- 2025/02/28
-
マシニングにおける芯出しの基本と精度向上のポイント
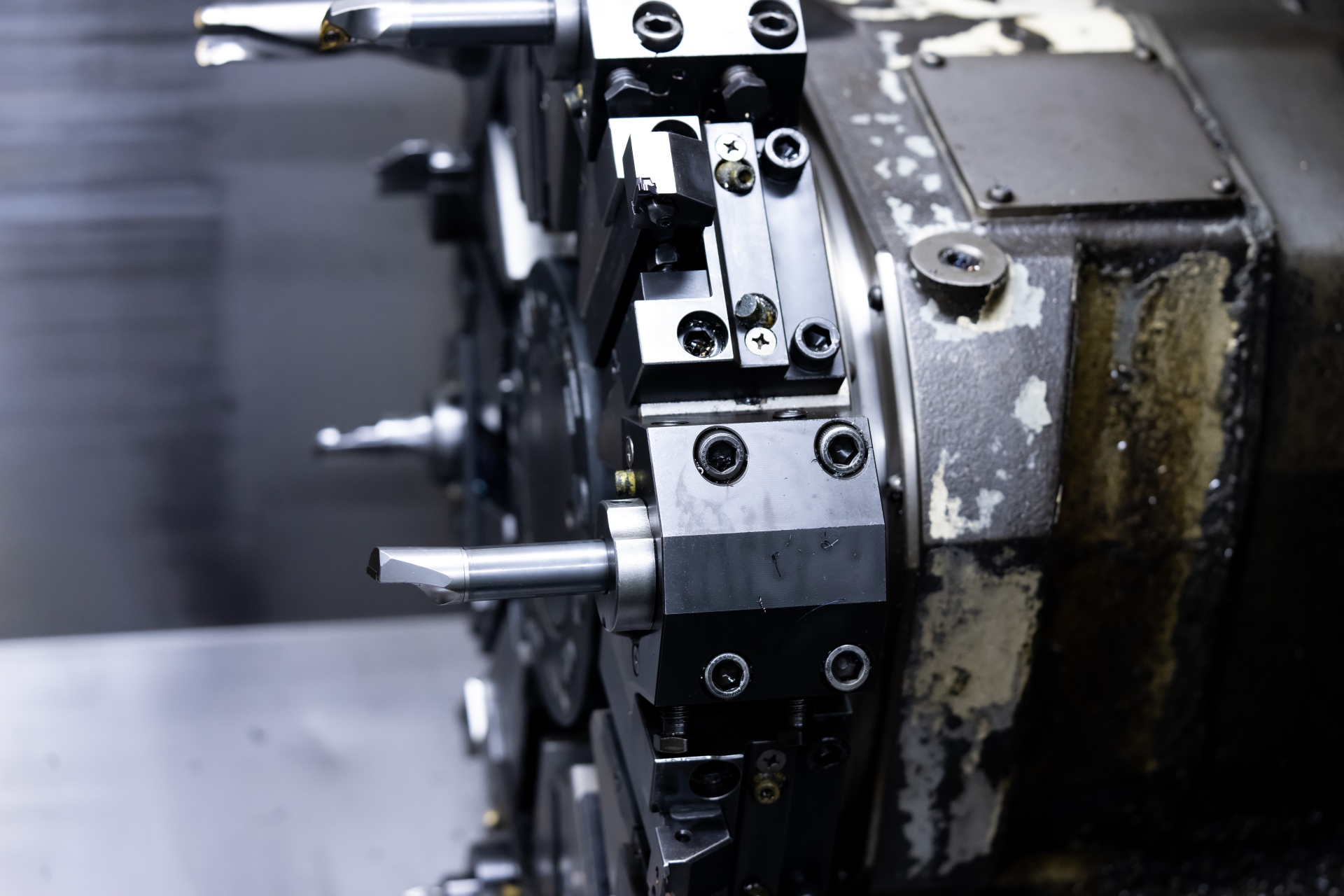
マシニング加工において、高い精度を維持するためには「芯出し」が欠かせません。加工の基準を正確に設定できるかどうかで、仕上がりの品質や作業効率が大きく左右されます。芯出しが甘いと、寸法誤差や加工不良につながり、手戻りが発生することもあります。適切な手法を理解し、適用することで、安定した加工を実現できるでしょう。この記事では、芯出しの基本から、精度を向上させるポイント、よくあるトラブルとその対策について詳しく解説します。
芯出しとは?
