- 2024/04/19
-
精密部品の鉄とステンレス違いとそれぞれの特徴を徹底解説

精密部品の選定において重要な要素の一つは、使用する材料です。特に鉄とステンレスはその特性から広く利用されていますが、どのような違いがあるのでしょうか。
本記事では「精密部品における鉄とステンレスの違い」を、組成や強度、耐久性から、耐食性、加工性、使用用途に至るまで、さらに適切な材料選定のポイントも徹底解説します。
精密部品に使用される鉄とステンレス8つの違いと特徴

重要な素材である鉄とステンレス。素材を詳しく比較し、それぞれの特性を理解することで、最適な選定に繋がります。 詳しく見ていきましょう。
1.基本的な組成の違い
- 鉄: 主に鉄元素から成り、炭素やその他の微量元素が含まれます。鉄の純度や炭素含有量により、さまざまな鋼材が生成されます。
- ステンレス鋼: 鉄を基に、10.5%以上のクロム(Cr)を含む合金で、ニッケル(Ni)やモリブデン(Mo)も添加されることが多いです。クロムが耐腐食性を向上させます。
2.強度と耐久性
- 鉄: 高い引張強度を持ち、重機や建築資材として広く使用されてますが、腐食に弱いため表面処理が必要です。
- ステンレス鋼: 強度があり、耐腐食性が高く、過酷な環境下でも長期間使用できます。
3.硬度と耐熱性
- 鉄: 比較的柔らかく加工しやすいです。熱処理により硬度を高めることが可能です。
- ステンレス鋼: 高い硬度と耐熱性を持ち、高温下でも強度を維持します。
4.熱伝導率
- 鉄: 比較的高い熱伝導率を持ち、熱を迅速に分散します。
- ステンレス鋼: 熱伝導率は低く、熱を保持するため、調理器具など特定の用途において有利です。
5.耐食性
- 鉄: 水分や酸素にさらされると錆びやすく、耐食性が低いです。
- ステンレス鋼: クロム成分が酸化被膜を形成し、耐食性が高いです。しかし、完全にさびないわけではなく、例えば、塩水や酸性環境などの特定の条件下では腐食する可能性があります。
6.電気伝導率
- 鉄: 一般的な導電性金属よりは低いです、ステンレスより高いです。電気機器やモーターに広く使用されます。
- ステンレス鋼: 電気抵抗が高く、一般的には電気を通しにくいです。
7.リサイクル
- 鉄: リサイクルが非常に一般的で、コスト効率が高いです。
- ステンレス鋼: 高価な特性から回収・再利用が進んでいます。
8.加工のしやすさ
- 鉄: 加工しやすく、切削や曲げ、溶接が容易です。特に炭素鋼(例:S45C)は加工性が優れています。
- ステンレス鋼: 高い硬度により加工が難しいですが、オーステナイト系(例:SUS304)は比較的加工しやすいです。フェライト系やマルテンサイト系は特殊な技術が必要となります。
