- 2025/02/26
-
マシニング加工とは?旋盤・フライスとの違いや治具の役割を解説
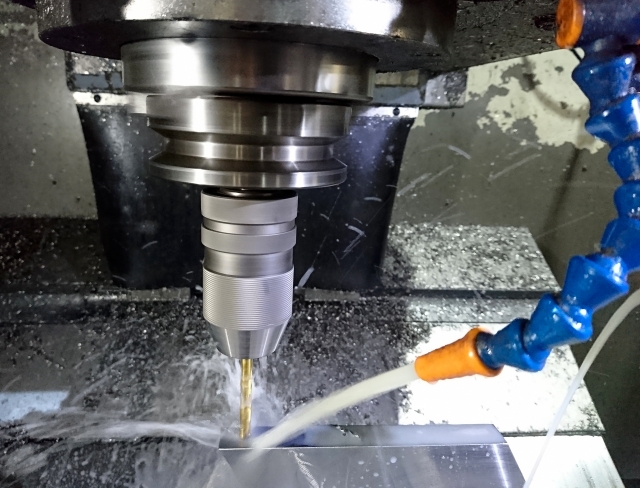
マシニング加工は、精密な部品を効率よく製造するために欠かせない加工技術の一つです。特に、金属や樹脂などの素材を高精度に削り出すことが求められる自動車・航空・医療・電子機器などの業界では、幅広く活用されています。しかし、旋盤やフライス盤とどのように違うのか、また、加工精度を向上させるための治具の役割について詳しく理解している方は少ないかもしれません。
この記事では、マシニング加工の基本から、旋盤やフライス盤との違い、さらには治具を活用するメリットについて詳しく解説します。加工方法を正しく理解し、用途に応じたより良い選択ができるようになれば、生産性向上やコスト削減にもつながるでしょう。
目次 [hide]
マシニング加工とは?
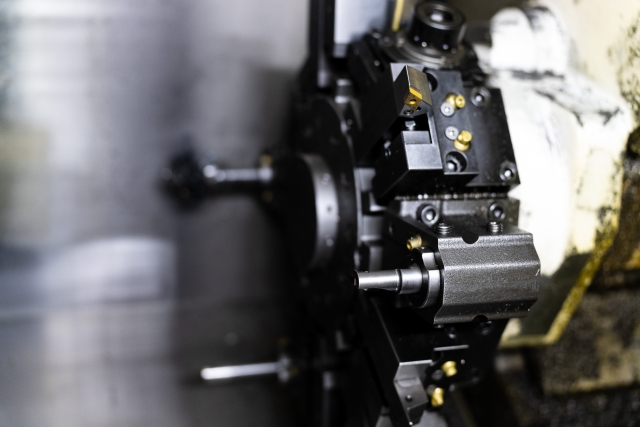
製造業において、金属や樹脂の部品を高精度で仕上げるためには、適切な加工技術が求められます。その中でも、マシニング加工は自動制御によって精密な切削を可能にし、多様な形状の部品を効率的に生産できる手法として広く活用されています。特に、大量生産が必要な工業製品や、高度な精度が求められる精密機器の製造には欠かせない技術です。
マシニング加工の基本概要
マシニング加工とは、数値制御(NC)を活用して、金属や樹脂といった多様な素材を精密に切削する加工技術のことです。この技術では、マシニングセンターと呼ばれる専用の工作機械を使用し、事前にプログラムされた指示に従って自動的に加工が進められます。人の手による作業とは異なり、高い精度を維持しながら一貫した品質の製品を大量に生産できる点が大きな特徴です。また、三次元的な加工も可能であり、複雑な形状の部品を効率よく製造できるため、多様な産業で不可欠な技術となっています。
マシニング加工の用途
マシニング加工は、さまざまな分野の製造工程において活躍しています。例えば、自動車業界では、エンジン部品やトランスミッションのギア、車体の補強パーツなどの精密加工が求められます。航空宇宙分野では、軽量かつ強度の高い材料を使用しながら、高精度で複雑な形状の機体部品やエンジンコンポーネントを製造する必要があります。
さらに、医療機器の製造においてもマシニング加工は不可欠です。人工関節や骨固定用のインプラント、精密な外科器具など、人体に直接関わる製品を製造する際には、誤差を極力抑えた高精度な加工が求められます。同様に、電子機器業界でもマシニング加工が広く活用されており、半導体関連の微細な部品や、放熱性を高めるための金属ケースの加工などに用いられています。
このように、マシニング加工は単なる金属の削り出しにとどまらず、現代のものづくりに欠かせない高度な技術として、多様な業界で必要とされています。加工精度の向上や自動化による生産性向上の観点からも、今後さらに発展が期待される分野といえるでしょう。
マシニング加工の特徴
高精度かつ安定した品質を維持しながら、大量生産にも対応できるのがマシニング加工の大きな強みです。従来の手作業による加工ではオペレーターの熟練度に依存する部分が大きかったのに対し、マシニング加工はプログラム制御による一貫した精密加工が可能です。また、さまざまな素材に対応し、複雑な形状の部品加工にも適応できるため、自動車や航空機、電子機器の製造など、多岐にわたる分野で活用されています。ここでは、マシニング加工の主な特徴について詳しく見ていきましょう。