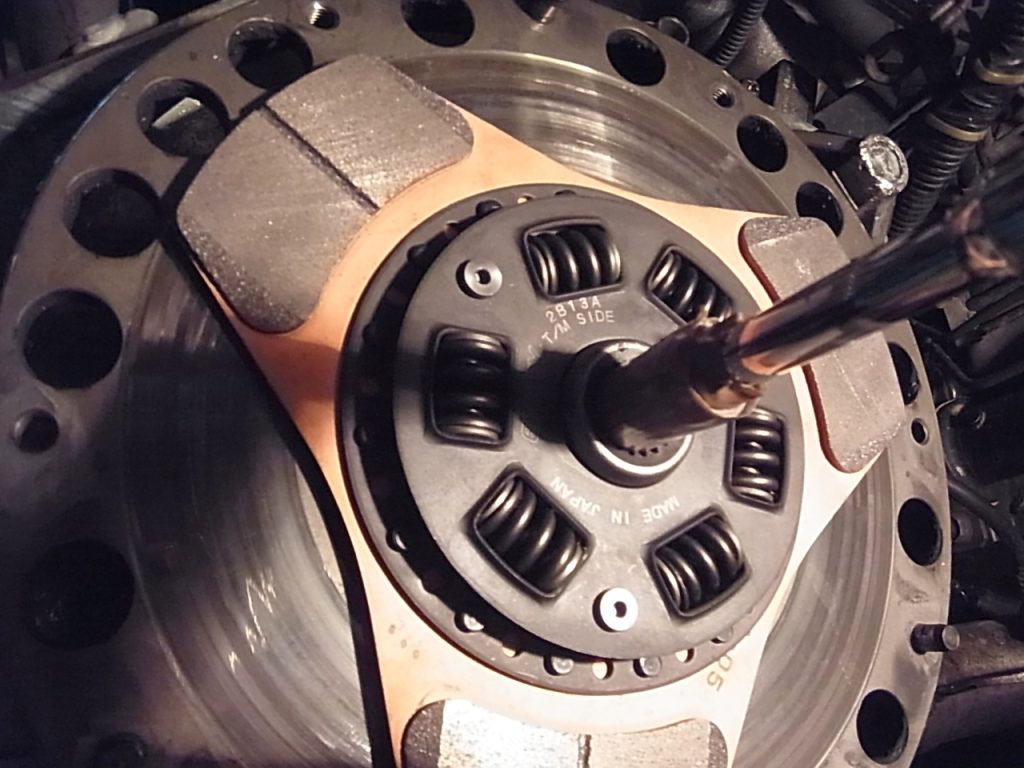
マシニング加工を行う上で、芯出しは避けて通れない工程の一つです。加工精度を向上させるためには、ワーク(加工対象)や工具の位置を正確に調整し、適切な基準を設定することが不可欠です。この作業が適切に行われないと、寸法精度のズレや仕上がりのバラつきが発生し、不良品の発生や加工トラブルにつながる可能性があります。ここでは、芯出しの基本概念について詳しく解説します。
芯出しの定義と目的
芯出しとは、ワークや工具の中心位置を正しく調整し、加工基準となる座標を正確に設定する作業のことを指します。マシニングセンターでは、ワークの取付位置や回転軸の芯を合わせることで、切削加工時の精度を確保します。特に高精度な加工を求められる製品では、わずかな芯ズレが加工ミスにつながるため、慎重な芯出しが求められます。
芯出しの目的は、主に以下の3点に集約されます。
- 加工精度の向上
- 芯出しを正確に行うことで、ワークの寸法誤差をできる限り抑え、均一な仕上がりを実現できます。
- 芯出しを正確に行うことで、ワークの寸法誤差をできる限り抑え、均一な仕上がりを実現できます。
- 工具寿命の延長
- 芯ズレがあると、工具に偏った負荷がかかり、摩耗が早まります。芯出しが適切に行われていれば、工具の消耗を抑え、長期間安定した加工が可能になります。
- 芯ズレがあると、工具に偏った負荷がかかり、摩耗が早まります。芯出しが適切に行われていれば、工具の消耗を抑え、長期間安定した加工が可能になります。
- 加工の再現性の確保
- 芯出しを適切に行うことで、複数回の加工においても同じ仕上がりを維持でき、量産時の品質管理が容易になります。
芯出しが必要なシーン
芯出しは、あらゆるマシニング加工において大切な作業ですが、特に以下の加工では精密な芯出しが求められます。
穴あけ加工における芯出し
ドリルやエンドミルを使用して穴を開ける際、芯出しの精度が仕上がりの品質に大きな影響を与えます。ワークと工具の中心軸がずれていると、穴の位置が設計値と異なったり、真円度が損なわれたりすることがあります。特に深穴加工では、芯ズレによるビビりや切削抵抗の偏りが発生しやすいため、芯出しを入念に行うことが大切です。
穴あけ加工の芯出しを行う際には、ダイヤルゲージやエッジファインダーを用いて、ワークの基準面と工具の中心を正確に合わせることが一般的です。また、高精度な加工を求められる場合は、タッチプローブを活用した自動芯出しシステムを導入するのも有効な手段となります。
フライス加工における芯出し
フライス加工では、ワークの基準面と工具の刃先が正確に位置合わせされていることが、均一な切削仕上がりを得るために不可欠です。芯出しが不十分だと、加工面に段差ができたり、切削負荷が偏って工具が破損するリスクが高まります。
特に、多面加工や高精度な直線切削を行う場合、芯出しの誤差が仕上がりに直結します。ダイヤルゲージを使用してテーブルの平行度を調整し、ワークの位置を確認することで、芯出しの精度を確保できます。また、クランプによる歪みが発生しないように、ワークの固定方法にも注意が必要です。
旋盤加工との違い
旋盤加工とマシニング加工では、芯出しのアプローチが異なります。旋盤では、ワーク自体が回転するため、回転軸を中心に芯出しを行う必要があります。一方、マシニングセンターでは、工具が回転し、ワークが固定されるため、工具とワークの基準点を合わせることが求められます。