鋼材の特性と加工性の比較
鋼材の種類 | 硬度 | 切削性 | 成形性 | 具体例 |
---|---|---|---|---|
炭素鋼(例:S45C) | 比較的高い | 切削加工が容易で、工具の摩耗が少ない | プレス加工や鍛造に適している | ボルトやナット、シャフト、歯車などの部品 |
オーステナイト系ステンレス鋼(例:SUS304, SUS316) | 比較的柔らかいが、加工硬化性が高い | 加工が難しく、低速加工が必要 | 高い延性を持ち、プレス加工が可能 | キッチン用品、建築用材料など |
フェライト系ステンレス鋼(例:SUS430) | オーステナイト系より高いが、マルテンサイト系ほどではない | やや加工しやすいが、脆性が生じやすい | 延性が低く、プレス加工にはやや向いていない | 家庭用電化製品、厨房機器、自動車の排気系部品 |
マルテンサイト系ステンレス鋼(例:SUS410) | 非常に高い | 切削が非常に難しく、高精度の工具が必要 | 成形加工が難しく、鍛造やプレス加工には適していない | バルブやポンプ部品など |
二相系ステンレス鋼(例:SUS329J1) | フェライト系とオーステナイト系の中間 | やや難しく、高精度の加工技術が必要 | 成形は可能だが、難易度が高い | 石油・ガス産業、化学工業、海洋構造物 |
析出硬化系ステンレス鋼(例:SUS630) | 溶体化処理後は柔らかいが、時効処理後は非常に高い | 時効処理後の切削は非常に難しく、精度が要求される | 溶体化処理後は成形可能だが、時効処理で硬度が増加 | 海洋環境や化学プラント、航空宇宙産業など |
【鉄】精密部品の材料としての特徴
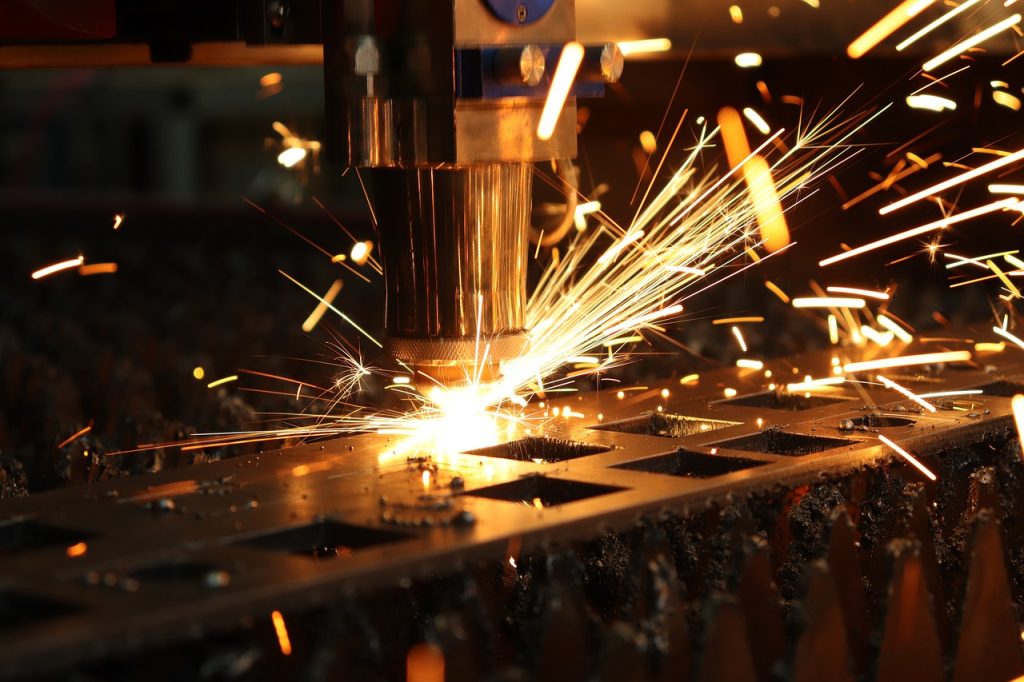
鉄の最大の特徴は、強度と耐久性が高い点です。その他、鉄に関する事を、もう少し詳しく見ていきましょう。
鉄の耐久性と環境への影響
鉄は、非常に耐久性が高い材料です。 そのため、長期間にわたって使用される製品に適しています。しかし、錆びやすいという欠点もあります。 そのため、適切な表面処理が求められます。 また、鉄の製造過程で発生するCO2排出量は多いため、環境への配慮も重要です。
鉄の加工性と製造コスト
鉄は、加工性に優れているため、さまざまな形状に成形することが可能です。 さらに、鉄は熱処理により物理特性を向上させることができます。 そして、鉄の加工方法として、鋳造、鍛造、圧延などが一般的です。 また、これらの加工方法は比較的コストが低く、製造コストを抑えることができます。 一方で、特殊な加工には高い技術が求められるため、製造コストが上昇する場合もあります。