NC制御による自動加工
マシニングセンターはNC(数値制御)を活用し、設計データを基にした高精度な加工を行います。オペレーターが直接操作する従来の手作業とは異なり、NCプログラムによる制御により、加工工程を自動化できるため、人為的な誤差をできる限り抑えられるのが特徴です。また、一度設定したプログラムを繰り返し使用できるため、製品の品質を均一に保ちながら大量生産を行うことが可能です。さらに、複雑な形状や精密な加工にも対応できるため、自動車や航空機、医療機器の部品製造など、高い精度が求められる分野で特に重宝されています。
多様な素材に対応
マシニング加工では、鉄やアルミニウム、ステンレス鋼、チタン合金といった金属をはじめ、耐熱性や強度が求められる特殊素材の加工にも対応しています。さらに、軽量で加工しやすい樹脂素材にも適応しており、電気絶縁性や耐薬品性が必要な部品の製造にも活用されています。こうした特性から、エレクトロニクス業界では電子部品の筐体やヒートシンクの加工に、医療業界では義肢やカテーテル部品の製造に採用されています。マシニング加工は、素材の特性に応じた適切な切削条件を設定することで、品質を維持しながら高効率な生産を実現できるのが強みです。
マシニングセンターの種類
マシニングセンターには、用途や加工対象のサイズに応じたさまざまな種類があり、それぞれ特有のメリットを持っています。
- 立形マシニングセンター
加工テーブルが水平方向に配置されたタイプで、比較的小型から中型の部品加工に適しています。視認性が高く、ツールの交換や調整がしやすいため、多品種少量生産に向いています。切削くず(チップ)が自然と下に落ちるため、切削面の視認性が良く、加工の進行状況を確認しながら作業を進めることが可能です。 - 横形マシニングセンター
水平に配置された主軸を持ち、ワークの側面から加工するのが特徴です。回転パレットを備えていることが多く、複数のワークを連続して加工できるため、大量生産に適しています。重力の影響で切削くずが加工面に残りにくく、精度を維持しやすい点も大きなメリットです。自動車や航空機の部品製造など、連続加工が求められる現場で多く使用されています。 - 門形マシニングセンター
大型の部品や高精度な加工を必要とするケースに適したタイプです。主軸が2本以上搭載されることが多く、複雑な形状の部品も高精度で加工できます。主に、大型の金型や航空機の機体パーツ、建設機械のフレーム加工などに使用されており、長尺ワークや高剛性が求められる加工にも対応できるのが特徴です。
このように、マシニングセンターは用途や加工対象に応じて適切なタイプを選ぶことで、効率的に生産を進められます。製造現場のニーズに合わせた機種を選定することで、生産性の向上やコスト削減につなげることが可能です。
マシニング加工における治具の役割
マシニング加工では、精度の高い加工を実現するために、ワーク(加工対象物)をしっかりと固定し、位置を正確に調整することが求められます。その際に重要となるのが「治具」と呼ばれる補助工具です。治具を適切に使用することで、作業効率が向上し、加工精度の安定化や生産性の向上が期待できます。また、同じ部品を繰り返し加工する場合にも、一貫した品質を確保するために欠かせない要素となります。
治具とは?