旋盤加工において芯ズレが発生すると、ワークの回転によってバランスが崩れ、振動が発生しやすくなります。そのため、芯出しには三つ爪チャックや四つ爪チャックを使用し、ワークの中心を慎重に調整することが大切です。また、芯押し台を利用して軸方向のブレを防ぐことも、精度向上につながります。
一方、マシニング加工では、ワークの固定が芯出しの精度を左右します。特に、ワークのクランプ時に歪みが生じると、加工後の精度に悪影響を及ぼします。そのため、適切なバイスや治具を選定し、ワークの固定方法を工夫することが大切です。
芯出しは加工方法ごとに異なるアプローチが必要ですが、いずれの場合も正確な芯出しを行うことで、加工品質の向上や工具寿命の延長につながります。
芯出しの方法と使用工具
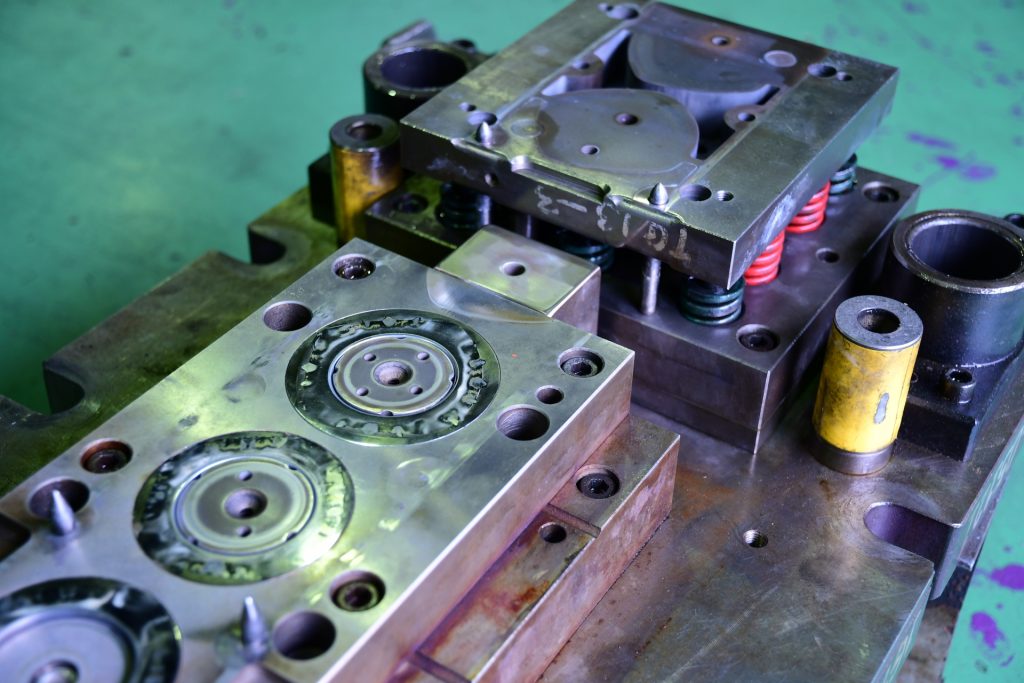
マシニング加工において、芯出しの正確さは加工精度を大きく左右します。芯出しの方法には、大きく分けて手動による方法と、自動化されたシステムを活用する方法の2種類があります。それぞれの手法には特徴があり、加工内容や求められる精度に応じて使い分けることが大切です。ここでは、手動で行う芯出しとCNCマシニングセンターの自動芯出しシステムについて詳しく解説します。
手動による芯出し
手動で芯出しを行う場合、作業者の技術力が加工精度に直接影響します。工具やワークの基準点を正確に合わせることで、均一な切削が可能になります。一般的に使用される測定工具として、ダイヤルゲージやハイトゲージがあり、それぞれの特徴を理解して適切に活用することが大切です。
ダイヤルゲージを使用した芯出し手順
ダイヤルゲージは、ワークの基準面とスピンドル軸との位置関係を微調整するための測定工具です。高精度な芯出しを行うためには、以下の手順をしっかり守ることが大切です。
- ダイヤルゲージの取り付け
- マシニングセンターのスピンドルに、ダイヤルゲージを取り付ける。
- ゼロ点を基準として、測定する方向を設定する。
- ワークの基準面を測定
- スピンドルを回転させながら、ワークの基準面をなぞるように測定する。
- ダイヤルゲージの針が示す数値を確認し、高低差がないかチェックする。
- 調整作業
- 数値のブレがある場合は、ワークの位置を微調整する。
- バイスやクランプの締め具合を均一にし、固定時に歪みが生じないようにする。
- 最終確認
- もう一度測定を行い、数値が一定であることを確認する。
- 測定が完了したら、ダイヤルゲージを取り外して加工を開始する。
ダイヤルゲージを用いた芯出しは、精度が高くコストも抑えられるため、手動芯出しの基本技術として広く活用されています。
ハイトゲージを活用した方法
ハイトゲージは、ワークの高さや基準面を測定し、芯出しを行うための測定工具です。特に、基準面を決定する際に活用されることが多く、精密な位置合わせが求められる加工に適しています。
- ワークの基準面を設定
- ワークをマシンテーブルに設置し、クランプで固定する。
- ハイトゲージを用いて、基準面の高さを測定する。
- 測定データをもとに調整
- 測定値を確認し、ワークの高さが均一になるように微調整する。
