- 2025/02/26
-
マシニングGコードとは?基本と活用法を解説
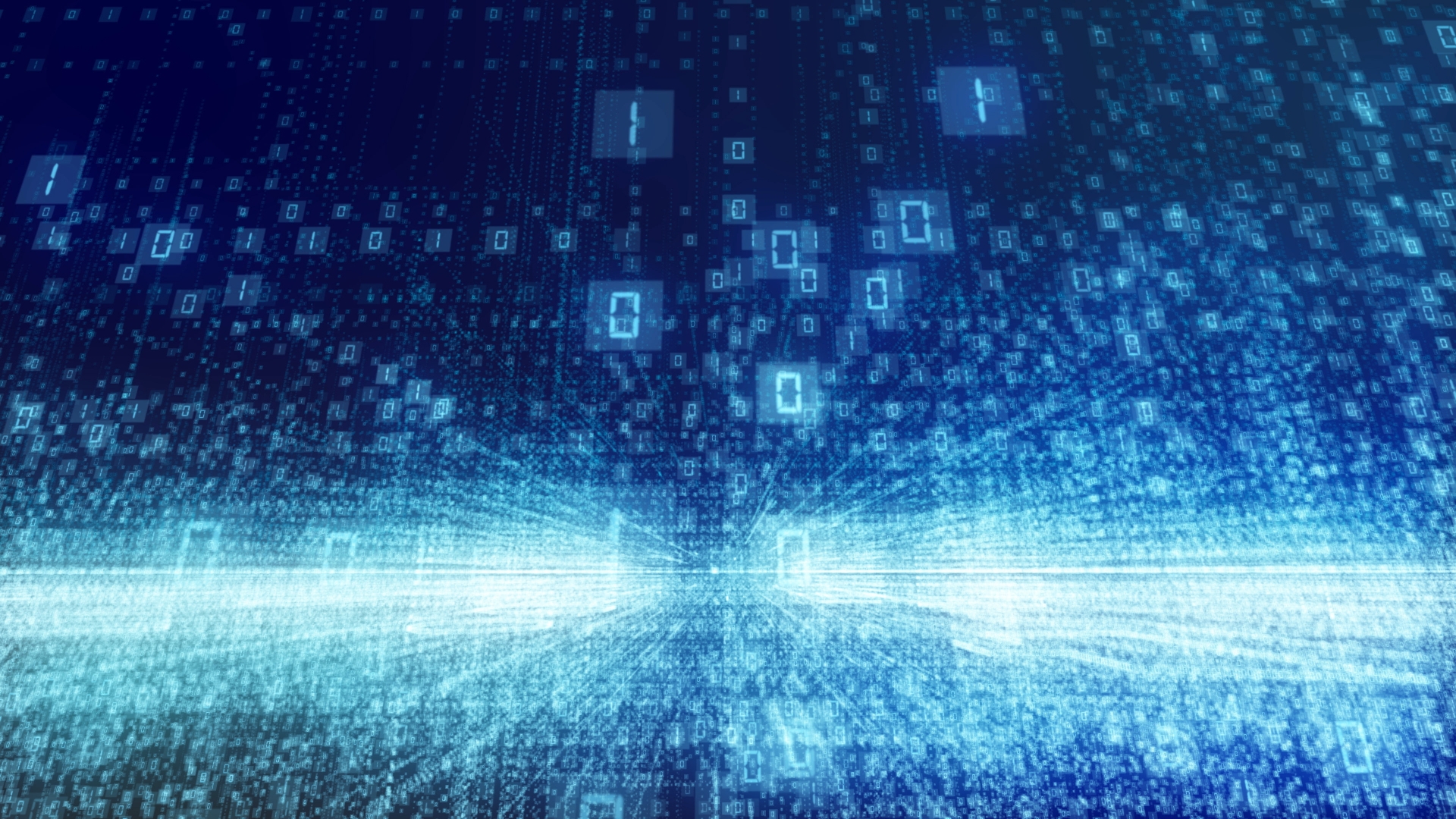
マシニングセンターを活用した精密加工には、Gコードの理解が欠かせません。NC工作機械を制御するためのプログラム言語として、Gコードは加工精度や作業効率を大きく左右します。特に初心者にとっては、「G00やG01って何?」「どのコードを使えば思い通りに加工できるのか?」といった疑問が生まれやすいものです。
本記事では、Gコードの基本構造から主要コマンドの使い方、実際の活用方法までを詳しく解説します。さらに、エラーを防ぐためのポイントやデバッグのコツについても紹介するので、マシニング初心者はもちろん、スキルアップを目指す方にも役立つ内容となっています。マシニング加工をより効率的に進めるために、Gコードをしっかり学びましょう。
マシニングセンターとGコードの基本
マシニングセンターは、精密加工に欠かせない工作機械のひとつです。加工プログラムに基づいて動作し、金属や樹脂などの材料を高精度で削り出すことが可能です。その制御において重要なのがGコードです。GコードはNC(数値制御)工作機械を動作させるためのプログラム言語であり、加工工程の指示を与える役割を果たします。ここでは、マシニングセンターの概要とGコードの基本について詳しく解説します。
マシニングセンターとは
マシニングセンターは、CNC(コンピュータ数値制御)を活用して自動で切削加工を行う工作機械です。従来の手動フライス盤とは異なり、プログラムを入力することで、複雑な形状や高精度な加工を効率的に実現できます。
マシニングセンターの主な特徴
特徴 | 内容 |
多軸加工が可能 | 3軸(X,Y,Z)や5軸加工にも対応し、複雑な形状の加工ができる |
自動工具交換機能(ATC) | 切削工程ごとに適切な工具へ自動で交換できる |
高精度な加工 | CNC制御により、ミクロン単位の精度で加工が可能 |
無人運転が可能 | プログラムを設定すれば、人が常時操作しなくても加工を続けられる |
こうした特徴により、マシニングセンターは航空機部品や自動車部品、精密機械部品の製造など、多岐にわたる分野で活用されています。
NC工作機械とGコードの関係
マシニングセンターを動かすためには、NC工作機械がGコードを読み取ることで制御を行う仕組みになっています。
- Gコードの指令を入力 → NC装置が解釈
- サーボモーターが動作 → スピンドルやテーブルを制御
- 工具が移動・切削を実行 → 指定された座標に従って加工
このように、GコードはNC工作機械の言語 であり、適切な記述がなければ正確な加工は実現できません。Gコードの知識があることで、より高度な加工やトラブル対応が可能になります。
Gコードとは
Gコード(G-code)は、NC工作機械を動作させるための命令コードです。Gコードの「G」はGeometric(幾何学的)を意味し、切削工具の移動や加工動作を指示します。Gコードを正しく設定することで、狙った形状に精密な加工を施すことが可能になります。
項目 | 説明 |
移動制御 | 工具の移動方法(直線・円弧・高速移動)を指定 |
切削速度の設定 | 適切な送り速度(F値)や回転速度(S値)を決定 |
座標設定 | ワークの基準点(G54~G59)を指定 |
加工方法の選択 | 穴あけ、フライス加工、タッピングなどを指示 |
GコードとMコードの違い
Gコードと併用されるMコード(Machine code) も重要です。Gコードは「工具の動作を決めるコード」であるのに対し、Mコードは「補助的な機械動作を制御するコード」です。