治具とは、加工時にワークを適切な位置に固定し、安定した加工を実現するための補助工具のことです。マシニング加工では、刃物の動きに対してワークがずれると、寸法精度や表面仕上げに影響を及ぼします。治具を使用することで、ワークのブレを防ぎ、正確な加工を行うことが可能になります。また、作業者の技量に依存せず、誰が加工しても均一な仕上がりが得られるため、大量生産の現場でも不可欠な存在となっています。
治具の種類
治具にはさまざまな種類がありますが、代表的なものとして「固定治具」と「位置決め治具」が挙げられます。
固定治具
固定治具は、ワークをしっかりと固定し、加工中に動かないようにするためのものです。強固に固定することで、切削時の振動を抑え、加工精度を向上させる役割を果たします。特に、大型のワークや高精度な加工が求められる部品では、適切な固定治具の使用が不可欠です。
位置決め治具
位置決め治具は、ワークを正確な位置にセットし、加工の再現性を高めるために使用されます。同じ部品を大量に生産する際、毎回ワークを手作業で位置調整すると誤差が生じやすくなりますが、位置決め治具を使うことで、常に同じ位置にワークを設置でき、寸法精度を確保できます。特に、マシニング加工では多軸の工具が異なる方向から加工を行うため、精密な位置決めが求められるケースが多くあります。
治具を活用するメリット
治具を適切に活用することで、以下のようなメリットが得られます。
- 加工精度の向上
ワークがしっかりと固定され、正確な位置にセットされるため、寸法誤差をできる限り抑えた加工が可能になります。 - 作業効率の向上とコスト削減
手作業での位置調整や固定作業にかかる時間を削減し、工程を効率化することで、生産スピードを向上できます。また、不良品の発生を抑えることで、材料の無駄を減らし、コスト削減にもつながります。 - 品質の均一化
同じ設計の部品を大量生産する際、治具を使うことで、加工精度にバラつきがなくなり、品質の安定化を図ることが可能です。特に、厳しい精度管理が求められる航空機部品や医療機器などの製造においては、治具の活用が不可欠となっています。
このように、治具はマシニング加工における大切な要素の一つであり、適切な選定と活用によって、加工の精度や効率を大幅に向上させることが可能です。
マシニングと旋盤の違い
旋盤とマシニング加工はどちらも金属や樹脂の加工に用いられますが、加工方法や適した形状、用途に大きな違いがあります。旋盤はワーク(加工対象物)を回転させながら切削し、円筒形状の加工に特化しているのに対し、マシニング加工は工具の方が動き、複雑な形状を削り出すことが可能です。それぞれの特徴を理解し、適切な加工方法を選択することで、製品の品質や生産効率を向上できます。
旋盤加工とは?
旋盤とは、ワークを回転させた状態で刃物を当て、削りながら形を整える工作機械のことを指します。円筒形状の部品を精密に加工するのに適しており、主に軸や円柱状の部品の製造に用いられます。旋盤の基本的な加工方法には、外径加工、内径加工、端面加工、ねじ切り加工などがあり、それぞれ異なる刃物を使用してワークを成形します。
例えば、自動車のシャフトやボルト、ナット、ベアリングの外側部分など、回転対称の形状が求められる部品の製造では旋盤が活躍します。また、旋盤は手動操作が可能なものから、CNC(コンピュータ数値制御)によって自動化されたものまであり、用途に応じた選択が可能です。
形状の違い
旋盤は円筒形状の加工に特化しており、ワークを回転させながら切削するため、基本的に丸みを帯びた形状の部品を作るのに適しています。一方、マシニング加工では工具の方が動き、X軸・Y軸・Z軸の3軸(またはそれ以上の軸)で制御できるため、立体的で複雑な形状の加工が可能です。例えば、四角い金属の塊を削ってギアやエンジン部品のような複雑な形状を作る場合、マシニングセンターが適しています。
加工工程の違い