鉄の表面処理と仕上げ方法
鉄の表面処理は、耐久性や美観を向上させるために非常に重要です。 一般的な表面処理方法として、メッキ、塗装、熱処理などが挙げられます。 メッキは耐蝕性を高め、塗装は防食と装飾効果を兼ね備えています。 さらに、熱処理は硬度や耐摩耗性を向上させます。 これにより、使用場面に応じた最適な仕上げを施すことが可能です。 適切な表面処理を選択することで、製品の寿命を延ばし、品質を保つことができます。
種類が豊富な材質と規格形状
鉄は、さまざまな材質と規格形状が存在します。 一般に使用される鋼材には、炭素鋼やステンレス鋼などがあり、それぞれに特性が異なります。 また、形状についても、鋼板、棒鋼、角鋼など多岐にわたります。 規格形状が豊富であるため、特定の用途に最適な材質と形状を選択することが可能です。 これにより、製品の性能を最大限に発揮させることができます。 使用する場面や必要な性能に応じて、適切な鉄材を選ぶことが求められます。
ステンレスの種類
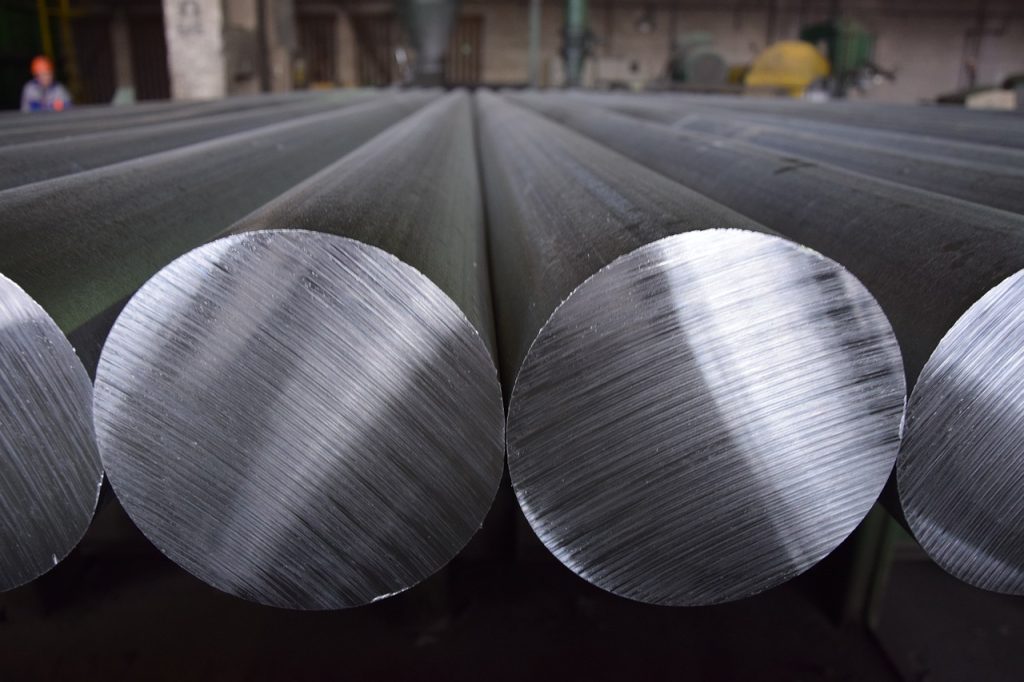
ステンレスは、多くの分野で使用される金属材料です。さまざまな成分や構造によって、異なる特性を持つ複数の種類に分類されます。先述の「8つの違いと特徴」でも登場したステンレスの種類についてより深く見ていきましょう。
1. オーステナイト系ステンレス鋼 (Austenitic Stainless Steel)
- 代表的な鋼種: SUS304, SUS316, SUS321
- 主な成分: 鉻 (Cr) 16-26%、ニッケル (Ni) 8-22%
- 特性: 優れた耐食性と靭性を持つ 非磁性(磁気を帯びない) 高温・低温に強い 溶接性が良い
- 用途: 化学プラント、食品加工設備、建築用外装材、厨房機器
2. フェライト系ステンレス鋼 (Ferritic Stainless Steel)
- 代表的な鋼種: SUS430, SUS409, SUS439
- 主な成分: 鉻 (Cr) 10.5-30%、炭素 (C) 0.12%以下
- 特性: 中程度の耐食性 磁性あり 熱膨張が低い 溶接性が劣る 高温でのクリープ特性が良い
- 用途: 自動車部品、家電製品の部品、装飾品、耐熱機器
3. マルテンサイト系ステンレス鋼 (Martensitic Stainless Steel)
- 代表的な鋼種: SUS420, SUS410, SUS440C
- 主な成分: 鉻 (Cr) 12-18%、炭素 (C) 0.1-1.2%
- 特性: 高硬度で耐摩耗性に優れる 耐食性はオーステナイト系やフェライト系よりも低い 磁性あり 焼入れ処理が可能で、強度が向上する
