工が難しい3D形状や曲面加工、精密な溝加工なども、マシニングセンターなら可能です。例えば、金型の製造やエンジン部品の加工など、細かいディテールが求められる製品にも対応できます。
3. 高効率な生産ラインの構築
工場の生産ラインに組み込むことで、手作業の負担を減らし、製造スピードを向上できます。ロボットアームや自動搬送システムと連携させることで、さらに効率化が進み、夜間の無人運転や連続生産も可能になります。近年では、スマート工場(IoTを活用した生産管理システム)の一環としても導入が進んでいます。
フライス盤とは?
フライス盤は、工作機械の中でも古くから使用されている切削加工機の一つであり、金属や樹脂などの素材を削ることで、平面や溝、穴あけなどの加工を行うことができる設備です。近年はCNC(コンピュータ数値制御)による自動化が進んでいますが、フライス盤は今でも手動操作が可能な機種が多く、単品加工や試作品の製作などに広く活用されています。それでは、まずフライス盤の基本的な定義について詳しく見ていきましょう。
フライス盤の定義
フライス盤とは、主軸に取り付けた工具(フライスカッター)を回転させ、ワーク(加工対象)を切削することで形状を整える加工機のことです。手動で操作するものから、数値制御(NC)を搭載した半自動・全自動タイプまでさまざまな種類があり、用途に応じて使い分けられます。
フライス盤の特徴
フライス盤は、単品加工や試作品の製作に適した機械であり、特に小規模な工場や試作開発の現場で多く利用されています。その特徴を詳しく見ていきましょう。
1. 単品加工や試作向き
フライス盤は、一つひとつの部品を細かく調整しながら加工するのに適しており、試作品の製作やカスタムパーツの加工に向いています。大量生産には向かないものの、少量生産や個別の調整が必要な部品を作る際には欠かせない存在です。
2. 操作がシンプルで汎用性が高い
フライス盤は基本的な構造がシンプルなため、オペレーターのスキル次第でさまざまな形状の加工が可能です。機械によっては手動で細かい調整ができるため、加工対象の材質や形状に応じて柔軟に対応できる点が強みです。また、平面加工や側面加工、溝加工、穴あけなど、多様な用途に使えるため、汎用性が高い設備といえます。
3. 作業者の技術に依存する部分が大きい
フライス盤は、CNCマシニングセンターのような完全自動制御ではなく、オペレーターの手作業による調整が必要なため、仕上がりの品質は作業者の技量に大きく左右されます。熟練した技術者が扱えば高精度な加工が可能ですが、操作に慣れていない場合は、品質のばらつきが出る可能性もあります。そのため、フライス盤を使用する際は、オペレーターの技術力も大切な要素となります。
4. 初期投資が比較的低コスト
マシニングセンターと比較すると、フライス盤は導入コストが低く、初期投資を抑えやすいというメリットがあります。特に手動タイプのフライス盤は、装置自体の価格が安価であり、メンテナンスの負担も少ないため、小規模な工場や個人の工房でも導入しやすい機械です。
フライス盤の用途
フライス盤は、その汎用性の高さから、多くの業界で利用されています。特に、以下のような用途で活躍することが多いです。
1. 少量生産や試作品の製作
大量生産には向かないものの、新製品の試作や少数のカスタム部品の製造に適しています。例えば、試作品の製造工程で微調整をしながら加工する場合や、特定の顧客のオーダーに応じた部品の製作などに利用されます。また、試作品を作成してから本格的な生産に移行するケースでは、フライス盤が最初の加工ステップとして大切な役割を果たします。
2. 簡単な形状の部品加工
フライス盤は、直線的なカットや平面加工、穴あけ加工といった比較的シンプルな作業に適しています。たとえば、金属や樹脂の板材を削って平面を仕上げる作業や、ボルト穴や溝を加工する工程などでは、手動のフライス盤でも十分対応可能です。
3. 短期間での加工が必要な場合
NCやCNCを使わず、手作業で迅速に加工ができるため、短期間で部品を仕上げる必要があるときに有効です。例えば、急ぎの修理部品や追加部品が必要になった場合、マシニングセンターを使うよりも早く加工できるケースがあります。また、簡単な加工であれば、プログラムを組む手間が不要なため、即座に作業に取りかかることができるのも利点です。
マシニングセンターとフライス盤の違い
マシニングセンターとフライス盤はどちらも金属や樹脂の切削加工に使用される機械ですが、その特性や用途は大きく異なります。生産効率や加工精度、導入コストなど、さまざまな観点から違いを理解することで、目的に合った機械を選択できます。ここでは、加工精度や自動化レベル、適した加工内容、コスト面の違いについて詳しく解説します。
