- 2024/07/30
-
切削加工の送り速度と表面粗さ(面粗度)の関係と計算方法
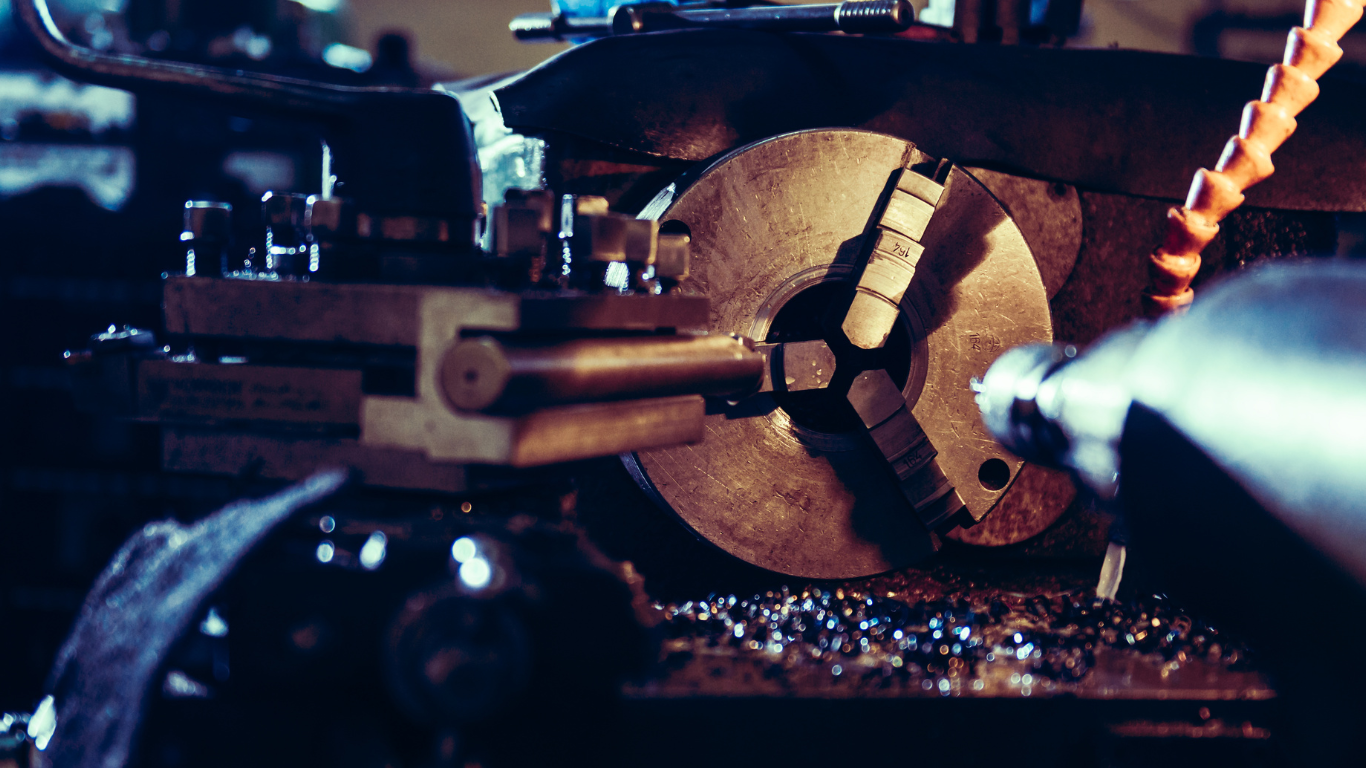
切削加工において、送り速度は加工効率や仕上がりを左右し、過剰な送り速度は表面粗さの悪化を招くことがあります。
本記事では、送り速度と表面粗さ(面粗度)の詳細や、「送り速度と表面粗さ(面粗度)の関係性」、「表面粗さ(面粗度)が悪化しないための対策」までを詳しく解説します。内容を理解し、最適な加工条件を見つける手助けとなるでしょう。
目次 [hide]
送り速度とは
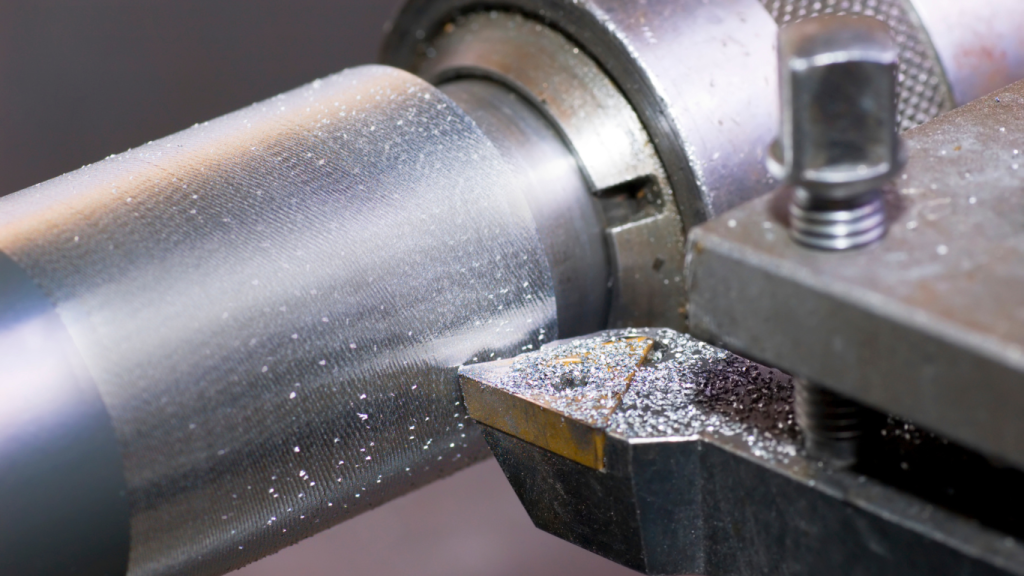
送り速度とは、工作機械や工具が移動する速度のことを指します。この速度は加工の精度や表面の仕上がりに大きく影響します。適切な送り速度を選定することで、高品質な加工を実現します。
送り速度が一定でないと加工に不具合が生じることもあります。送り速度の調整は、加工する素材や使用する工具の種類に合わせて行うことが求められます。
送り速度と送り量の違い
送り速度と送り量は似ているようで異なる概念です。送り速度は工具が素材を加工する速度を指しますが、送り量は主軸一回転当たりの刃物の移動量を表します。
例えば、送り速度が速くても、送り量が少ないと加工に時間がかかります。逆に、送り速度が遅くても、送り量が多ければ効率良く加工が可能です。そのため、送り速度と送り量のバランスが重要とされるのです。
更に、送り速度が速過ぎると加工中に工具が過剰に摩耗することがあります。一方、送り量が多すぎると加工された素材の表面が荒れやすくなります。これらの要素を考慮し、送り速度と送り量を最適に設定することが求められます。
送り量の計算
1刃あたりの進行量(mm/tooth)、1分間の進行量(mm/min)、または被削材の1回転あたりの進行量(mm/rev)として表されます。旋削加工では、被削材の回転を基準にし、以下の式で計算します。
旋削の場合: 1分あたりの送り速度 F(mm/min) = 1回転あたりの送り f(mm/rev) × 主軸回転数 N(rpm)