- 用途: 刃物、工具、タービンブレード、バルブ部品
4. 二相系ステンレス鋼 (Duplex Stainless Steel)
- 代表的な鋼種: SUS329J1, SUS2205, SUS2507
- 主な成分: 鉻 (Cr) 21-26%、ニッケル (Ni) 4.5-7%、モリブデン (Mo) 2-3.5%
- 特性: 高い耐食性と強度を兼ね備える オーステナイト相とフェライト相が混在 耐応力腐食割れ性が高い 溶接性が比較的良好
- 用途: 石油・ガス産業、化学プラント、海洋構造物、熱交換器
5. 析出硬化系ステンレス鋼 (Precipitation Hardening Stainless Steel)
- 代表的な鋼種: SUS630 (17-4PH), SUS631 (17-7PH)
- 主な成分: 鉻 (Cr) 15-17.5%、ニッケル (Ni) 3-7%、銅 (Cu) 1-5%
- 特性: 高強度かつ高硬度 熱処理により硬化する 磁性あり 耐食性はオーステナイト系より劣るが、マルテンサイト系よりは優れる
- 用途: 航空宇宙部品、精密機械部品、シャフト、バルブ部品
【ステンレス】精密部品の材料としての特徴
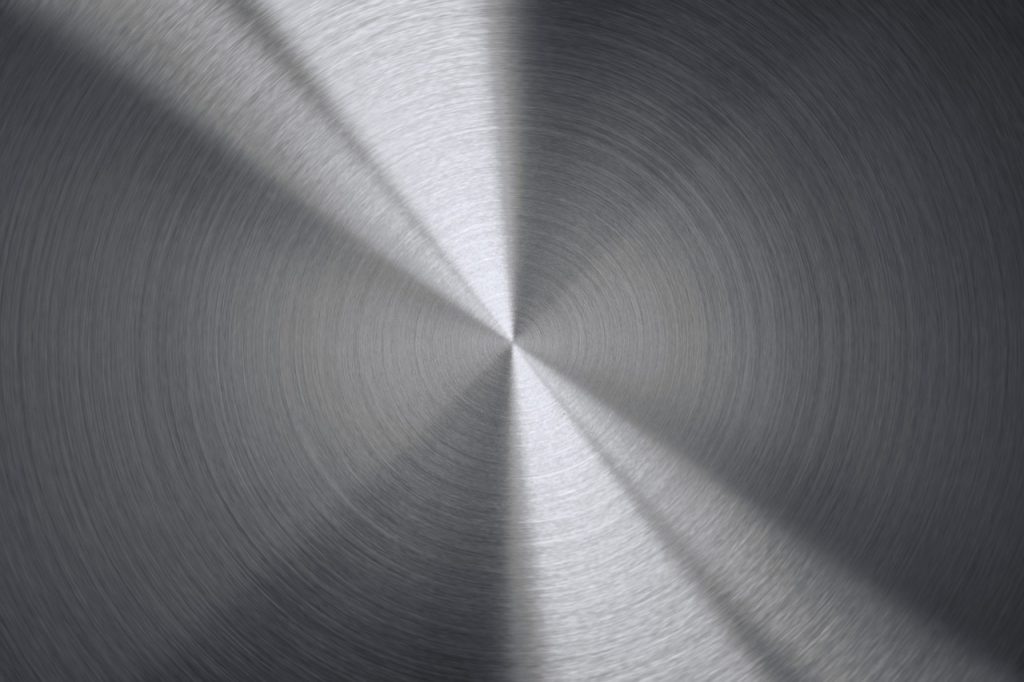
ステンレスの最大の特徴は、その優れた耐食性です。クロムを含むため、腐食に強く、特に過酷な環境下でも長期間にわたり高い性能を発揮します。加工の難しさはありますが、その特性により様々な用途で使用されています。
ステンレスの強度
ステンレスは高い強度を持つため、薄くても十分な強度を保てます。 構造材や部品として高い評価を得ており、 特に航空機や自動車などの軽量化が求められる分野では重宝されます。 さらに、その強度が維持されるため、耐久性も確保できます。
ステンレスの溶接性と製造方法
精密部品のステンレスの溶接はステンレスの種類によって難易度が異なります。 種類に応じた具体例や溶接技術について詳細を見ていきましょう。
オーステナイト系ステンレス鋼(例:SUS304, SUS316)
- 溶接性: 溶接が非常にしやすく、溶接後の機械的性質の変化が少ないため、広く使用されています。高い靭性と延性を保ちながら、熱影響部の脆化を避けることができます。また、溶接後の割れのリスクも低く、特別な前処理や後処理が不要な場合が多いです。
- 具体的な溶接技術: TIG(タングステンイナートガス)溶接やMIG(メタルイナートガス)溶接がよく使われます。薄肉材の溶接にも適しており、特に精密部品の製造に向いています。
フェライト系ステンレス鋼(例:SUS430)