加工精度の違い
マシニングセンターはCNC(コンピュータ数値制御)を活用することで、極めて高精度な加工を実現できます。 設定されたプログラム通りに工具が動作するため、仕上がりのばらつきが少なく、一貫した品質を維持することが可能です。特に、ミクロン単位の誤差が許されない精密機械部品や金型製作などの分野では、CNC制御の強みが発揮されます。
一方で、フライス盤は作業者が手動で操作することが多く、加工精度は技術者の腕に左右される傾向があります。 手作業の微調整が可能なため、細かなカスタマイズや一品ものの製作には向いていますが、同じ形状の部品を大量に作る場合は精度のばらつきが生じやすくなります。NC制御を搭載したフライス盤であれば一定の精度を保つことはできますが、マシニングセンターほどの安定性はありません。
作業の自動化レベル
マシニングセンターはCNC制御により全自動での加工が可能です。 加工プログラムをセットすれば、工具の交換や工程の切り替えも自動で行われ、連続した生産ラインに適しています。特に大量生産を行う工場では、無人運転が可能な点が大きなメリットです。近年は、ロボットアームや搬送システムと連携することで、さらなる効率化が進んでいます。
フライス盤は基本的に手動操作が主体であり、一部の機種ではNC制御による半自動運転も可能ですが、完全自動化には対応していません。 作業者が材料をセットし、手動で工具を移動させながら加工を進めるため、マシニングセンターと比較すると生産効率は低くなります。しかし、その分自由度が高く、試作品や特注品の加工に適しています。
適した加工内容
マシニングセンターとフライス盤では、それぞれ適した加工内容が異なります。
マシニングセンターに適した加工
- 大量生産を前提とした加工(自動車部品、電子機器部品など)
- 高精度な寸法が求められる製品(航空機部品、精密機械部品など)
- 複雑な形状の部品(金型や3D形状の加工)
フライス盤に適した加工
- 単品部品の製作(少量生産品や試作品)
- 簡単な形状の加工(平面削りや穴あけなど)
- 短期間での仕上げが求められる部品(修理用のスペアパーツや追加加工)
コストの違い
マシニングセンターは高価な設備ですが、長期的に見れば生産効率の向上に貢献し、結果的にコスト削減につながります。 導入時の価格は数百万円から数千万円と高額ですが、自動化による作業時間の短縮や、人件費の削減が可能になります。また、安定した品質で大量生産が可能なため、歩留まり率が向上し、材料ロスを減らせる点も経済的メリットの一つです。
対して、フライス盤は比較的安価で導入でき、特に手動タイプのものは初期投資を抑えやすいのが特徴です。 数十万円程度から購入できるモデルもあり、小規模な工場や個人事業主でも導入しやすくなっています。ただし、作業者の熟練度に依存するため、生産スピードや品質にばらつきが出る可能性があり、結果的にコストがかかる場合もあります。
比較表:マシニングセンター vs フライス盤
項目 | マシニングセンター | フライス盤 |
制御方法 | CNCによるプログラム制御 | 手動操作またはNC制御 |
作業の自動化 | 完全自動化が可能 | 手動または半自動 |
加工精度 | 高精度(ミクロン単位の誤差) | 作業者の技量に依存 |
加工の適用範囲 | 複雑な形状や高精度が求められる部品 | 比較的シンプルな形状の加工 |
生産効率 | 高速かつ連続加工が可能 | 作業者の手作業が必要なため低め |
初期導入コスト | 高額(数百万〜数千万) | 比較的低コスト(数十万〜) |
適した用途 | 大量生産、精密加工、自動化ライン | 少量生産、試作品製作、カスタム加工 |
どちらを選ぶべきか?用途別の使い分け
マシニングセンターとフライス盤は、それぞれ特有のメリットを持つ加工機ですが、用途に応じた適切な選択をすることで、作業効率の向上やコスト削減が可能になります。大量生産向きなのか、少量生産向きなのか、また求める加工精度や導入コストなどを総合的に考慮することが大切です。 ここでは、具体的な使用シーンを想定し、それぞれの機械を選ぶべきケースを詳しく解説します。
マシニングセンターを選ぶべきケース
ここでは、マシニングセンターを選ぶべきケースを紹介します。
1. 高精度な部品を大量に生産する場合