フライス加工の場合: 1分あたりの送り速度 F(mm/min) = 1刃あたりの送り f(mm/tooth) × 刃数 t(または n)× 主軸回転数 N(rpm)
表面粗さ(面粗度)とは
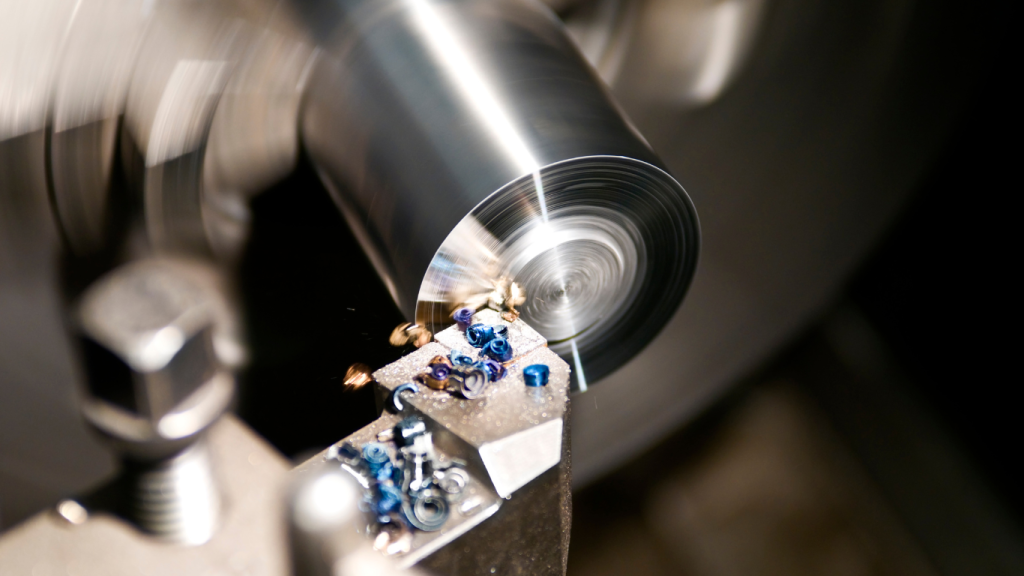
表面粗さ、または面粗度とは、物体の表面の微細な凹凸やざらつきを示す尺度のことです。この特性は製品の性能や寿命、見た目に影響を与えます。
一般的には、製造業において重要な要素であり、高精度の加工が求められる場合は特に注意が必要です。表面粗さを評価する際の尺度や基準は、産業分野や用途によって異なりますが、主に数値で表現され、測定のための専用機器が使用されます。
表面粗さ(面粗度)の測定方法
表面粗さを測定する方法はいくつかあります。代表的な方法のひとつは、コンタクト式の触針式プロフィルメータです。この技術では、微細な針を表面に走らせ、その動きによって得られるデータを解析して、表面の凹凸を確認します。コンタクト式の他には、非接触型の方法もあります。
例えば、光を用いた光学的測定方法です。この手法では、レーザーや顕微鏡を用いて表面をスキャンし、その反射光のデータから表面形状を解析します。それぞれの方法には、メリットとデメリットがあるため、用途や必要な精度に応じて適切な方法を選択します。
Rz・最大高さ
Rzは、表面粗さの指標の一つで、最大高さを示します。この指標は、基準面から最も高い点と最も低い点の差を計測することで得られます。このような計測により、表面の粗さがどれほど極端であるかを評価します。
一般的には、Rzが高いほど表面粗さが大きいとされます。Rzは特に、製造業や機械工業で広く用いられており、高精度の部品や製品を製造するためには、Rzの数値管理が重要です。重要なデータであるため、常に正確な測定と解析が求められます。
Ra・算術平均粗さ
Raは、表面粗さを評価するための代表的な指標のひとつです。算術平均粗さとも呼ばれ、正確には算術平均絶対偏差のことを指します。測定方法としては、表面の平均的な凹凸の高さを数値化したものです。