コード | 役割 | 例 |
Gコード | 加工パス・工具の動作制御 | G00(高速移動)、G01(直線補間) |
Mコード | 機械制御(主軸のON/OFFやクーラント操作) | M03(主軸正転)、M08(クーラントON) |
GコードとMコードを適切に組み合わせることで、精密で効率的な加工プログラムを作成できます。
主要なGコード(G00, G01, G02, G03 など)
Gコードには、工具の移動方法を指定するものがあり、基本となるのがG00・G01・G02・G03です。
コード | 動作 | 説明 |
G00 | 高速位置決め | 工具を指定座標へ短い距離で高速移動する(切削なし) |
G01 | 直線補間 | 指定座標へ直線的に移動しながら切削加工を行う |
G02 | 時計回りの円弧補間 | 円弧を時計回りに切削する(中心座標と半径を指定) |
G03 | 反時計回りの円弧補間 | 円弧を反時計回りに切削する |
これらの基本Gコードを使いこなすことで、精密な直線加工や円弧加工を実現できます。
マシニングセンターの動作を理解する上で、Gコードの基本を押さえることは必須です。本記事では、Gコードの役割やNC工作機械との関係、主要なGコードの種類について解説しました。Gコードを正しく理解することで、より高度な加工が可能になり、エラーを防ぎながら効率的なプログラム作成ができるようになります。次のステップとして、実際のGコードプログラム例を学び、より実践的な活用法を身につけていきましょう。
Gコードの基本構造
GコードはNC工作機械を制御するための命令群であり、工具の移動、加工方法、座標設定などを指示する役割を持ちます。適切にGコードを記述することで、意図した通りの加工を実現できます。ここでは、Gコードの記述方法と主要なコマンドについて詳しく解説します。
Gコードの基本フォーマット
Gコードは基本的に、複数の要素を組み合わせて1行の命令文として記述します。一般的なGコードのフォーマットは以下のようになります。
N100 G01 X100 Y50 Z-10 F300 S500
各要素の意味
要素 | 説明 |
N100 | 行番号(プログラムの順序を明確にするための番号) |
G01 | Gコード(この場合は直線補間の指示) |
X100 Y50 Z-10 | 座標(X100, Y50, Z-10 の位置まで移動) |
F300 | 送り速度(Feed rate:300mm/min) |
S500 | 主軸回転速度(Spindle speed:500rpm) |
このように、複数のパラメータを組み合わせて指令を出すことで、工具の動作を詳細に指定できます。
Gコードプログラムの構成
Gコードで記述されるNCプログラムは、ヘッダー、ボディ、エンドの3つのセクションに分かれています。
O0001 (プログラム番号)
N10 G21 G17 G90 G40 (ヘッダー設定)
N20 T1 M06 (工具交換)
N30 G00 X50 Y50 Z10 (位置決め)
N40 G01 Z-5 F200 (切削開始)
N50 G02 X100 Y50 R25 (円弧補間)
N60 G00 Z10 (工具退避)
N70 M30 (プログラム終了)
各セクションの役割
セクション | 内容 |
ヘッダー | 加工条件の設定(単位指定、座標系、工具交換など) |
ボディ | 実際の加工指令(工具移動、切削操作など) |
エンド | プログラム終了の指示(M30など) |
NCプログラムを正しく記述することで、誤動作を防ぎ、スムーズな加工を実現できます。
