- 2024/04/01
-
工作物の熱処理法!初心者でもわかる基礎知識
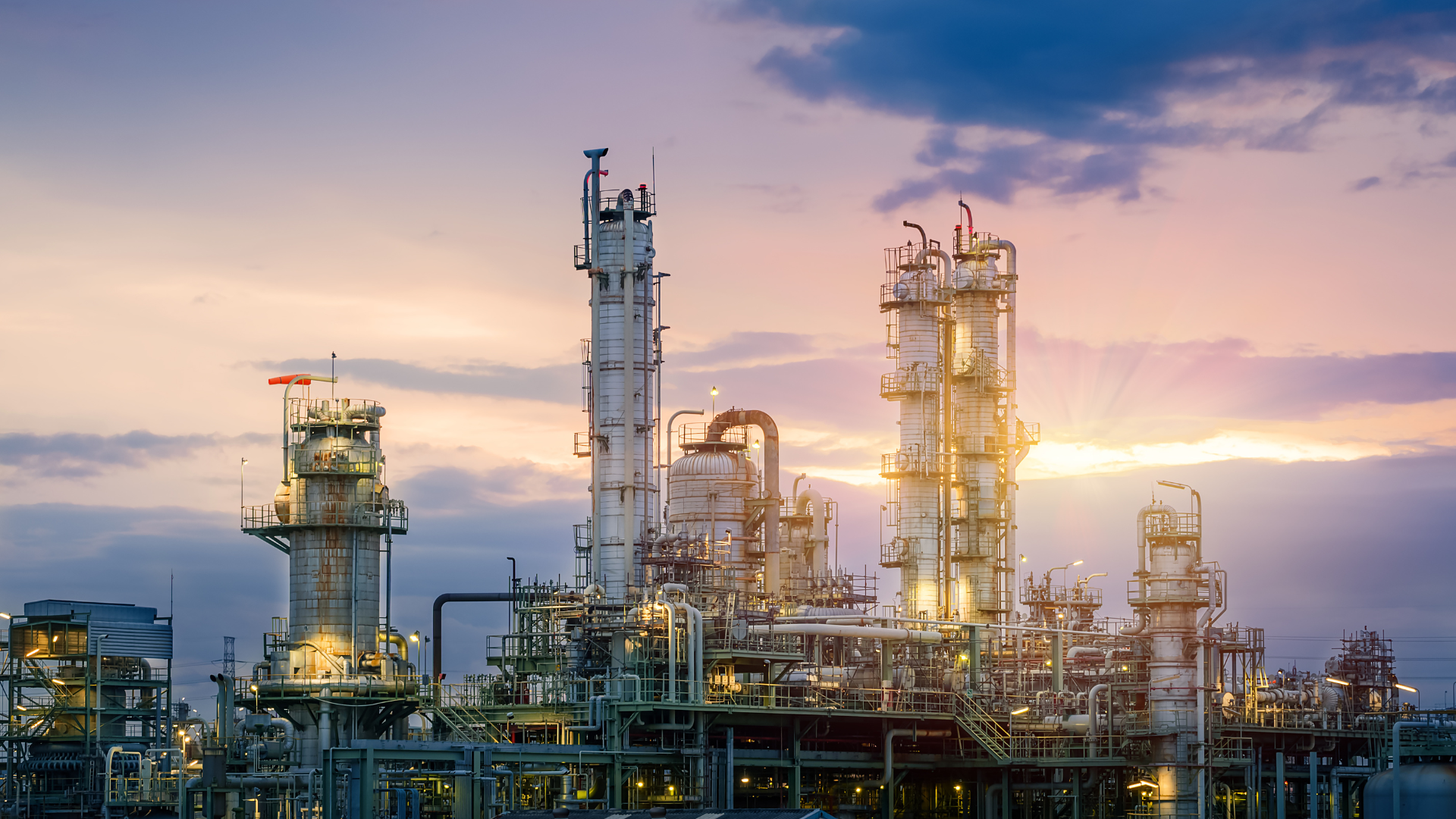
熱処理は、材料を所定の温度まで加熱し、冷却条件を制御することで、強度や硬度、靱性などの特性を大きく変化させる重要な技術です。金属部品をはじめ多様な工作物に適用され、製品の耐久性や性能を飛躍的に向上させる役割を担っています。本記事を参考に、工作物に合った最適な熱処理を選択するための基本的な考え方を学びましょう。
目次 [hide]
工作物と熱処理法の基本
熱処理法は、工作物の特性を大きく左右する重要な技術です。まずは、熱処理法の概要や、そもそもなぜ工作物に熱処理が必要なのかを押さえることで、基礎知識を固めましょう。
熱処理法とは?