これにより、表面の滑らかさや凹凸の程度を一目で把握できます。Raは特に、表面の平均的な状態を評価するために用いられ、他の指標と比べても使い勝手の良い指標であることが特徴です。これは、製品の性能評価や品質管理において非常に有効なデータとなります。
Rq(Rms)・二乗平均平方根粗さ
Rq、またはRmsは、二乗平均平方根粗さを示す指標です。この指標は、表面の微細な凹凸の平均的な高さを評価します。具体的には、表面の高さデータを平方し、その平均値の平方根を取る計算方法になります。
Rqは、Raと同様に表面の平均的な粗さを評価する方法ですが、より詳細なデータを提供します。そのため、高精度な表面評価が必要な場合には特に有効です。製造業や検査工程での品質管理など、Rqの数値は多くの現場で活用されています。
送り速度と表面粗さ(面粗度)の関係性

送り速度と表面粗さは、加工の品質と効率に大きな影響を与える要因です。送り速度が速いほど、加工時間が短くなりますが、表面粗さが悪化しやすくなります。
一方、送り速度が遅いと、時間はかかりますが、より滑らかな表面となります。そのため、適切なバランスを見つけることが重要なのです。
送り速度の速さが表面粗さ(面粗度)に与える影響
送り速度が速いと、材料を早く削ることになります。その結果、切削面に微小なざらつきが生じることが多く、表面粗さが悪化する原因となります。また、工具自体の負荷が増すため、摩耗が早く進み、工具寿命が短くなるリスクもあります。従って、超高速での加工は高リスクです。
一方で、送り速度を遅くすると、切削工具が材料をゆっくりと切削します。この結果、表面は滑らかに仕上がりやすくなり、表面粗さが低減されます。また、工具への負荷も軽減されるため、より長い寿命が期待できるでしょう。しかし、加工時間が大幅に増えるため、生産効率が落ちる可能性もあります。
送り速度と表面粗さ(面粗度)のバランスを取る方法
送り速度と表面粗さの最適なバランスを見つけるためには、試作と調整を繰り返すことが必要です。具体的には、切削条件や使用する材料、工具の種類によって異なる最適な送り速度を見つけ出すことが重要です。