主要なGコード一覧
Gコードには多くの種類 がありますが、基本的なコマンドを押さえることで、スムーズにNC工作機械を扱えるようになります。ここでは、主なGコードを位置決め・移動系、座標系の設定、加工条件の設定の3つに分類して解説します。
位置決め・移動系
加工時の工具移動を制御するGコードには、高速移動・直線移動・円弧移動などがあります。
Gコード | 内容 | 説明 |
G00 | 高速位置決め | 工具を切削せずに、指定位置まで高速移動する |
G01 | 直線補間 | 指定した座標へ直線的に移動しながら切削を行う |
G02 | 時計回りの円弧補間 | 円弧を時計回りに描くように移動しながら切削 |
G03 | 反時計回りの円弧補間 | 円弧を反時計回りに描くように移動しながら切削 |
G00は非切削移動に使われ、加工中に使うのはG01, G02, G03です。特に円弧補間(G02, G03)は、円や曲線の加工に欠かせません。
座標系の設定
座標系の設定は、加工物の基準位置を決めるために重要な役割を果たします。
Gコード | 内容 | 説明 |
G17 | XY平面指定 | 加工の基準平面をXY平面に設定 |
G18 | ZX平面指定 | 加工の基準平面をZX平面に設定 |
G19 | YZ平面指定 | 加工の基準平面をYZ平面に設定 |
G54~G59 | ワーク座標系 | ワークの基準点を指定し、異なる加工原点を設定可能 |
G54~G59を使用することで、複数のワークを異なる原点で加工することが可能になります。また、G17, G18, G19を適切に使い分けることで、異なる方向での加工もスムーズになります。
加工条件の設定
加工時の基準となる値を決定するGコードには、絶対座標と相対座標の指定や、基準点の設定などがあります。
Gコード | 内容 | 説明 |
G90 | 絶対値指令 | 原点を基準に、指定座標へ移動 |
G91 | 相対値指令 | 現在位置を基準に、指定した距離分だけ移動 |
G92 | 位置決め | 任意の座標を新しい基準点として設定 |
G90とG91は、工具の移動方法を決める重要なコードです。G90は原点を基準とするため、位置指定が明確になりますが、G91を使うと現在位置を基準に相対的な移動が可能になります。G92は、ワークの途中で基準点を変更する際に便利です。
Gコードの基本構造を理解することで、より効率的なプログラム作成が可能になります。Gコードを適切に活用することで、精密な加工を実現し、作業効率を向上できます。
実際のプログラムに組み込む際には、誤ったGコードの指定がエラーや加工不良の原因になるため、シミュレーションや試験運転を行いながら調整すると良いでしょう。次のステップとして、具体的なGコードの活用事例やトラブルシューティングについても学んでいくと、より実践的なスキルが身につきます。
Gコードの活用例
Gコードを活用することで、マシニングセンターによる正確で効率的な加工が可能になります。初心者のうちは、単純な直線移動や穴あけのプログラムを作成することから始め、徐々に3D形状加工や多軸マシニングといった高度なプログラムへとステップアップしていくことが重要です。ここでは、基本的なGコードのプログラム例と、応用的な活用方法について解説します。
簡単なGコードのプログラム例(穴あけ、フライス加工)
初心者向けのGコードの書き方として、まず穴あけ加工とフライス加工の2つを紹介します。
穴あけ加工のGコード例
O1000 (穴あけプログラム)
N10 G21 G17 G90 (ミリ単位, XY平面, 絶対値指定)