- ワーク固定時に生じる歪みを防ぐため、適切な治具を使用する。
- 芯出しの最終チェック
- 測定値が安定したら、ワークをしっかり固定し、加工の準備を整える。
ハイトゲージは、高さ基準を正確に測定できるため、穴あけ加工やフライス加工時の芯出し作業に役立ちます。
手動芯出しのメリット・デメリット
メリット
- 測定工具が比較的安価で導入しやすい。
- 細かい調整が可能で、高精度な加工が実現できる。
- 設備の種類に関わらず、幅広い加工に対応可能。
デメリット
- 作業者の技量に依存するため、熟練度によって精度が変わる。
- 測定と調整に時間がかかり、生産性が低下しやすい。
- 繰り返し作業が多い場合、自動化と比べて手間がかかる。
自動芯出しシステム
近年のCNCマシニングセンターでは、芯出しを自動で行う機能が搭載されており、高精度な加工が短時間で実現できるようになっています。特に、大量生産や複雑な形状の加工において、手動による芯出しの手間を削減し、生産効率を向上させることが可能です。
CNCマシニングセンターの自動芯出し機能
CNCマシニングセンターには、ワークの位置を自動で検出し、基準点を設定する機能が備わっています。
- ワークの設置
- ワークをマシンテーブルにセットし、固定する。
- クランプによる歪みを防ぐため、適切な圧力で締める。
- 基準点の測定
- マシニングセンターの自動測定機能を利用し、ワークの座標を測定する。
- 測定データをもとに、CNCプログラムが適した位置調整を行う。
- 自動調整
- 測定値をCNCシステムが解析し、適切な芯出し補正を実行する。
この機能により、作業者が手動で芯出しを行う手間が省け、精度のバラつきを抑えることが可能になります。
タッチプローブの活用
タッチプローブは、自動芯出しを行うための高精度な測定装置です。ワークの基準面や穴位置を正確に検出し、加工の基準点を自動で設定します。
タッチプローブのメリット
- 測定精度が高く、ミクロン単位の誤差を抑えられる。
- 人為的なミスを減らし、一貫した品質を確保できる。
- 測定データがCNC制御に反映され、自動補正が可能。
新しい測定機器による高精度芯出し
近年では、レーザー測定器や3Dスキャナーを活用した芯出し技術も導入されており、より精密な加工が実現可能になっています。
- レーザー測定器:非接触でワークの位置を測定し、ズレをできる限り抑える。
- 3Dスキャナー:ワークの形状をデジタルデータ化し、正確な位置調整を行う。
これらの新しい技術を活用することで、従来の芯出し手法と比べて精度が格段に向上し、作業時間の短縮にもつながります。
芯出しには手動と自動の方法があり、それぞれにメリット・デメリットがあります。加工内容や求める精度に応じて適切な方法を選択し、より良い工具を活用することが、高品質なマシニング加工を実現する鍵となります。
芯出し精度を高めるためのポイント
マシニング加工において、芯出しの精度が仕上がりの品質に直結します。芯ズレが発生すると、加工寸法の誤差や工具の摩耗が進み、不良品の発生や生産効率の低下につながるため、できる限り精度を高めることが大切です。芯出し精度を向上させるためには、ワークの固定方法、基準面の管理、さらには周囲の環境条件まで考慮する必要があります。ここでは、それぞれのポイントについて詳しく解説します。
ワーク固定のポイント