- 溶接性: 溶接がやや難しく、熱影響部で結晶粒の成長や脆化が生じやすいことがあります。溶接後に靭性が低下するリスクがあり、また、特定の条件下では応力腐食割れのリスクも増加します。
- 具体的な溶接技術: 溶接時には低熱入力で短時間での溶接を心がけることが重要です。前処理として、溶接部を適切に清掃し、後処理として徐冷や低温焼鈍を行うことがあります。
マルテンサイト系ステンレス鋼(例:SUS410)
- 溶接性:溶接後に硬化する性質があり、溶接後の割れや変形が生じやすいため、非常に慎重な技術が求められます。溶接中や溶接後に適切な熱処理が行われないと、硬くて脆いマルテンサイト組織が形成され、割れが発生するリスクが高まります。
- 具体的な溶接技術:事前の予熱(150〜300℃)と溶接後の徐冷や焼鈍が重要です。溶接中の低熱入力を保つことも求められます。
二相系ステンレス鋼(例:SUS329J1)
- 溶接性:オーステナイトとフェライトの二相組織を持つため、溶接性が比較的良好ですが、フェライトとオーステナイトのバランスが崩れないように注意が必要です。特に、溶接後の冷却速度や熱入力が影響しやすいです。
- 具体的な溶接技術:溶接後のフェライトとオーステナイトの比率を適切に保つために、溶接中の熱管理が重要です。通常、溶接後の熱処理は不要ですが、厚肉材の場合は追加の熱処理が推奨されることがあります。
析出硬化系ステンレス鋼(例:SUS630)
- 溶接性:溶接後の熱処理が必要です。溶接直後は柔らかく、その後、特定の温度範囲で熱処理することで硬化します。このため、溶接後の熱処理プロセスが非常に重要であり、溶接の際には適切な技術が求められます。
- 具体的な溶接技術:溶接後に固溶化処理を行い、その後、時効処理で硬化させます。これにより、強度と耐久性が向上します。
各ステンレス鋼種に応じて、適切な溶接技術とプロセスを選択することが、製品の品質と耐久性を確保するために重要です。
鉄とステンレスの使用用途の違い
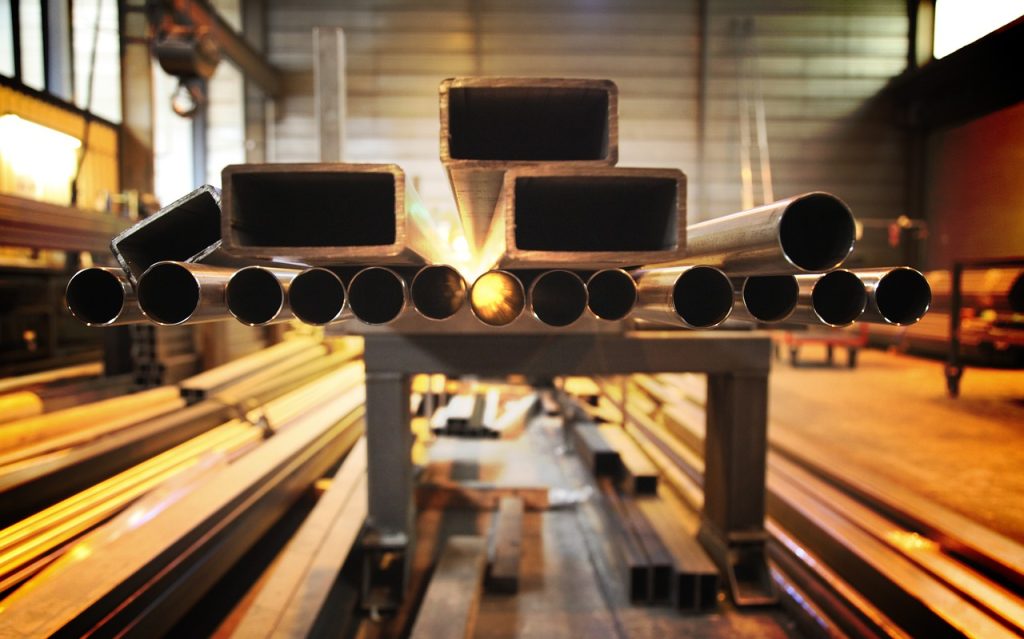
鉄とステンレスは、どちらも広く利用されている金属ですが、その特性に応じて使用用途が異なります。どのように影響を与えているかを詳しく見ていきます。
鉄の主な使用用途とその理由
鉄はその高い強度と耐久性から、多くの産業で幅広く使用されています。 まず、建築分野においては、鉄筋コンクリートや鉄骨造の建物に使用され、建物の骨格を支える材料として重要です。 鉄は、塑性変形がしやすいため、さまざまな形に加工されやすく、建築デザインにも対応できるからです。