N20 T1 M06 (工具交換:ドリル)
N30 G00 X50 Y50 Z10 (移動)
N40 G01 Z-10 F200 (穴あけ)
N50 G00 Z10 (工具退避)
N60 M30 (プログラム終了)
このプログラムでは、指定座標(X50, Y50)にドリルを移動し、Z-10の深さまで穴をあける動作を行います。G00とG01を使い分けることで、高速移動と切削動作を適切に制御しています。
フライス加工のGコード例
O2000 (フライス加工)
N10 G21 G17 G90 (ミリ単位, XY平面, 絶対値指定)
N20 T2 M06 (工具交換:エンドミル)
N30 G00 X20 Y20 Z5 (加工位置へ移動)
N40 G01 Z-2 F300 (切削開始)
N50 G01 X100 Y20 (直線切削)
N60 G01 X100 Y100 (直角に移動)
N70 G01 X20 Y100 (直線切削)
N80 G01 X20 Y20 (元の位置へ戻る)
N90 G00 Z10 (工具退避)
N100 M30 (プログラム終了)
このプログラムは、工具を使ってX20,Y20を起点に四角形を描くように切削するフライス加工の例です。G01を使用することで、指定座標へ直線移動しながら切削を行います。
実際の動作イメージ
Gコードの動作を確認する方法として、以下のような手段があります。
- NCシミュレーターを活用する
- 専用のシミュレーションソフトを使うと、Gコードを実際に動かす前に加工イメージを確認できます。
- 専用のシミュレーションソフトを使うと、Gコードを実際に動かす前に加工イメージを確認できます。
- マシニングセンターの試運転
- 加工ミスを防ぐため、エアカット(工具を空中で動かして確認)することが推奨されます。
- 加工ミスを防ぐため、エアカット(工具を空中で動かして確認)することが推奨されます。
- カットサンプルを用意
- いきなり本番の材料を使わず、安価な材料でテスト加工することでミスを減らせます。
これらの方法を取り入れることで、Gコードによる加工精度を高め、よりスムーズに作業を進められます。
Gコードを活用した応用加工
Gコードの基本を押さえたら、次のステップとして応用的な加工手法を学びます。ここでは、3D形状加工、多軸マシニング、高速・高精度加工のポイントについて解説します。
3D形状加工におけるGコードの活用
3D形状加工では、工具が複数の軸(X, Y, Z)を同時に動かしながら切削を行います。一般的にG02(円弧補間)やG03(反時計回りの円弧補間)を組み合わせることで、より滑らかな曲面加工が可能になります。3D加工のGコード例を紹介します。
N10 G21 G17 G90 (ミリ単位, XY平面, 絶対値指定)
N20 T3 M06 (工具交換)
N30 G00 X50 Y50 Z10 (加工位置へ移動)
N40 G01 Z-5 F200 (切削開始)
N50 G02 X100 Y50 R25 (円弧補間)
N60 G03 X50 Y50 R25 (反時計回りの円弧補間)
N70 G00 Z10 (工具退避)
N80 M30 (プログラム終了)
このプログラムでは、円弧補間を使用し、滑らかなカーブを描くように切削しています。3D形状を加工する際には、送り速度(F値)や回転数(S値)の効率化も重要になります。
多軸マシニングでのGコードの組み方
多軸マシニングでは、X, Y, Z軸だけでなく、回転軸(A軸、B軸、C軸)を活用することで、より複雑な加工が可能になります。
軸の種類 | 説明 |
X/Y/Z軸 | 水平・垂直移動(基本の3軸) |