ワークの固定が不十分だと、加工時に振動が発生し、精度に悪影響を及ぼします。適切な固定を行うことで、芯出しの精度を維持し、安定した加工が可能になります。
バイスやクランプの適切な使用方法
ワークを固定する際に一般的に使用されるのがバイスやクランプです。正しく使用しないと、固定力が不均一になり、芯出し精度が低下してしまいます。
- 適切な締め付け圧の調整
- 強すぎる締め付けはワークの変形を引き起こし、加工後の寸法誤差の原因になります。
- 逆に、締め付けが弱いと加工中にワークが動いてしまい、加工位置のズレにつながるため、適切な圧力で固定することが大切です。
- クランプ位置のバランス調整
- ワークの片側だけを強く固定すると、傾きや歪みが生じる可能性があります。
- クランプを対称的に配置し、均等な力がかかるように調整することで、芯出し精度を向上できます。
- 専用治具の活用
- 形状が複雑なワークの場合、標準的なバイスやクランプでは安定した固定が難しいことがあります。
- 専用の治具やサポートブロックを使用することで、より精密な固定が可能になります。
ワークのたわみ・歪みを防ぐコツ
ワークの固定時にたわみや歪みが発生すると、芯出しの基準点がずれてしまい、加工精度に影響を与えます。以下の対策を講じることで、歪みをできる限り抑えられます。
- ワークの支持点を増やす
- 固定点が少ないと、ワークが浮いたり、たわみが生じることがあります。
- 可能な限り支持点を増やし、均等に固定することで、歪みを抑えられます。
- クッション材を活用する
- 固定時に金属製のバイスやクランプがワークを直接押さえると、圧力が一点に集中し、変形の原因になります。
- ゴム製や樹脂製のクッション材を使用すると、ワークの変形を防ぎながら安定した固定が可能になります。
基準面の確認と調整
芯出しの基準となる面が正しく設定されていないと、ワークの位置がずれ、加工精度に影響を及ぼします。基準面の管理を徹底することで、安定した加工が実現できます。
基準面の精度を確保する重要性
基準面とは、ワークの位置決めや芯出しの際に基準となる面のことで、加工の精度を左右する重要な要素です。
- 基準面のフラットネスを確認
- ダイヤルゲージを使用し、基準面が平坦であることを確認します。
- 平坦でない場合、面削加工やラッピング処理を行い、精度を高めます。
- 基準面に適した固定方法を選択
- 基準面がしっかりしていないと、ワークがずれやすくなります。
- 吸着チャックや真空チャックを活用すると、安定した固定が可能になります。
ゼロ点設定
芯出しを行う際、ゼロ点(基準点)を正しく設定することで、加工精度を大幅に向上させることができます。
- タッチプローブやエッジファインダーの活用
- 手動で芯出しを行う場合、エッジファインダーを使ってワークの位置を確認します。
- CNCマシニングセンターでは、タッチプローブを使用して自動でゼロ点を設定することが可能です。
- 複数回測定して誤差を確認
- 一度の測定だけでなく、複数回測定して誤差がないことを確認することで、より精度の高いゼロ点設定ができます。
環境要因の影響
芯出し精度は、加工環境にも大きく影響を受けます。特に、温度変化や機械の剛性など、外的要因を考慮することで、安定した加工を実現できます。
温度変化による影響と対策