また、コンピュータシミュレーションや自動制御技術を活用することで、より精度の高い調整が可能になります。最適なバランスを見つけることで、高品質かつ効率的な加工が実現できます。
表面粗さ(面粗度)が悪化すると?
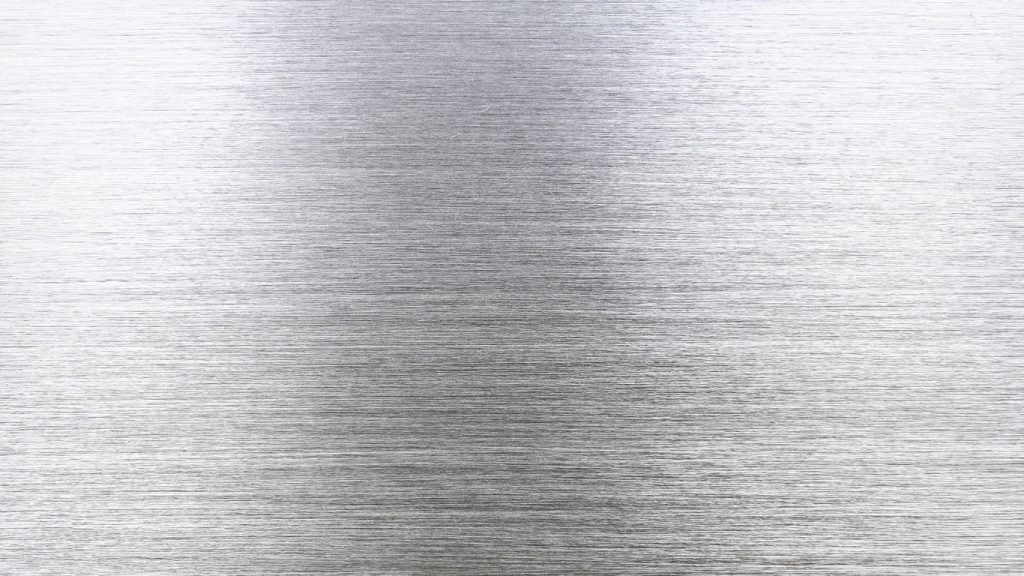
表面粗さが悪化すると、製品の品質や性能に大きな影響を及ぼします。例えば、加工不良が発生しやすくなり、製造工程での歩留まりが低下することがあります。
また、表面の金属光沢が褪せて見栄えが悪くなるだけでなく、摩擦抵抗が増加して部品の寿命が短くなることも考えられます。さらに、気密性や油密性が低下することで、流体漏れや圧力損失が発生する可能性があります。
加工不良
表面粗さが悪化すると、加工不良が発生しやすくなります。特に、切削加工では、工具と材料の間に適切な摩擦が得られず、加工面が滑らかにならないことが多いです。こうした不良は、製品の精度を大きく損ないます。
また、不均一な表面のため、部品同士の組み合わせの際に隙間が生じることがあり、組立不良に繋がる可能性があります。さらに、加工時間が長くなり、生産効率が低下することも懸念されます。
切削面の金属光沢が褪せる
表面粗さが悪化すると、切削面の金属光沢が褪せることがあります。光の反射が不均一になり、美しい光沢を失うからです。これにより、製品の見栄えが悪くなり、市場での評価が低下することがあります。
さらに、光沢が褪せた表面は、酸化や腐食のリスクが高まります。結果として、製品の耐久性が低下する可能性があります。このような品質低下は、顧客満足度にも影響を与えるでしょう。
摩擦抵抗が大きくなる
表面粗さが増すと、摩擦抵抗も大きくなります。接触面積が増えることで摩擦力が高まるためです。これにより、機械部品の可動部分がスムーズに運動しなくなり、エネルギー効率が低下します。
また、摩擦熱が発生しやすくなり、部品の劣化が進行するリスクがあります。特に、高速で運動する部品にとっては、摩擦抵抗が重要な問題となります。結果として、機械全体の性能が低下する可能性が高いです。
気密性・油密性の悪化