旋盤加工ではワークが回転し、固定された刃物を当てることで削り出します。そのため、一定の円形断面を持つ部品を作るのに向いています。一方、マシニング加工は工具が移動しながらワークを削るため、直線的なカットや複雑な凹凸、穴あけ加工など、多様な加工が可能です。旋盤では実現できない形状でも、マシニング加工なら実現できることが多く、自由度が高いのが特徴です。
用途の違い
旋盤は、主に回転対称の部品を加工する際に使用されます。例えば、エンジンのクランクシャフトやピストン、ベアリングの軸など、円筒形のパーツが必要な場合に適しています。これに対し、マシニング加工は複雑な形状や多面加工が必要な部品に向いており、航空機の部品、精密機械のフレーム、電子機器のヒートシンクなどの製造に活用されています。
また、旋盤では主に円形の穴を開ける加工が得意ですが、マシニング加工では長方形や異形の穴を開けたり、ネジ穴や段差加工を施したりすることも可能です。そのため、設計の自由度が高く、さまざまな用途に対応できるのがマシニング加工の強みです。
項目 | 旋盤 | マシニング加工 | |
1. | 加工方法 | ワークを回転させながら刃物を当てる | 工具が移動しながらワークを削る |
2. | 適した形状 | 円筒形状 | 複雑な立体形状 |
3. | 工具の動き | 固定された刃物がワークに当たる | 工具がX・Y・Z軸方向に動く |
4. | ワークの動き | 回転する | 固定されている |
5. | 主な用途 | シャフト、ボルト、ベアリング、ナット | 航空機部品、精密機械フレーム、電子機器のヒートシンク |
6. | 得意な加工 | 外径加工、内径加工、端面加工、ねじ切り | 穴あけ、フライス加工、段差加工、異形の穴加工 |
このように、旋盤とマシニング加工は、それぞれ得意とする形状や加工方法が異なります。加工する部品の特性や求められる精度、生産量に応じて、より良い加工方法を選択することが大切です。
マシニングとフライス盤の違い
フライス盤とマシニングセンターは、どちらも工具を回転させてワークを削る機械ですが、自動化の度合いや対応できる加工の範囲には大きな違いがあります。フライス盤は比較的シンプルな操作で単品加工や試作品の製作に適している一方、マシニングセンターはNC(数値制御)を活用し、複雑な形状の部品を精密かつ効率的に加工するのに適しています。
フライス盤とは?
フライス盤とは、回転するカッターを使ってワークの表面を削り取る加工機械です。主に直線的な加工や平面加工に用いられ、単品の部品や試作品の製作に適しています。フライス盤には、作業者が手動で操作する汎用フライス盤と、NC(数値制御)によって自動で加工を行うNCフライス盤があります。
汎用フライス盤は、作業者のスキルに依存するため熟練が必要ですが、小ロット生産や試作品の加工では高い柔軟性を発揮します。一方、NCフライス盤は、数値制御によって同じ形状の部品を精密に加工できるため、ある程度の量産にも対応可能です。
マシニング加工との比較
比較項目 | フライス盤 | マシニングセンター |
自動化レベル | 手動操作の汎用フライス盤とNC制御のフライス盤がある | NC(数値制御)による完全自動化 |
対応できる加工 | 比較的単純な形状の加工(平面、溝、穴あけなど) | 多軸制御により複雑な3D形状や高精度な加工が可能 |
精度 | 作業者のスキルに依存するため、精度にばらつきが出ることもある | NCプログラムによる制御で一貫した精度を維持 |
生産性 | 小ロットや試作向き | 量産に適しており、自動化で高い生産性を発揮 |
操作性 | 手動操作が可能なため、細かい調整が容易 | プログラムが必要で、操作には専門知識が必要 |
主な用途 | 試作部品、少量生産の加工 | 自動車部品、航空機部品、大量生産が必要な精密機械部品 |
どちらを選ぶべきか?