- 機械やワークの熱膨張に注意
- 金属は温度変化によって膨張・収縮するため、加工精度に影響を与えることがあります。
- 特に、朝と夜で気温が大きく変化する環境では、芯出しの基準が変わる可能性があります。
- 加工前のウォーミングアップ
- 機械の主軸を一定時間回転させ、温度を安定させることで、熱膨張による影響をできる限り抑えます。
- 機械の主軸を一定時間回転させ、温度を安定させることで、熱膨張による影響をできる限り抑えます。
- 温度管理の徹底
- 空調を活用し、作業場の温度を一定に保つことが大切です。
- 加工中の温度変化をリアルタイムでモニタリングし、補正を行うことで、高精度な加工が可能になります。
機械の剛性と芯出しの関係
- マシンの剛性を確保
- 剛性が不足していると、加工時に振動が発生し、芯ズレが生じる可能性があります。
- ベッドやコラムの剛性を確認し、必要に応じて補強を行うことで、芯出し精度を向上できます。
- 振動対策を施す
- 振動が大きい環境では、芯出しの精度が安定しません。
- 防振パッドの設置や、振動の少ない固定方法を採用することで、より精密な芯出しが可能になります。
芯出し精度を高めるには、ワークの固定方法、基準面の管理、環境要因を適切にコントロールすることが不可欠です。これらのポイントを意識することで、高精度なマシニング加工を安定して行うことが可能です。
よくあるトラブルと対策
マシニング加工において、芯出しが不正確だと、加工精度に悪影響を及ぼし、不良品の発生や工具の摩耗を早める原因となります。芯出しに関するトラブルは多くの現場で見られますが、正しい知識と対策を講じることで、ミスをできる限り抑えることが可能です。ここでは、芯出しミスによる加工不良の例、測定誤差を減らすための工夫、ワークのズレや振動を防ぐためのポイントについて詳しく解説します。
芯出しミスによる加工不良の例
芯出しが不適切なまま加工を行うと、ワークの位置がずれたり、切削時の負荷が偏ったりして、さまざまな加工不良が発生します。以下のようなトラブルが代表的な例です。
寸法誤差が発生する
芯出しがずれていると、ワークの基準位置が正しく設定されず、寸法のズレが発生します。特に、精度が求められる穴あけ加工や溝加工では、数ミクロンの誤差が大きな不良につながることがあります。
- 対策
- ダイヤルゲージやタッチプローブを活用して、芯出しの精度を高める。
- 加工前に試し削りを行い、寸法誤差がないか確認する。
工具の偏摩耗や破損が起こる
芯出しが不正確な場合、工具の一部分に過剰な負荷がかかり、摩耗が偏って進行します。その結果、工具寿命が短くなり、工具が破損することもあります。
- 対策
- 芯出しの際、ワークの高さや角度のズレを入念にチェックする。
- 高精度な芯出しが求められる場合は、CNCの自動芯出し機能を活用する。
加工面の仕上がりが悪くなる
芯ズレによって、加工面にビビり(振動による微細な波紋)が発生し、仕上がりの品質が低下することがあります。
- 対策
- ワーク固定時のたわみや歪みを防ぐため、クランプの力を均等にかける。
- 環境要因(機械の振動や温度変化)を考慮し、安定した加工環境を整える。
ダイヤルゲージの誤差を抑える方法
ダイヤルゲージを用いた芯出しは一般的ですが、誤差が発生しやすいため、正確な測定を行うためのポイントを押さえておくことが大切です。