表面粗さが悪化すると、気密性や油密性が著しく低下します。凹凸が大きいため、密着性が損なわれるからです。これにより、流体漏れが発生しやすくなります。
例えば、シールやパッキンの性能が低下し、流体が外部に漏れることがあります。同様に、圧力が一定に保てないため、機械の動作が不安定になることもあります。また、油膜が均一に形成されないことで、機械部品の摩耗が進む可能性があります。
表面粗さ(面粗度)が悪化しないための対策
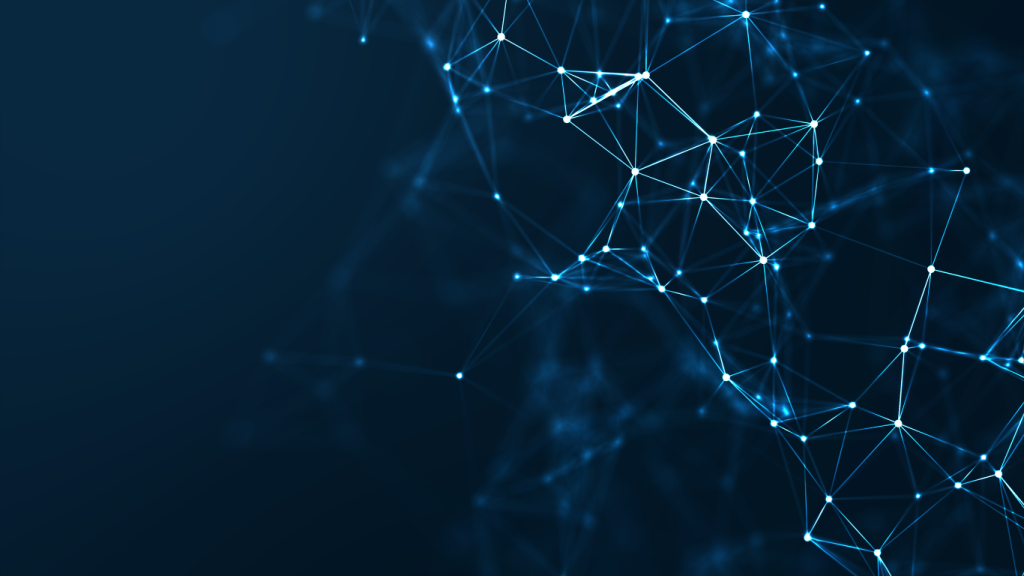
表面粗(面粗度)の悪化を避けるためには、加工技術に関する正しい知識が欠かせません。ここでは、表面粗さ(面粗度)が悪化しないための対策をご紹介します。
ワイパーインサートの選定
ワイパーインサートは切削過程での微細な振動を抑える役割を果たします。最適なインサートを選定する場合には、作業材の特性や加工条件を考慮することが不可欠です。それによって、表面粗さの悪化を未然に防ぐことが可能になります。
さらに、ワイパーインサートの刃先形状やコーナRも選定のポイントです。これにより、切削抵抗を低減させ、滑らかな表面を実現することができます。つまり、材料に応じた最適なインサートを使用することで、加工品質を向上させることができるのです。
最適な工具の選定
適切な工具を選定することは、表面粗さに大きく影響します。まず、コーティングされた工具を選定することが推奨されます。なぜなら、コーティング工具は耐摩耗性が高く、長寿命です。
また、インサートのコーナRが小さく、すくい角が大きい工具を選ぶことも重要です。これにより、切削抵抗を減少させ、加工面の滑らかさを向上させることができます。
特に、すくい角が大きい工具は切削力を分散しやすく、結果として表面粗さが改善されます。工具の選定は、作業条件や材料特性を総合的に考慮することが求められます。このため、適切な工具を選定することが、結果として高品質な加工表面を作り出すカギとなります。
切削条件の最適化
切削条件の最適化、つまり切削速度、進退量、切削深さといった条件を適切に設定することが重要です。これにより、切削時の振動や熱の発生を抑制し、表面品質を向上させることができます。同時に、材料自体の特性を踏まえた切削条件の設定も重要です。