次に、製造業では、機械部品や工具、車両のフレームなどに鉄を使用します。 その強度と耐久性により、機械の長寿命化や信頼性の向上が期待できるからです。 また、鉄は比較的安価で手に入る素材であるため、コストパフォーマンスも高いです。 これらの理由から、鉄は非常に多くの場面で使用されているのです。
ステンレスの主な使用用途とその理由
ステンレスはその錆びにくさと耐久性から、特定の用途で重宝されています。 例えば、医療分野では、手術器具や医療用器具に使用されます。 これにより、器具が長期間にわたり清潔に保たれることができるのです。
食品加工機器の製造にもステンレスが使われます。 食品に触れる部分が錆びないことで、衛生面を維持できるのが理由です。 また、家庭用器具やキッチン用品としてもステンレスは非常に人気があります。 このように、ステンレスはその特性から、衛生が求められる場面や錆びにくさが求められる場面で主に使用されています。
ステンレス鋼の衛生規格と基準
衛生面での使用に際して、ステンレス鋼には厳格な規格と基準が設けられています。食品加工機器に使用されるステンレス鋼は、国際的に認められた規格であるISO 22000や**HACCP(Hazard Analysis and Critical Control Points)**に適合している必要があります。これらの規格は、食品の安全性を確保するために、機器が微生物の繁殖を抑制し、容易に清掃・消毒可能であることを求めています。
また、医療分野においては、ISO 13485という品質管理システム規格に基づいて、ステンレス鋼製の医療機器が設計・製造されます。この規格は、医療器具が無菌状態を維持し、感染リスクを最小限に抑えることを保証します。さらに、ASTM F899は、医療器具用のステンレス鋼材に関する標準規格であり、材料の化学成分や機械的特性を定めています。
これらの規格と基準に適合するステンレス鋼は、耐腐食性、非磁性、及び高強度といった特性を持つことから、医療や食品業界において不可欠な素材となっています。そのため、ステンレス鋼は、衛生管理が厳しく求められる現場での使用に最適な選択肢です。
まとめ
鉄とステンレスは、それぞれ異なる特性を持っており、用途に応じた選定が必要です。鉄は高い強度と加工性を持ち、コストパフォーマンスに優れていますが、耐食性に欠けるため表面処理が必須です。一方、ステンレスは優れた耐食性と強度を持つため、過酷な環境下でも安心して使用できますが、加工には注意が必要です。それぞれの特性を理解し、最適な材料を選ぶことが、精密部品の品質を確保するために重要です。
お問い合わせ
弊社製品、加工についてのお問い合わせは、こちらで受付しております。
各部門のスペシャリストが、ご質問にお応えします。
電話
0574-54-2231
(平日 8:15~17:15)
FAX
0574-54-2235