熱処理法とは、材料を一定の温度に加熱し、冷却方法を制御することで、強度や硬度、靱性などの特性を変化させる加工技術です。金属部品をはじめ、多様な工作物に適用され、製造現場では欠かせない工程の一つです。
なぜ熱処理が必要なのか
材料そのものの特性だけでは、使用環境に十分対応できない場合があります。そこで熱処理を行うことで、必要な強度や耐摩耗性、靱性などを付与し、製品の性能向上や寿命延長が期待できます。
熱処理の基本プロセス
熱処理では、加熱と冷却の条件を変えることで素材の性質を制御します。ここでは、変態点や温度・時間管理の考え方など、工程を理解する上で必須となる基本プロセスを説明します。
加熱と冷却のメカニズム
熱処理では、素材を特定の温度まで加熱し、その後の冷却速度を調整します。適切な加熱温度と冷却法を組み合わせることで、結晶構造を意図的に変化させ、所望の特性を得られます。
温度・時間管理と変態点
金属は、一定の温度帯を超えると結晶構造が変化(変態)します。変態点を踏まえた温度・時間の管理は、熱処理成功のカギです。設定値のわずかなズレでも、硬度や靱性が大きく変わる場合があります。
材料特性の変化
熱処理によって、材料の脆さを改善し、靱性や硬度を高められます。ただし、過度な焼入れは割れの原因にもなるため、焼き戻しなどの調整工程を組み合わせることが重要です。
熱処理法の種類と特徴
焼入れ・焼き戻し、焼きなまし・焼きならし、特殊な表面硬化処理など、熱処理には多彩な手法があります。それぞれの特徴を知ることで、求める物性に合わせた最適な方法を選択できるようになります。
焼入れ・焼き戻し
焼入れは、高温に加熱後急冷して硬度を上げる手法です。ただし脆くなるため、焼き戻しで適度に応力を除去し、靱性を回復させるのが一般的な流れです。
焼きなまし・焼きならし
焼きなましは、ゆっくりと冷却して材料を軟化させ、加工性を高める方法です。焼きならしは組織を均一化し、強度や靱性をバランスよく向上させます。
特殊な熱処理
浸炭や窒化など、表面だけを硬化させる方法や、真空中で処理する方法など、素材・用途に応じて多彩な手法が存在します。
熱処理法の具体的な手法
全体焼入れや部分焼入れ、浸炭焼入れ・真空焼入れなど、実際にどのように行われるかを詳しく見ていきます。材質別の留意点も含め、作業現場での具体的な適用例を学びましょう。
全体焼入れ/部分焼入れ
素材全体を焼入れする方法と、必要箇所のみを局所的に硬化させる部分焼入れがあります。炎焼入れや高周波焼入れは、表面に集中して熱を加える代表的な例です。
浸炭焼入れ/真空焼入れ
浸炭焼入れは、表面に炭素を浸透させて外側を硬くし、内部は粘り強さを保ちます。真空焼入れは、酸化や脱炭を抑えながら高精度な処理が可能です。
材質別の留意点
炭素鋼は、炭素量により硬化しやすさが異なり、合金鋼は添加元素の影響で熱処理温度が変化します。ステンレスなどは焼入れ可能な系統と不可能な系統があるため、材質に応じた選択が欠かせません。
熱処理の効果と利点
熱処理を行うことで、機械的特性や耐久性、成形性などが大きく改善されます。ここでは、製品寿命の延伸や耐食性の強化など、熱処理がもたらすさまざまなメリットを整理します。
機械的特性の向上
熱処理によって硬度や引張強度が高まり、製品の耐摩耗性や耐衝撃性が向上します。これにより、部品の寿命が大幅に伸びることも少なくありません。
耐久性と耐食性の強化
焼入れや浸炭といった表面硬化処理は、摩擦部品の耐久性を飛躍的に高めます。また、真空熱処理などを活用すれば、酸化や錆を抑制し、耐食性をアップさせる効果も期待できます。
成形性や加工性の改善
焼きなましのように、素材を軟化させる処理を行えば加工しやすくなり、切削性も高まります。最終的な形状を効率よく成形するために、適宜熱処理を挟むことが有効です。
熱処理における品質管理
正確な温度管理や製品検査を行わないと、割れや変形といったトラブルに直結します。品質管理の重要性と、硬さ試験や金相観察などの検査手法、トラブルシュートのポイントを確認しましょう。
温度管理の重要性
炉内の温度が不均一だと、仕上がりにムラが生じます。サーモカップルなどを用いて正確に測定・制御することが、不良品を減らすポイントです。
品質検査のポイント
硬さ試験や金相観察、寸法測定など、多角的な検査が必要です。特に焼入れ後は、歪みや割れが発生していないかの確認が重要になります。
トラブルシューティング
割れ、酸化、変形といった問題は、温度管理ミスや急冷のタイミングなどが原因となる場合が多いです。プロセスを再検証し、問題箇所を迅速に特定することが大切です。
熱処理の応用分野
自動車、鉄鋼、電子部品など、多種多様な業界が熱処理を活用しています。具体的な事例を通じて、各分野でどのように熱処理技術が活かされているかを理解しましょう。
自動車産業での活用
エンジン部品やギアなどの駆動系部品を中心に、多数の熱処理工程が組み込まれています。高強度かつ軽量な素材を利用するため、適切な熱処理が不可欠です。
鉄鋼業界での応用
鋼板の製造や特殊鋼の生産など、熱処理は素材の基本性能を高める要となります。大規模設備を使い、大量生産に対応できるプロセスが整っています。
電子部品や精密機器製造での利用
小型かつ高精度が要求される電子機器の分野でも、熱処理により薄肉部品の硬度確保や寸法安定性向上が図られます。
まとめ
熱処理は、工作物の性能を大幅に向上させる重要な工程です。加熱・冷却のメカニズムや温度管理を正しく理解し、目的に合った手法を選択することが肝心です。焼入れ・焼き戻し、焼きなましなど多彩な処理法があり、材質や使用環境に応じて使い分けることで、高強度化や耐久性向上、加工性の改善が期待できます。
品質管理や最新技術を活かしながら、今後も環境や安全への配慮を忘れずに、最適な熱処理プロセスを追求していくことが求められます。
お問い合わせ
弊社製品、加工についてのお問い合わせは、こちらで受付しております。
各部門のスペシャリストが、ご質問にお応えします。
電話
0574-54-2231
(平日 8:15~17:15)
FAX
0574-54-2235