A軸 | X軸回転 |
B軸 | Y軸回転 |
C軸 | Z軸回転 |
5軸加工機では、GコードにA軸やB軸を加えて記述することで、複雑な形状の加工が実現できます。
高精度加工のためのGコード設定
より高精度な加工を実現するためには、適切な送り速度、回転数、工具の選定が必要です。
設定 | 説明 |
F値(送り速度) | 適切な送り速度を設定し、ビビリ(振動)を防ぐ |
S値(主軸回転数) | 材料に応じた回転速度を設定 |
G05(高精度モード) | 加工精度を向上させる |
送り速度を適切に調整し、G05を活用することで高精度な加工が可能になります。
Gコードを活用すれば、基本的な穴あけやフライス加工から、高度な3D形状加工や多軸マシニングまで、さまざまな加工が可能です。
今後のステップとして、シミュレーションソフトを活用しながらGコードの理解を深め、より複雑な加工に挑戦していくことで、さらにスキルを向上できます。Gコードを自在に扱えるようになれば、マシニングセンターをより効率的に活用できるでしょう。
Gコードのトラブルシューティング
Gコードを使ったNC工作機械のプログラミングでは、ちょっとしたミスが加工ミスや機械トラブルの原因になることがあります。記述ミスや座標の誤設定、フィードレートの不適切な設定など、初心者が陥りやすいトラブルを防ぐためには、エラーの原因を理解し、適切なデバッグ方法を身につけることが重要です。ここでは、よくあるエラーとその対処法、そして効率的なデバッグの方法について解説します。
Gコードの記述ミスによるエラー
Gコードは正確に記述する必要がありますが、以下のような基本的なミスが原因でエラーが発生することがあります。
エラーの種類 | 説明 | 対処法 |
Gコードの記述ミス | 存在しないGコードを記述している | 使用可能なGコードを確認する |
数値の入力ミス | 小数点の抜けや桁数の間違い | コードのフォーマットを再確認 |
指令の矛盾 | G00とG01を同時に指定している | どちらか一方のみ使用する |
オーバートラベルエラー | 物理的に動けない座標を指定 | 工作範囲内に収めるよう調整 |
Gコードは1文字の間違いでも動作不良の原因になるため、入力したコードを慎重に確認することが大切です。
座標系の誤設定による問題
座標系を適切に設定していないと、工具の移動位置がずれてしまい、加工ミスにつながることがあります。
エラーの種類 | 原因 | 対処法 |
原点がズレている | ワーク座標(G54〜G59)が適切に設定されていない | 正しいワーク座標を確認する |
絶対座標と相対座標の誤設定 | G90(絶対座標)とG91(相対座標)を混同 | 使用する座標系を統一する |
工具オフセットの未設定 | 工具長補正が適用されていない | G43 H〇 で適切な補正を指定する |
座標系の誤設定を防ぐために、プログラム開始時に座標系(G54など)や工具オフセット(G43)を明示的に指定することが重要です。
フィードレートやスピンドル回転数の不適切な設定
切削加工では、送り速度(F値)や主軸回転数(S値)の設定が適切でないと、仕上がりや工具寿命に悪影響を与えることがあります。
設定ミス | 問題点 | 解決策 |
送り速度が速すぎる | 工具が折れたり、ワークが損傷する | 材料に適したF値を設定する |
送り速度が遅すぎる | 加工時間が長くなり効率が悪い | 適正なF値に調整する |
回転数が高すぎる | 工具が摩耗しやすくなる | 推奨S値を確認する |
回転数が低すぎる | 切削品質が悪化する | より良い切削条件に合わせる |