測定方向
- ダイヤルゲージの測定方向が適切でないと、正確な数値が得られません。測定点の位置を変えながら、誤差が発生していないかチェックすることが大切です。
- ワークの中心を測る際は、ダイヤルゲージの接触面が直角になるように配置し、正確な測定ができるようにする。
ダイヤルゲージの振れを抑える
- 測定中にダイヤルゲージが揺れてしまうと、誤差が発生しやすくなります。スピンドルをゆっくりと動かしながら、均等な測定が行えるように調整することが大切です。
- マグネットスタンドを使用し、ゲージが安定した状態で測定を行う。
複数回の測定で確認する
- 一度の測定だけではなく、異なる方向から数回測定し、数値のズレがないことを確認する。
- 測定ごとにゼロリセットを行い、誤差が積み重ならないようにする。
ワークのズレや機械の振動を防ぐポイント
芯出しの精度が高くても、加工中にワークがずれてしまうと、正確な寸法を保てません。また、機械の振動によって微細なズレが発生することもあります。これらの問題を防ぐための対策を解説します。
ワークのズレを防ぐ固定方法
- クランプの締め付け圧を適切に設定する。強すぎるとワークが歪み、弱すぎると加工中にズレが発生するため、バランスが重要です。
- ワークの形状に合わせた専用の治具を使用することで、より安定した固定が可能になります。
機械の振動を抑える工夫
- マシニングセンターのベースがしっかりと固定されていることを確認します。特に大型の機械では、床の水平状態を定期的にチェックし、振動を抑える対策が必要です。
- 振動が多い環境では、防振マットやアンカーボルトを活用し、振動を吸収する工夫を行います。
工具の回転数と切削条件の調整
- 高回転での切削時に芯ズレが発生すると、工具の摩耗が進むため、適切な回転数に設定することが大切です。
- 深切削や高速加工を行う場合は、クーラントを適切に使用し、熱膨張による影響をできる限り抑えます。
まとめ
マシニング加工で高品質な仕上がりを実現するには、芯出しの精度が不可欠です。正確な芯出しにより寸法誤差を抑え、加工面の品質を向上できます。一方、芯ズレが生じると、加工不良や工具の摩耗が進み、生産効率が低下する可能性があります。
芯出しの精度向上には、ワークの固定、基準面の確認、環境管理が大切です。適切なバイスやクランプでワークの歪みを防ぎ、測定機器を活用して基準面を正しく設定することで、より安定した加工が可能になります。また、温度変化や機械の剛性を考慮し、振動対策を施すことで、芯ズレのリスクを軽減できます。
芯出しのトラブルを防ぐためには、測定手法の効率化と技術向上が欠かせません。ダイヤルゲージの誤差を抑え、自動芯出しシステムを活用することで、より精度の高い加工が実現できます。
弊社では、新しい精密加工機械を取り扱い、お客様のニーズに応じたより良い解決策を提案しております。新規導入を検討されている方には、専門スタッフが丁寧に対応し、技術的なご相談にも応じます。製品や導入に関するお問い合わせは、お気軽にご連絡ください。
お問い合わせ
弊社製品、加工についてのお問い合わせは、こちらで受付しております。
各部門のスペシャリストが、ご質問にお応えします。
電話
0574-54-2231
(平日 8:15~17:15)
FAX
0574-54-2235