マシニングセンターはCNC(コンピュータ数値制御)による高精度な加工を可能にするため、大量生産向けの製造現場に適しています。 自動車部品、航空機部品、医療機器部品など、厳密な寸法公差が求められる製品において、手作業では実現しにくい精度を安定して確保できるのが大きな強みです。また、同じ仕様の部品を何百、何千単位で製造する場合でも、品質のバラつきを抑えられるため、高精度かつ均一な仕上がりを実現できます。
2. 複雑な形状の加工をする場合
マシニングセンターは、従来のフライス盤では加工が難しい複雑な形状の部品を高精度で削り出すことが可能です。 例えば、3D形状や多軸加工が必要な金型、精密な溝加工、ねじ切り、曲面加工などに対応できるため、金型製作や電子機器の部品加工におすすめです。また、工具の自動交換機能(ATC)が搭載されているため、複数の異なる加工を一度のセットアップで連続して行うことができ、工程の大幅な短縮が可能です。
3. 生産効率を向上させたい場合
生産コストを抑えつつ、加工のスピードと精度を向上させたい場合は、マシニングセンターの導入が有効です。 マシニングセンターは、プログラムを一度設定すれば自動で連続加工ができるため、人手を介さずに24時間無人稼働することも可能です。そのため、人件費を削減しながら大量生産を行いたい場合や、工場の生産性を向上させたい場合におすすめです。 また、ロボットアームや自動搬送システムと組み合わせることで、さらに効率的な生産ラインを構築できるため、規模の大きい工場では欠かせない設備となっています。
フライス盤を選ぶべきケース
ここでは、フライス盤を選ぶべきケースを紹介します。
1. 試作品や少量生産を行う場合
フライス盤は、単品加工や少量生産を行う際に適した加工機です。 試作品の製作では、頻繁に設計変更が入ることが多く、その都度プログラムを設定する必要があるマシニングセンターよりも、柔軟に対応できるフライス盤の方が適しています。 特に、開発段階で細かな調整が求められる場合や、短納期での対応が必要なケースでは、作業者が手動で調整できるフライス盤が有利です。
また、小ロット生産の場合、マシニングセンターのように高額な設備投資を行うよりも、比較的安価に導入できるフライス盤を活用する方がコスト面でも効率的です。そのため、多品種少量生産を行う工場や、特注品を製作する現場では、フライス盤の導入が適しています。
2. シンプルな形状の加工がメインの場合
直線的な切削や単純な穴あけ、溝加工といった基本的な加工を行う場合には、フライス盤が適しています。 マシニングセンターを使用するほどの複雑な形状でなければ、手動またはNC制御のフライス盤でも十分に対応できるため、加工コストを抑えることが可能です。
例えば、金属や樹脂のプレートに対する平面削りや、単純なボルト穴の追加加工、角の面取りなど、基本的な作業を素早く行う必要がある場面では、マシニングセンターを使うよりもフライス盤の方が短時間で作業を完了できることもあります。
3. 初期投資を抑えたい場合
設備投資の予算が限られている場合、フライス盤の導入がより現実的な選択肢となります。 マシニングセンターは数百万〜数千万円のコストがかかるのに対し、フライス盤は比較的安価で、手動タイプであれば数十万円程度から導入が可能です。
また、マシニングセンターのようなCNCプログラミングの知識が不要なため、導入後すぐに稼働できる点もフライス盤の利点です。 さらに、マシニングセンターの場合は設備のメンテナンスやオペレーターの教育にもコストがかかりますが、フライス盤であれば比較的手軽に運用できるため、小規模な工場や個人事業主が加工機を導入する際に適した選択肢といえます。
まとめ
マシニングセンターとフライス盤は、どちらも金属加工に欠かせない機械ですが、それぞれの特性を理解し、適切に使い分けることが生産効率を高める鍵となります。高精度な部品を大量に生産する場合や、複雑な形状の加工が求められる場合には、マシニングセンターがおすすめです。一方で、単品加工や試作品の製作、コストを抑えた導入を検討している場合は、フライス盤が有効な選択肢となります。
弊社では、新しい精密加工機械を取り揃え、お客様のニーズに応じたより良い解決策を提案しております。 新規導入をご検討の際は、専門のスタッフがご要望に沿った機種選定や技術的なアドバイスを行い、導入後の運用についてもサポートいたします。製品の詳細や導入に関するご相談は、お気軽にお問い合わせください。
お問い合わせ
弊社製品、加工についてのお問い合わせは、こちらで受付しております。
各部門のスペシャリストが、ご質問にお応えします。
電話
0574-54-2231
(平日 8:15~17:15)
FAX
0574-54-2235