さらに、使用する工具や冷却液も切削条件に大きく影響を与えます。適切な切削条件を見つけ出すことで、安定した加工を実現し、表面粗さを良好に保つことができます。切削条件の最適化により、高品質な仕上がりを得ることが可能です。
切削点の冷却
冷却によって切削点の温度を適切に下げることで、工具の寿命を延ばし、表面品質を良好に維持することができます。特に、高速切削では冷却が不可欠です。冷却液の適切な選定と供給方法がポイントです。
冷却液の種類や供給量、供給角度などを調整することで、切削時の熱の発生を抑えることができます。これにより、工具と作業材の温度上昇を防ぎ、表面粗さを一定に保つことができます。効果的な冷却策を取り入れることで、表面品質の向上が見込めます。
送り量を小さく
送り量の調整も、表面粗さを改善するための重要な対策です。送り量を小さくすることで、切削中の衝撃を低減し、表面に均一な仕上がりをもたらします。また、送り量が小さいと切削点の熱の発生も抑えられるので、工具の摩耗を防ぐことができます。送り量を適切に調整することが表面品質に直結します。
さらに、一定の送り量を維持することで、安定した加工が可能となります。送り量の設定は、作業材や工具の特性を考慮した上で行うべきです。これにより、高品質な表面仕上がりを実現することができます。送り量の管理は加工の精度を向上させるポイントとなります。
まとめ
送り速度や表面粗さは切削加工において製品の品質を大きく左右する要素です。適切な送り速度と送り量のバランスを見極めることで、高品質な加工表面を実現することができます。
常に切削条件を最適化し、工具の選定や冷却技術を駆使することで、製品の品質と加工効率が向上します。この理解を深め、日々の作業に役立てていただければと思います。
お問い合わせ
弊社製品、加工についてのお問い合わせは、こちらで受付しております。
各部門のスペシャリストが、ご質問にお応えします。
電話
0574-54-2231
(平日 8:15~17:15)
FAX
0574-54-2235