フライス盤とマシニングセンターは、それぞれの特性に応じて適した用途があります。
- フライス盤が適しているケース
- 試作や単品加工が多い場合
- 手作業での微調整が必要な加工
- 加工コストを抑えつつ少量の部品を製作したい場合
- マシニングセンターが適しているケース
- 精度の高い大量生産が求められる場合
- 形状が複雑で多面的な加工が必要な場合
- 人手を減らし、自動化による生産効率向上を図りたい場合
フライス盤とマシニングセンターにはそれぞれ得意とする加工が異なります。加工する部品の仕様や生産量に応じて、適切な機械を選択することが大切です。
マシニングセンターとフライス盤の違いについては、「マシニングとフライスの違いとは?加工の特徴と使い分けを解説」で詳しく解説しているので、こちらの記事を参考にしてください。
マシニング加工の活用事例
マシニング加工は、高い精度と安定した品質が求められる分野で幅広く活用されています。特に、自動車産業や航空・宇宙産業、医療機器・電子部品の製造などでは、部品の複雑な形状や厳密な寸法精度が求められるため、マシニングセンターによる加工技術が不可欠です。ここでは、それぞれの分野における具体的な活用事例について詳しく見ていきましょう。
自動車部品の製造
自動車産業では、エンジンや駆動系、シャシー部品など、精密な金属加工が必要な部品が数多く存在します。特に、エンジンのシリンダーブロックやトランスミッション部品の加工では、厳格な寸法精度と表面仕上げが求められます。これらの部品はエンジン性能や燃費、耐久性に大きく影響を与えるため、ミクロン単位の精度での加工が必須となります。
また、サスペンションアームやステアリング部品などの安全に関わるパーツも、マシニング加工によって高精度に仕上げられています。これらの部品は耐久性や剛性が求められるため、アルミ合金や高張力鋼などの難削材を使用することが多く、マシニングセンターによる精密加工が欠かせません。
航空・宇宙分野での精密加工
航空機や宇宙産業では、部品の軽量化と高い強度が求められるため、アルミ合金、チタン合金、炭素繊維強化プラスチック(CFRP)などの特殊な素材を使用した部品が多くなります。
例えば、航空機のフレーム構造部品やエンジンコンポーネントは、複雑な形状を持ちながらも極めて高い寸法精度が求められるため、マシニングセンターによる精密な加工が行われます。また、航空機の主翼や尾翼に使われるアルミ合金のリブやスパー(補強材)も、軽量化と強度のバランスを取るため、細かい肉抜き加工や複雑な形状が施されており、マシニング加工技術が不可欠です。
宇宙分野においても、人工衛星やロケットの機体部品、燃料供給系のバルブや継手部品など、超高精度な加工が必要な部品が多く、マシニング加工の精度と安定性が重要な役割を果たしています。
医療機器・電子部品の製造
医療分野では、人体に使用するインプラントや外科手術器具の製造において、厳格な品質管理と高精度な加工が求められます。例えば、人工関節や骨固定プレート、インプラント用のスクリューなどは、生体適合性の高いチタンやコバルトクロム合金などを使用し、精密な形状を削り出す必要があります。これらの医療機器は、患者ごとに異なる形状が求められるケースも多いため、マシニングセンターによるカスタム加工が活用されています。
また、電子部品の分野では、半導体関連部品や放熱性を高めるヒートシンク、微細なコネクタ部品などの製造にマシニング加工が利用されています。特に、電子機器の小型化・高機能化が進む中で、微細な溝や穴加工、極薄の切削加工が求められる場面が増えており、高精度なマシニング技術の重要性が高まっています。
まとめ
マシニング加工は、精密な部品の製造を支える重要な技術として、自動車、航空・宇宙、医療機器、電子部品など幅広い分野で活用されています。数値制御による高精度な加工が可能であり、複雑な形状や多様な素材にも対応できることが特徴です。特に、近年では加工精度の向上や生産性向上を目的とした新しい工作機械が次々と登場し、製造業のさらなる発展を支えています。
新しい精密加工機械を取り扱い、お客様のニーズに合わせたより良い解決策を提案しております。新規導入を検討されている方には、専門スタッフが丁寧にご案内し、技術的なご相談にも対応いたします。製品の詳細や導入に関するご質問がございましたら、お問い合わせフォームよりお気軽にご連絡ください。
お問い合わせ
弊社製品、加工についてのお問い合わせは、こちらで受付しております。
各部門のスペシャリストが、ご質問にお応えします。
電話
0574-54-2231
(平日 8:15~17:15)
FAX
0574-54-2235