一般的に、材料や工具の種類に適したF値・S値の設定が加工品質を左右するため、加工マニュアルやメーカーの推奨値を参考にするのが望ましいです。
効率的なデバッグ方法
エラーを防ぐためには、効率的なデバッグ手法を活用し、加工前に問題点を発見することが大切です。
Gコードのエラーを事前に確認する方法として、シミュレーションソフトを活用すると効果的です。
シミュレーションを活用するメリット
- 加工ミスを事前にチェックできる
- 工具の動きを視覚的に確認できる
- 加工時間の効率化に役立つ
- 機械を実際に動かす前にプログラムのバグを修正できる
市販のNCシミュレーターや、CNCマシンメーカーが提供する専用ソフトを使うことで、より正確なデバッグが可能になります。
Gコードの手動確認ポイント
シミュレーションソフトがない場合でも、手動でGコードをチェックすることで、多くのエラーを未然に防ぐことが可能です。
チェック項目 | 確認内容 |
Gコードのフォーマット | 記述ミスや桁数の間違いがないか |
ワーク座標系の指定 | G54〜G59が正しく設定されているか |
送り速度・回転数 | 適切なF値・S値が設定されているか |
工具交換の指示 | 適切な工具が使用されているか(T〇 M06) |
エンドコマンドの記述 | M30などの終了コードが記述されているか |
Gコードは一行ずつ丁寧にチェックすることがトラブル回避の鍵となります。
初心者でもミスを減らせるチェックリスト
Gコードのプログラムミスを減らすために、初心者でも簡単に確認できるチェックリストを活用するのが効果的です。
Gコード記述時のチェックリスト
- Gコードの記述ミスがないか(存在しないコードを使っていないか)
- G90(絶対座標)とG91(相対座標)を適切に使い分けているか
- G54などのワーク座標系を正しく設定しているか
- F値(送り速度)が適切か(速すぎたり遅すぎたりしていないか)
- S値(回転数)が材料や工具に適しているか
- M30などの終了コードが適切に入っているか
- シミュレーションまたはエアカットで動作を確認したか
このようなチェックリストを活用することで、プログラムのエラーを未然に防ぎ、より安全かつ高精度な加工が可能になります。
Gコードを活用したNC工作機械の加工では、些細なミスが大きなトラブルを引き起こすことがあります。エラーを防ぐためには、シミュレーションソフトを活用し、手動チェックを怠らず、ミスを減らすためのチェックリストを実践することが大切です。初心者でも、正しい知識と適切な確認手順を身につければ、Gコードをスムーズに扱えるようになります。
まとめ
Gコードを適切に活用することで、マシニングセンターの性能をできる限り引き出し、高精度かつ効率的な加工を実現できます。本記事では、Gコードの基本構造からトラブルシューティングまで詳しく解説しました。正確なプログラム作成とエラーの回避によって、作業効率を向上させるだけでなく、工具や機械の寿命を延ばし、コスト削減にもつながります。
弊社では、新しい精密加工機械を取り扱い、お客様のニーズに合わせたより良い解決策を提案しております。新規導入を検討されている方には、専門スタッフが丁寧にご案内し、技術的なご相談にも対応いたします。製品の詳細や導入に関するご質問がございましたら、お問い合わせフォームよりお気軽にご連絡ください。
お問い合わせ
弊社製品、加工についてのお問い合わせは、こちらで受付しております。
各部門のスペシャリストが、ご質問にお応えします。
電話
0574-54-2231
(平日 8:15~17:15)
FAX
0574-54-2235